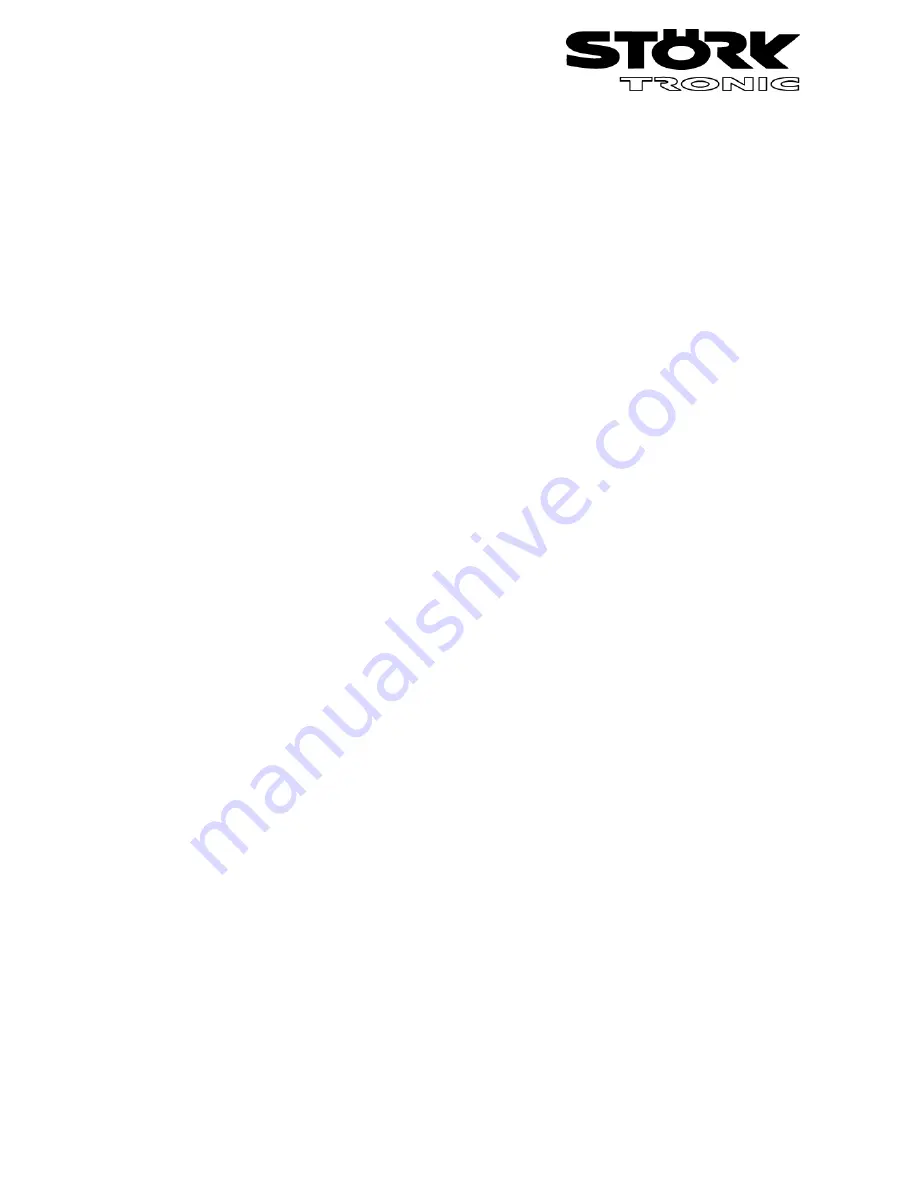
d9: Execution of defrost demand
With d9 = 0 the defrost demand will be prevented as long as the locking conditions of parameters
c0, c1 and c2 apply. With d9 = 1 defrosting starts independently of these parameters.
During defrosting there is an increase of the refrigerating chamber temperature. This can be
specially noticed if there is a high temperature when starting defrosting. With d9=2 a cooling cycle
takes place before defrosting for the temperature difference to the setpoint set with dC.
If cooling takes to long the time limit set with dF applies.
db: Time base defrost cycle
This parameter changes the time base for the defrosting cycle. With parameter set to “1” hours
become minutes and minute become seconds. This allows a quick control and monitoring of the
refrigeration plant during installation and maintenance.
dC: Temperature decrease before defrosting
only effective if d9=2
dF: Time limitation for temperature decrease
see d9 and dC.
dU: start manual defrosting (only required in combination with data logger)
With dU = 1 the defrost interval is started prematurely. The following automatic defrost takes place
after the time period d0 (synchronisation of the defrosting)
dH: Waiting after defrost
This parameter is used for open cooling systems when several controllers control one cold room.
By linking the network variables a common defrost start can be realised. The parameter dH pre-
vents the controllers from switching back from defrosting to cooling mode at different times. If dH is
set to “1” the starting of the compressor is delayed until the time “d3” (defrosting time limit) expires.
dU: start manual defrosting (only required in combination with data logger)
With dU = 1 the defrost interval is started prematurely. The following automatic defrost takes place
after the time period d0 (synchronisation of the defrosting)
Defrosting in a network
A central defrosting by means of the integrated real time clock is possible in different ways:
1. via network variables:
Together with a suitable linking tool these variables permit to realise any controller
configuration.
2. via explicit messages (Störk-Tronic protocol):
The number of connected slaves can be set with parameter L2 (“0” = no network defrosting).
Their addresses start from the one of the master controller (“L0”) upwards. If the master has
the address “1” the first slave will have “2” and so on …
If the master receives a defrost demand it will pass it to all slaves. If a slave doesn’t answer the
display indicates the message “F90”. Please check the network connection in this case.
In case of defrosting during network operation the automatic internal defrosting of the slaves
should be switched off (“d0”=0).
Any manual defrosting has no effect on the other networked controllers.
A0: Hysteresis for alarm contact
The hysteresis of the alarm contact is asymmetrically, set downward at the maximum alarm value
upward at the minimum alarm value.