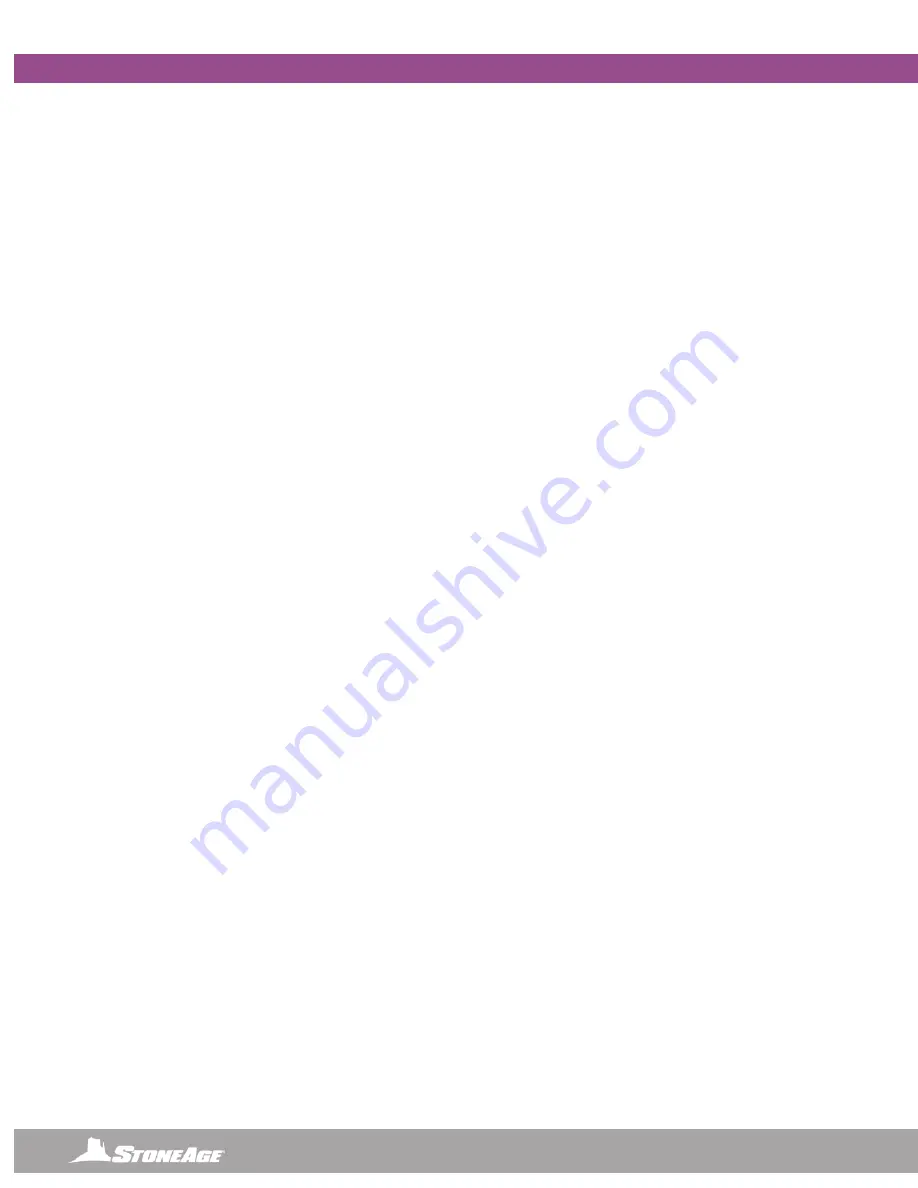
24
866-795-1586 • WWW.STONEAGETOOLS.COM
CONTROL PANEL FUNCTIONS
HOSE FEED LEVER-
•
The
HOSE FEED LEVER
will move the hose in the forward (feeding) and reverse (retracting) directions. The
OFF
position is at the spring
centered middle position and will stop the Drive Rollers from turning. The speed controls are located on the AUTOBOX
®
(ABX-2L-V2) Hose
Tractor. Speed is independently adjustable for Forward/Reverse. Minimum speed is .2ft/sec (6 cm/sec). Maximum speed is 3.0ft/sec
(914 mm/sec).
POSITIONER CONTROLS-
•
UP/DOWN
will move the PRODRIVE Tractor (ABX-PRO) up and down the tube face bundle. Push forward to move the assembly UP,
release to STOP the motion, push down to move the assembly down.
•
LEFT/RIGHT
will move the PRODRIVE Tractor (ABX-PRO) from side to side along the tube face bundle. Push left to move the assembly
to the LEFT, release the lever to STOP the motion, push RIGHT to move the assembly to the right.
MOMENTARY PNEUMATIC DUMP CONTROL-
•
To use the
DUMP CONTROL
, hold it in the FORWARD position to route the high-pressure water to the tool. Release the knob to divert
the high-pressure water away from the tool.
•
To de-energize the system, release the
HOSE FEED LEVER
and rel ease the
MOMENTARY PNEUMATIC DUMP CONTROL.
This will stop the Drive Rollers from moving and reroute the high-pressure water away from the AUTOBOX
®
(ABX-2L-V2) Hose Tractor.
TEST RUN PROCEDURE
•
Perform the
PRE-RUN SAFETY CHECK (SEE PAGE 6)
.
•
Ensure appropriate Collet is installed and hose clamp pressure is set at 20-30psi (.14-.20 MPa)
•
Operate the high-pressure hose and waterjet tool at full pressure to test the clamp force. Proper clamp force will provide good control of the
hose in forward and reverse directions.
•
Adjust the hose feed speed controls. Proper forward and reverse speeds will vary, depending on the type of material being removed and the
tube size. Adjustment of the hose feed speed controls may be necessary during operation in order to optimize cleaning and overall productivity.
•
Operate the high-pressure water at full pressure and use the
MOMENTARY PNEUMATIC DUMP CONTROL
to verify that the dump valve is
working properly.
RUN PROCEDURE
•
After assembling and verifying, the AUTOBOX
®
(ABX-2L-V2) Hose Tractor system is ready for operation.
•
Once all hose connections have been secured and verified, it is recommended to flush the hoses and verify the dump valve is working properly
before installing the Banshee tools.
•
After flushing the hoses, install the Banshee tools and insert both tools into the back of the AUTOBOX
®
(ABX-2L-V2) Hose Tractor. It may be
necessary to twist the hoses slightly as the tools and hose ends are manually pushed through the Drive Rollers.
•
Once the Banshees are inside the Guide Tubes, install the Collet (anti-withdrawal protection).
The appropriate Collet must be verified,
installed, secured, tested, and performance confirmed before operating at high pressure.
•
Adjust the clamp pressure to 20-30 psi. (.14-.20 MPa). Align the Guide Tubes with an open set of tubes in the heat exchanger bundle.
•
Feed forward and advance the hoses into the tube bundle at low pressure and wait for the tools to exit the far side of the heat exchanger.
•
Set the forward hose stops in the desired position to ensure the entire tube is cleaned, but that the hose crimp does not fully exit the tube.
•
Retract the hoses into the Guide Tubes.
•
Close the dump and gradually increase the pump to the desired operating pressure.
•
Feed forward and advance the hoses into the tube bundle. Dump and make any desired changes to forward and/or reverse operating speeds.
•
If the Drive Rollers are slipping excessively, increase the clamp pressure. It is recommended to operate the clamp pressure as low as possible
without excessive slippage. Optimal clamp pressure is achieved when the Drive Rollers slip ½ to 1 full rotation after hitting the hose stops (for-
ward) or the Collet engages the hose crimp (reverse). It is recommended to use hose supplied with the secondary crimp so the (anti-withdrawal
protection) Collet does not impact the pressure containing crimp.
•
Operate the left/right and up/down positioner functions to begin high pressure cleaning at the preferred location on the tube bundle.
•
Always align the Guide Tubes as closely as possible with the heat exchanger tubes before advancing the hoses
•
When operating the AUTOBOX
®
(ABX-2L-V2), an obstacle or restriction within a heat exchanger tube may be encountered. When this occurs,
the AUTOBOX
®
(ABX-2L-V2) is designed to slow and stall the air drive motor, stopping the advancement of the hose, lance, and Banshee tool.
The operator should stop forward feed and reverse the lance feed direction, backing the tool away from the obstruction. Repeat the back and
forth operation, until the resistance or obstruction is cleared via the cleaning action of Banshee tool at the end of the hose. The AUTOBOX
®
(ABX-2L-V2) is not designed for Drive Roller slip. If slippage occurs, gradually increase the clamp force using the
HOSE CLAMP PRESSURE
REGULATOR
on the Control Box
.
OPERATION