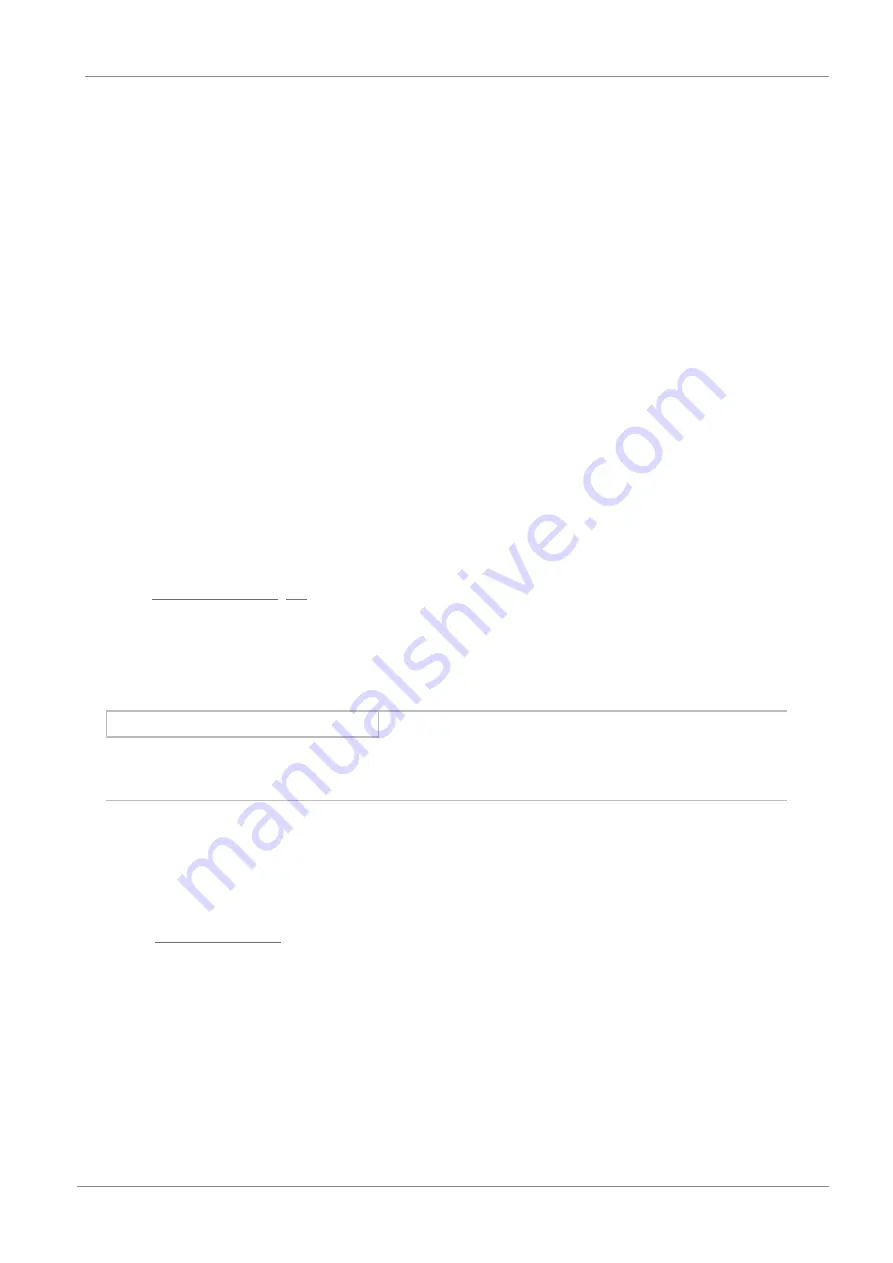
STOBER
10 | More on PROFINET?
11/2019 | ID 442710.03
43
10.3
Communication
An IO controller controls and regulates communication with IO devices in the PROFINET network. In the process, the
controller transmits cyclical process data (PZD), such as control information, to the devices and receives current state
signals from them.
In addition, IO controllers and IO devices acyclically exchange data that is not time-critical, such as configuration parameter
values or one-time events, using parameter channel data.
Both communication services run in parallel, with transmission of cyclical PZD having higher priority. In each cyclical
exchange of data, an acyclical frame is injected as needed.
10.3.1
Cyclical communication: Process data
Process data (PZD) objects are normally data that is required for controlling and observing the ongoing process, such as
target positions, travel velocities or acceleration information.
It is generally used for data exchange in real time. It also gives you simultaneous access to multiple drive parameters.
Process data is exchanged quickly and cyclically with a high priority over the RT real-time channel.
For PROFINET IO, the cyclical data traffic relies directly on the MAC address of a device and does not contain any IP
addresses. This keeps the overall length of a data packet relatively small.
The direction of data flow is of critical importance in this data transfer. From the perspective of the respective nodes, a
distinction is made between receive PZD
(RxPZD) and transmit PZD (TxPZD).
The specific communication elements that are sent and received in specific PZD can be freely selected. The length and
structure of process data are defined as part of project configuration by means of the process data modules (see the
chapter
Currently, 18 parameter values with a maximum total length of 72 bytes (36 words) can be exchanged between the IO
controller and IO device per drive controller.
10.3.2
Acyclical communication: Parameter channel data
Information
If you use the example project provided by STOBER for programming acyclical communication services, this chapter is not
relevant in practice.
The parameter channel is used to transfer data that is not time-critical. Parameter channel data enables read and write
access to the configuration parameters of an IO device and transfers one-time events.
Parameter channel data is transmitted acyclically in ongoing cyclical PROFINET operation, without impairing PZD
communication.
This requires drive-specific acyclical communication services. You can either program them based on the RDREC and WRREC
SIMATIC
(see the following chapters) or load a STOBER-specific example project specifically tailored
to the STOBER drive controllers of the 6th generation from the download area in your TIA Portal and configure the
parameters appropriately for your system environment.