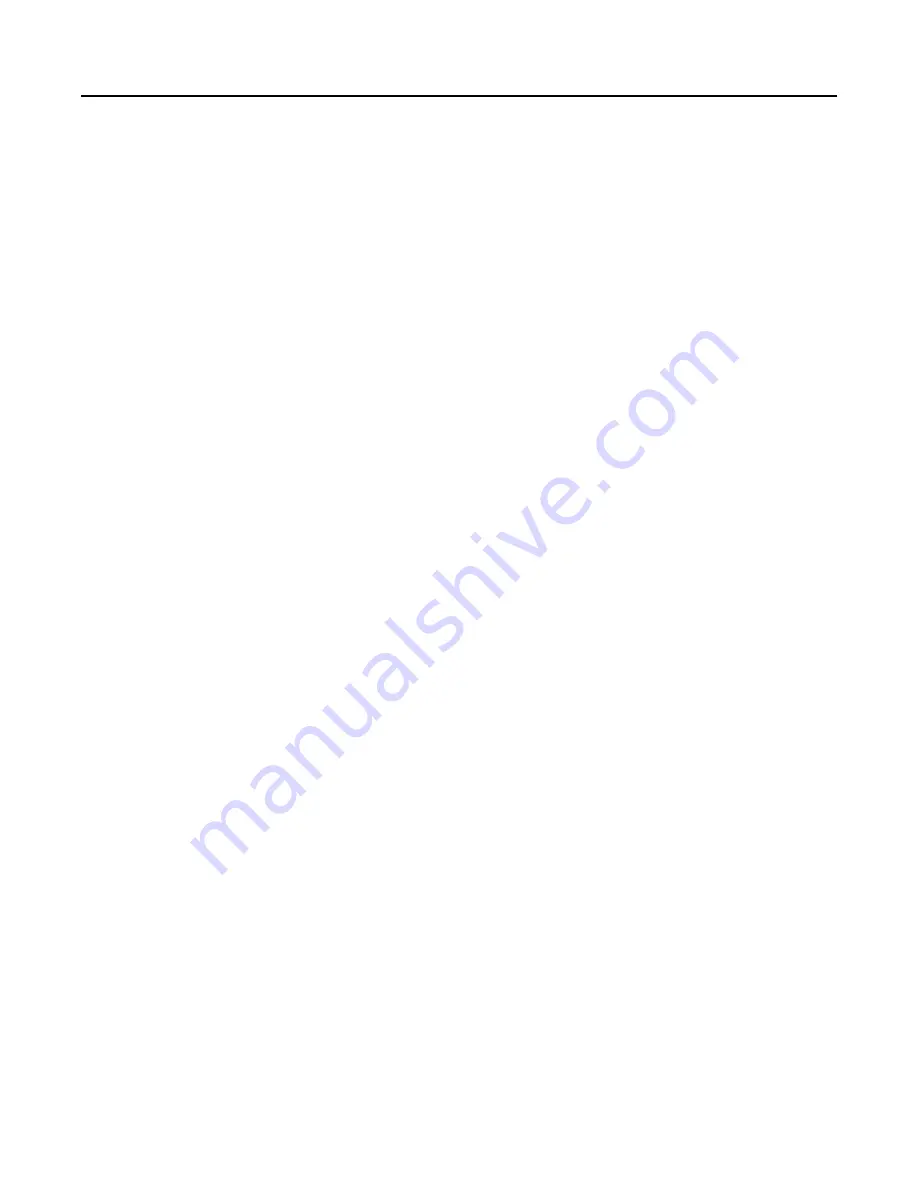
2.
Loosen vent screw (3 4 or 5) on the fuel filter.
3.
Operate hand priming pump (6). When fuel free
from air flows from the vent screw tighten the vent
screw.
4.
Loosen connection (10 or 12) at the fuel injection
pump. Refer to illustration 59 .
Note:
Fuel return line (11) may need to be removed
in order to prime the fuel system.
5.
Operate the hand priming pump. When fuel free
from air flows from the connections tighten the
connecting bolt.
6.
The engine should now be able to start. Operate
the starting motor in order to start the engine.
Note:
Do not operate the starting motor for more than
15 seconds. If the engine does not start after 15
seconds, stop and wait for 30 seconds before trying
again.
In-line Priming Pump 7
In order to identify the in-line priming pump, refer to
illustration 58 .
1.
Ensure that fuel valve (2) for the fuel filter that has
an element is in the ON position. Refer to
illustration 55 .
2.
Loosen vent screw (3 4 or 5) on the fuel filter.
3.
Operate in-line priming pump (7). When fuel free
from air flows from the vent screw tighten the vent
screw.
4.
Loosen connection (10 or 12) at the fuel injection
pump. Refer to illustration 59 .
Note:
Fuel return line (11) may need to be removed
in order to prime the fuel system.
5.
Operate the in-line priming pump. When fuel free
from air flows from the connections tighten the
connecting bolt.
6.
The engine should now be able to start. Operate
the starting motor in order to start the engine.
Note:
Do not operate the starting motor for more than
15 seconds. If the engine does not start after 15
seconds, stop and wait for 30 seconds before trying
again.
Electrical Priming Pump 8
In order to identify the electrical priming pump, refer
to illustration 58 .
1.
Ensure that fuel valve (2) for the fuel filter that has
an element is in the ON position. Refer to
illustration 55 .
2.
Loosen vent screw (3 4 or 5) on the fuel filter.
3.
Operate electrical priming pump (8). When fuel
free from air flows from the vent screw tighten the
vent screw. Switch off the electrical priming pump.
4.
Loosen connection (10 or 12) at the fuel injection
pump. Refer to illustration 59 .
Note:
Fuel return line (11) may need to be removed
in order to prime the fuel system.
5.
Operate the in-line priming pump. When fuel free
from air flows from the connections tighten the
connecting bolt.
6.
The engine should now be able to start. Operate
the starting motor in order to start the engine.
Note:
Do not operate the starting motor for more than
15 seconds. If the engine does not start after 15
seconds, stop and wait for 30 seconds before trying
again.
Fuel Transfer Pump 9
In order to identify the fuel transfer pump, refer to
illustration 58 .
Note:
In order to use the transfer pump, you must
operate the starting motor. Do not operate the
starting motor for more than 15 seconds. After 15
seconds, stop and wait for 30 seconds before
operating the starting motor.
1.
Ensure that fuel valve (2) for the fuel filter that has
an element is in the ON position. Refer to
illustration 55 .
2.
Loosen vent screw (3 4 or 5) on the fuel filter.
3.
Operate fuel transfer pump (9). When fuel free
from air flows from the vent screw tighten the vent
screw. Stop the fuel transfer pump.
4.
Loosen connection (10 or 12) at the fuel injection
pump. Refer to illustration 59 .
Note:
Fuel return line (11) may need to be removed
in order to prime the fuel system.
5.
Operate the fuel transfer pump. When fuel free
from air flows from the connections tighten the
connecting bolt. Stop the transfer pump.
6.
The engine should now be able to start. Operate
the starting motor in order to start the engine.
80
SEBU8312-03
Содержание TANVAC HDV3000
Страница 2: ...1300 998 784 STGGLOBAL NET OPERATORS MANUAL TANVAC HDV3000 Sec on 1 ...
Страница 11: ...8 4 COMPONENT IDENTIFICATION Engine Control Panel Control Panel ...
Страница 14: ...11 Water System Water pump Switch Water Pump ...
Страница 15: ...12 Water Strainer Hose Reel ...
Страница 16: ...13 Water Tank Drain Valve Lever Vacuum System Dump valve Suction Valve ...
Страница 17: ...14 Blower Vacuum ...
Страница 19: ...16 Primary Shutoff Assembly Collection Tank Interior Bag House Lid ...
Страница 20: ...17 Bag House Drain Valve Tools Water Gun ...
Страница 34: ...31 20 3000lt ELECTRIC CONTROL BOX CIRCUIT DIAGRAM 1 ...
Страница 35: ...32 21 3000lt ELECTRIC CONTROL BOX CIRCUIT DIAGRAM 2 ...
Страница 36: ...33 22 3000lt VACUUM UNIT BOTTOM RAIL ASSEMBLE ...
Страница 37: ...1300 998 784 STGGLOBAL NET OPERATORS MANUAL Cat 2 2 Opera on Manual Sec on 2 ...
Страница 137: ... Table 32 contd 100 SEBU8312 03 Reference Information Section Maintenance Log ...
Страница 141: ......
Страница 144: ...1300 998 784 STGGLOBAL NET OPERATORS MANUAL Comet Manual Sec on 3 ...
Страница 161: ...1300 998 784 STGGLOBAL NET OPERATORS MANUAL Sutorbilt R Series Sec on 4 ...
Страница 200: ...SB 7 632 Page 39 SECTION 8 PARTS LIST ...
Страница 202: ...SB 7 632 Page 41 ...
Страница 204: ...SB 7 632 Page 43 301GAE810 A Ref Drawing ...
Страница 206: ...SB 7 632 Page 45 ...
Страница 208: ...SB 7 632 Page 47 ...
Страница 210: ...SB 7 632 Page 49 303GAE810 A Ref Drawing ...
Страница 212: ...SB 7 632 Page 51 ...
Страница 214: ...SB 7 632 Page 53 ...
Страница 216: ...SB 7 632 Page 55 300GAE810 A Ref Drawing ...
Страница 218: ...SB 7 632 Page 57 ...
Страница 220: ...SB 7 632 Page 59 ...
Страница 222: ...SB 7 632 Page 61 302GAA810 A Ref Drawing ...
Страница 224: ...SB 7 623 Page 63 ...
Страница 226: ...1300 998 784 STGGLOBAL NET OPERATORS MANUAL Sutorbilt P Series Sec on 5 ...
Страница 245: ...SB 7 622 Page 12 1 PIPE STEEL 2 SCH 80 2 MED CARBON STEEL 1 2 FIGURE 9 GEAR DRIVER SK2150 ...
Страница 258: ...SB 7 622 Page 25 SECTION 8 PARTS LIST 300GAF810 B Ref Drawing ...
Страница 260: ...SB 7 622 Page 27 300GAG810 A Ref Drawing ...
Страница 262: ...SB 7 622 Page 29 300GAH810 A Ref Drawing ...
Страница 265: ......
Страница 266: ...1300 998 784 STGGLOBAL NET OPERATORS MANUAL Lofa Manual Sec on 6 ...
Страница 268: ...EP250 Panel Operation and Troubleshooting 2 463 3000 01 Rev D 23 Sep 2013 This page intentionally left blank ...
Страница 294: ...1300 998 784 STGGLOBAL NET OPERATORS MANUAL Excava on Hydro SWMS Sec on 7 ...
Страница 314: ...1300 998 784 STGGLOBAL NET OPERATORS MANUAL Pressure Cleaner Water SWMS Sec on 8 ...