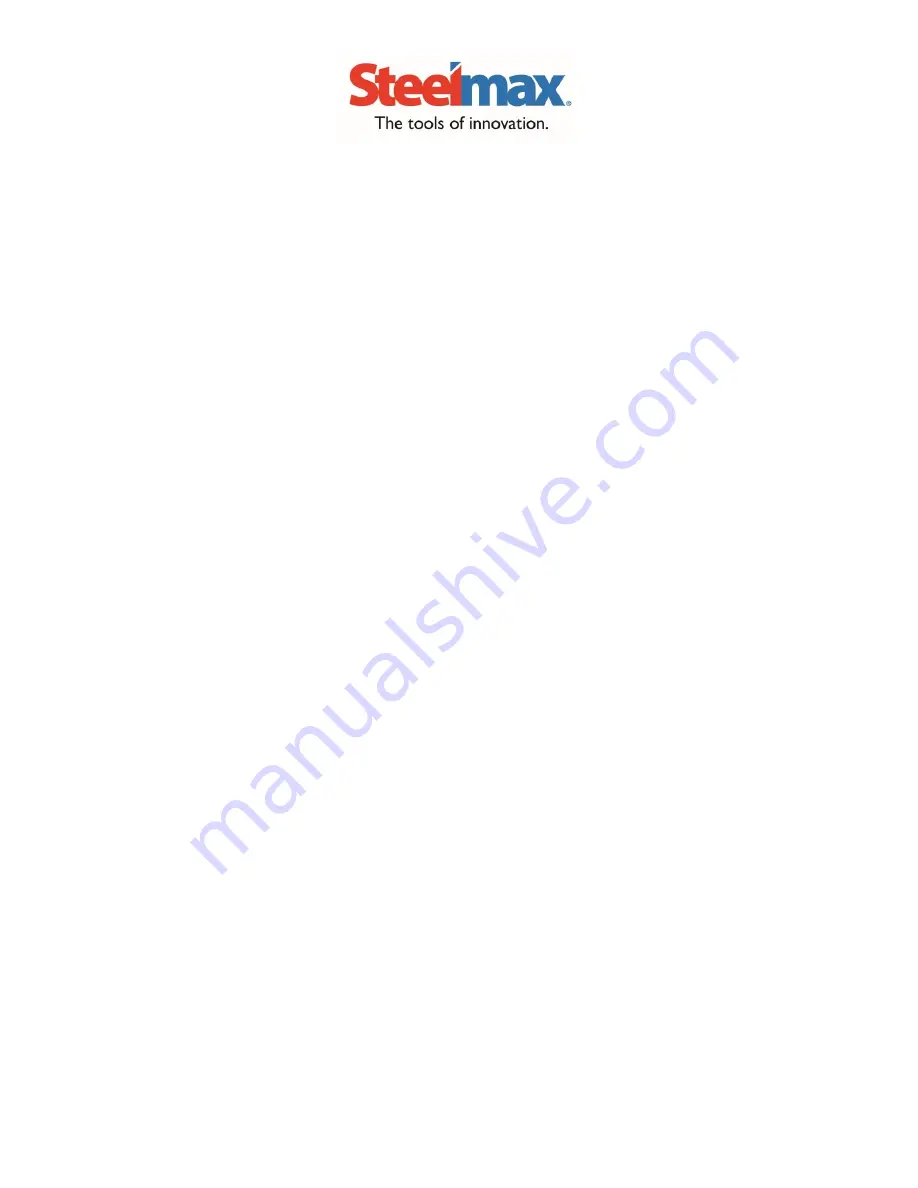
SM-S-9 XP Operator’s Manual
- ii -
2017 Version 1.01
STEELMAX LIMITED WARRANTY
Within twelve (12) months from the original date of purchase Steelmax will repair or replace any machine tool found
to be defective in materials or workmanship, provided the product working registration card has been returned to
Steelmax within thirty (30) days of the purchase date. This warranty is void if the tool being returned has been used
beyond the recommendations in this Operator’s Manual or if the machine has been damaged by accident, neglect,
improper service, or other causes not arising out of defects in materials or workmanship. This warranty does not apply
to machines and/or components which have been altered, changed, or modified in any way, or subjected to use beyond
recommended capacities and specifications. Electrical components are subject to respective manufacturers warranties.
All goods returned defective shall be returned prepaid freight to Steelmax, which shall be the buyer’s sole and
exclusive remedy for defective goods. Steelmax reserves the right to optionally repair or replace the machine with
the same or equivalent item. There is no warranty for any consumable items, including, without limitation, saw blades,
annular cutters, abrasive belts and cutting inserts. All machines must have the consumables used when the machine
failed installed to determine if the machine has been overused or if it falls under Steelmax’s warranty replacement
program for defects in material and workmanship. In no event shall Steelmax be liable for loss or damage resulting
directly or indirectly from the use of the merchandise or from any other cause. Steelmax is not liable for any costs
incurred on such goods or consequential damages. No officer, employee or agent of Steelmax is authorized to make
oral representations of fitness or to waive any of the foregoing terms of sale and none shall be binding on Steelmax.
STEELMAX RESERVES THE RIGHT TO MAKE IMPROVEMENTS AND MODIFICATIONS TO DESIGN AND
SPECIFICATIONS WITHOUT PRIOR NOTICE. IN ADDITION, STEELMAX RESERVES THE RIGHT TO
MODIFY THESE TERMS AND CONDITIONS WITHOUT PRIOR NOTICE.