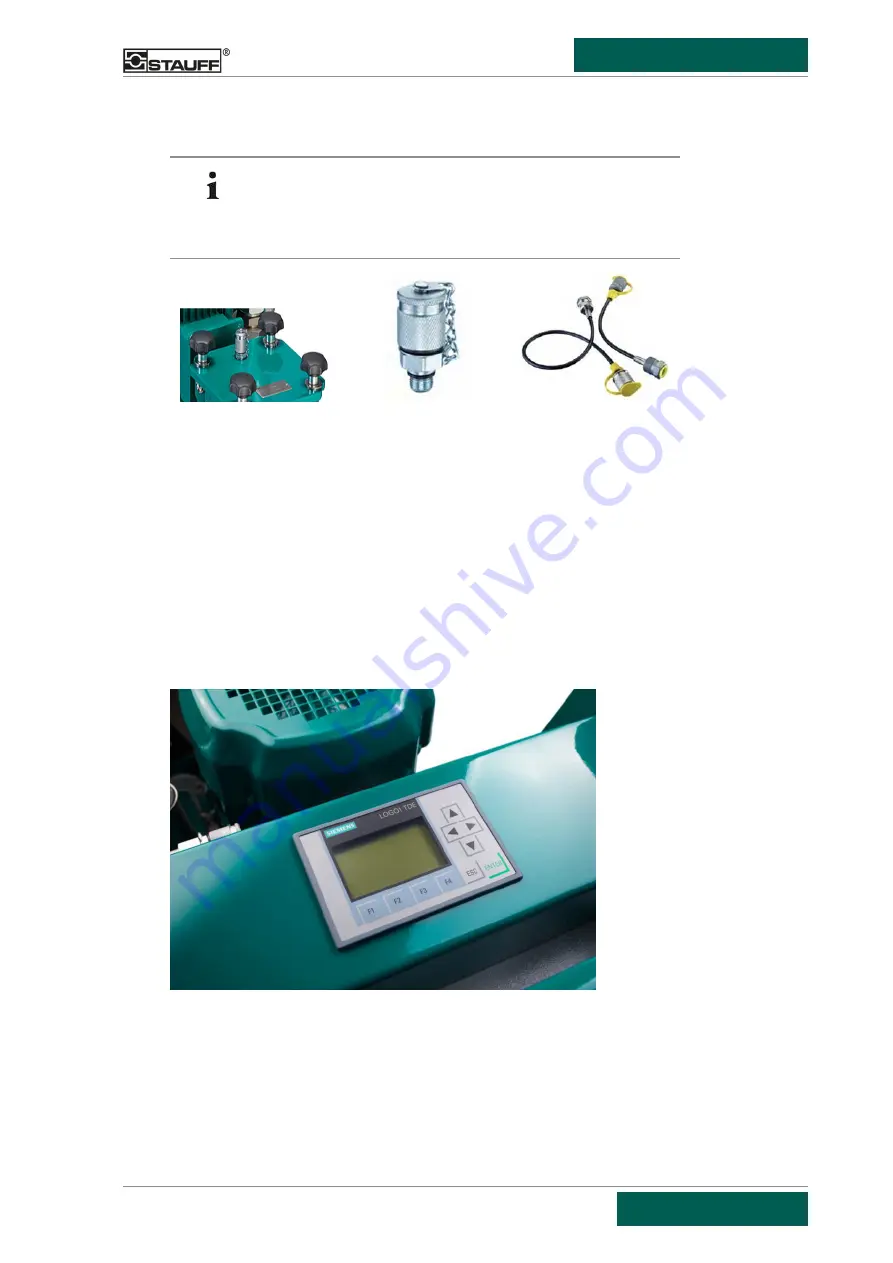
5 Installation
SMFS-U-CM-110
21 / 40
www.stauff.com
After the pump has been switched off, residual liquid can be emitted
from the hoses.
During initial commissioning and after each filter element
change, the housing has to be vented at the cover of the filter
housing using the provided STAUFF test hose (SMS) on the
already installed STAUFF test coupling (SMK).
Fig. 5: SMK position on the
housing
Fig. 6: SMK
Fig. 7: SMS
u
Please follow these steps when venting the filter housing:
1. Unscrew the protective cap of the SMK.
2. Place one side of the SMS in the tank or a suitable vessel and screw
the other side onto the SMK.
3. As soon as oil is emitted on the test hose end in the tank, the SMS
can be unscrewed from the SMK again.
5.3 Particle counter
Fig. 8: Particle counter
The filter trolley SMFS-U-CM-110 is equipped with a condition monitoring
system. This shows the purity level, operating hours, relative humidity rh in
% and the temperature of the filtered medium on the dedicated display.
In addition, a desired purity level up to which filtration is required can be
specified for the trolley. 1 minute after reaching this purity level, the filter
trolley switches off automatically.