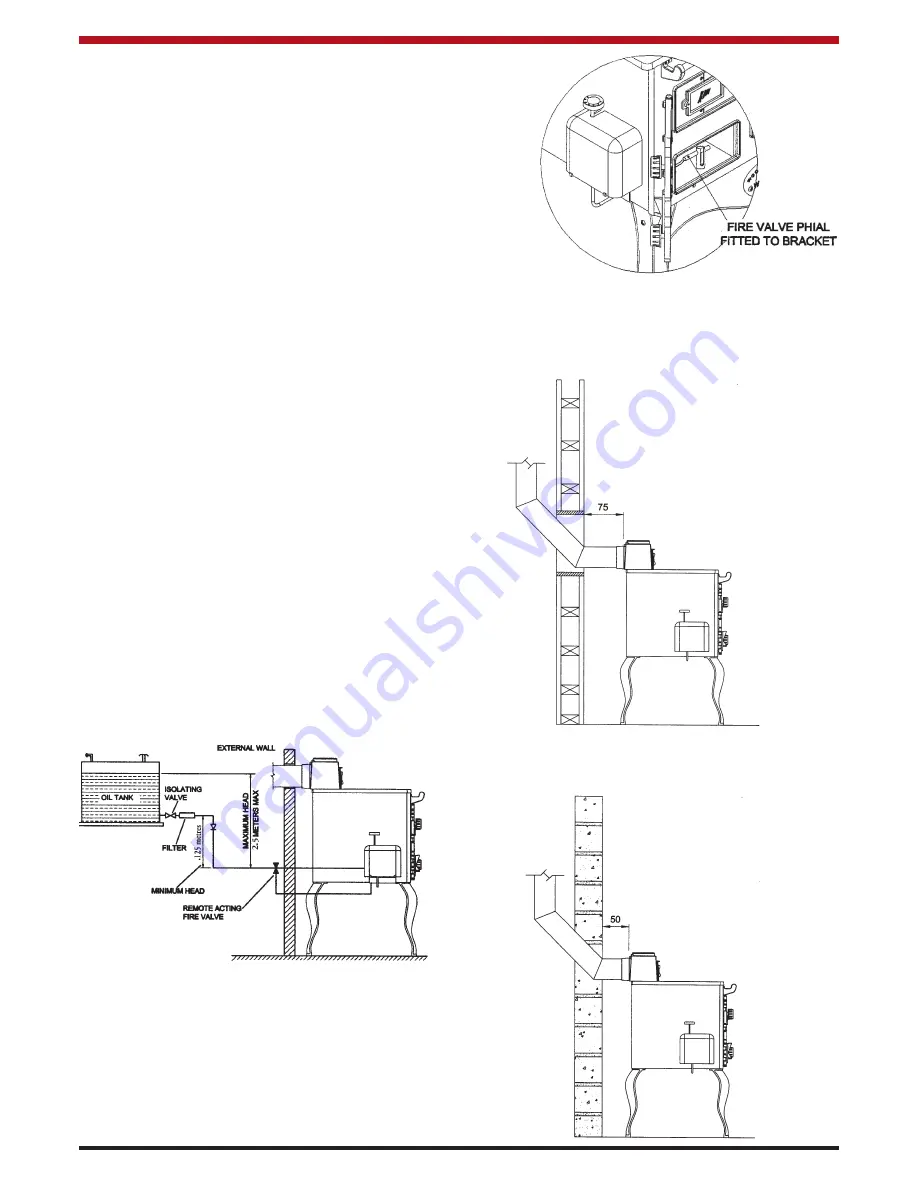
An oil filter (5 - 10 micron) and stop valve must be fit-
ted to the fuel feed line and located near the supply
tank and facilities should be provided to enable it to
be serviced without draining down the oil supply sys-
tem. (See fig.4).
At the point where the oil line enters the building, the
oil line must be fitted with an approved remote act-
ing fire valve which meets the requirements of B.S.
5410 : Part 1, fitted with the appropriate length of
capillary. The temperature rating limit should be
90
o
C. The heat sensoring phial of the fire valve
should be passed through the base of the burner
compartment and fitted through the fire valve brack-
et provided in the burner compartment (see Fig.5). It
is absolutely essential that the fire valve is located
externally and is as close as possible to the appli-
ance. For existing installations where the oil supply
is built into the structure internally, the remote acting
fire valve should be fitted where the oil supply line is
first exposed internally. This type of layout is not
recommended for new installations.
These requirements are further explained within the
following documents:
*
BS 5410: Part : Code of practice for Oil
Firing installations up to 45 kW output
capacity for space heating and hot water
supply purposes.
*
OFTEC Technical Information Book Three:
Installation Requirement for Oil Fired Boilers
and Oil Storage Tanks.
*
The Building Regulations Part J: England
Wales, Part F - Section 4 Scotland and Part
L Northern Ireland.
CLEARANCES TO COMBUSTIBLES
The minimum clearance to combustible materials
should be maintained at least 75mm (3”) from rear of
cooker (see Fig. 6).
Fig.4
Fig.5
6
Fig.6
The minimum clearance to non-combustible materi-
als should be maintained at least 50mm (2”) from
rear. (see Fig.7)
If there are other oil fired appliances connected to
the oil storage tank especially appliances with oil
pumps e.g. oil fired boilers or stoves, it is recom-
mended that a separate oil supply line is taken from
the oil tank to the cooker. The separate oil supply
line to the cooker will avoid the possibility of the
pumped appliance taking oil from the cooker burner.
A suitable shut off valve should be fitted near the
cooker and be accessible at all times.
NOTE:
Ensure that the fire valve phial is not touch-
ing any point of the base casting.
Fig.7