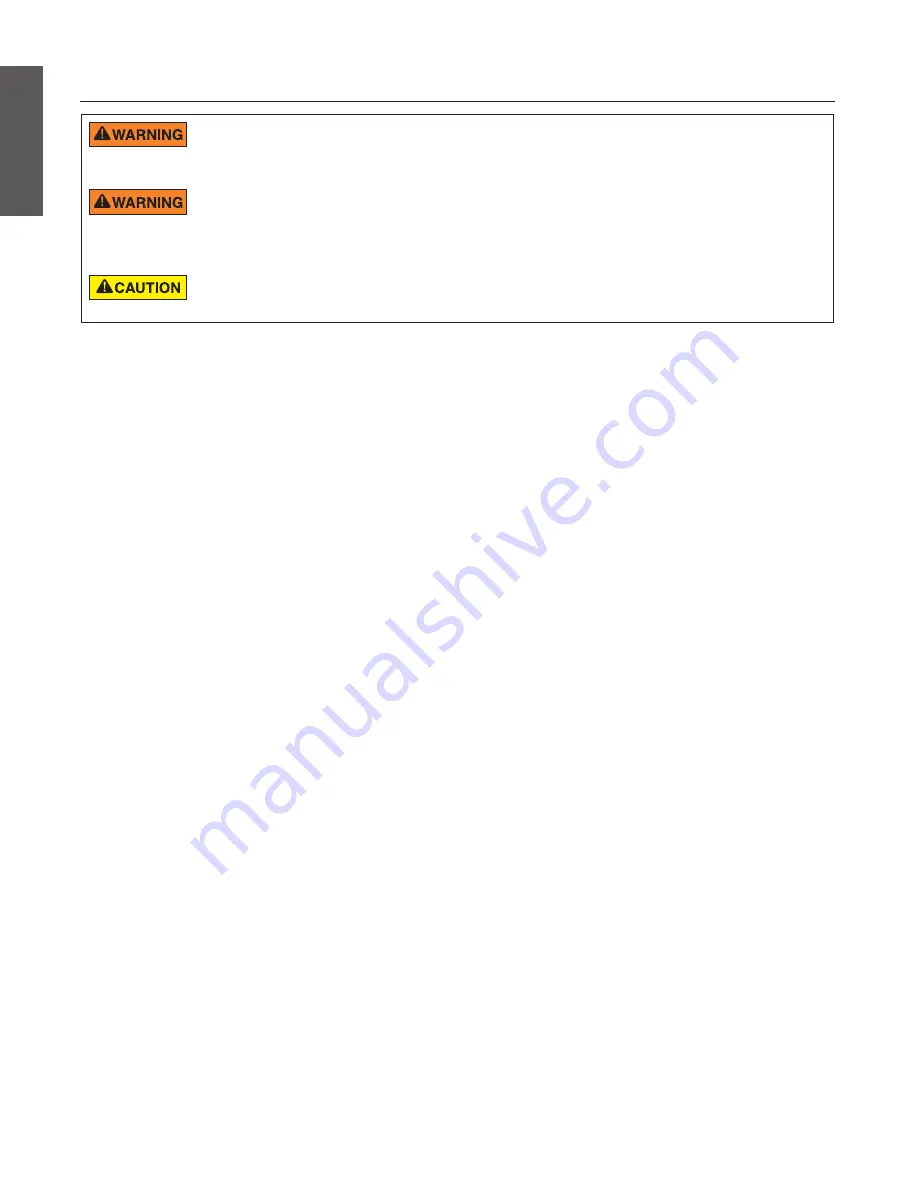
20
Care of Electric Motor
Protect from heat
1. Shade the motor from the sun.
2. Any enclosure must be well ventilated to prevent
overheating.
3. Provide ample cross ventilation.
Protect against dirt
1. Protect from any foreign matter or splashing water.
2. Do not store (or spill) chemicals on or near the motor.
3. Avoid sweeping or stirring up dust near the motor
while it is operating.
4. If a motor has been damaged by dirt it may void the
motor warranty.
5. Clean the lid and clamp, O-ring, and sealing surface
of the pump pot.
Protect against moisture
1. Protect from splashing or sprayed water.
2. Protect from extreme weather such as flooding.
3. If motor internals have become wet - let them dry
before operating. Do not allow the pump to operate if
it has been flooded.
4. If a motor has been damaged by water it may void
the motor warranty.
Note: When replacing the motor, be certain that the
motor support is correctly positioned to support the
size of motor being installed.
SERVICING
Always disconnect power to the SuperFlo
®
VS Variable Speed Pump at the circuit breaker and
disconnect the communication cable before servicing the pump. Failure to do so could result in death or
serious injury to service people, users or others due to electric shock. Read all servicing instructions before working on the pump.
open the strainer pot if pump fails to prime or if pump has been operating without water in the strainer pot. Pumps operated in
these circumstances may experience a build up of vapor pressure and may contain scalding hot water. Opening the pump may
cause serious personal injury. In order to avoid the possibility of personal injury, make sure the suction and discharge valves are
open and strainer pot temperature is cool to touch, then open with extreme caution.
Be sure not to scratch or mar the polished shaft seal faces; seal will leak if faces are damaged. The polished and lapped faces
of the seal could be damaged if not handled with care.
Pump Disassembly
All moving parts are located in the rear sub-assembly
of this pump.
To remove and repair the motor subassembly, follow
the steps below:
1. Turn off the pump circuit breaker at the main panel.
2. Drain the pump by removing the drain plugs.
3. Remove the 4 bolts that hold the main pump body
(strainer pot/volute) to the rear sub-assembly.
4. GENTLY pull the two pump halves apart, removing
the rear sub-assembly.
5. Remove the three hex head screws holding the
diffuser in position.
6. Hold the impeller securely in place and remove the
impeller lock screw by using a flat blade screwdriver
or wrench. The screw is a left-handed thread and
loosens in a clockwise direction.
7. To unscrew the impeller from the shaft, insert a
5/16 Allen key into the center of the motor fan cover
and twist the impeller counter-clockwise.
8. Remove the four bolts from the seal plate to the
motor using a 3/8 inch wrench.
9. Place the seal plate face down on a flat surface
and tap out the ceramic seal.
10. Clean the seal plate, seal housing, and the motor
shaft.
Shaft Seal Replacement
The Shaft Seal consists primarily of two parts, a
rotating member and a ceramic seal.
The pump requires little or no service other than
reasonable care, however, a Shaft Seal may
occasionally become damaged and must be replaced.
Note: The polished and lapped faces of the seal could
be damaged if not handled with care.
English