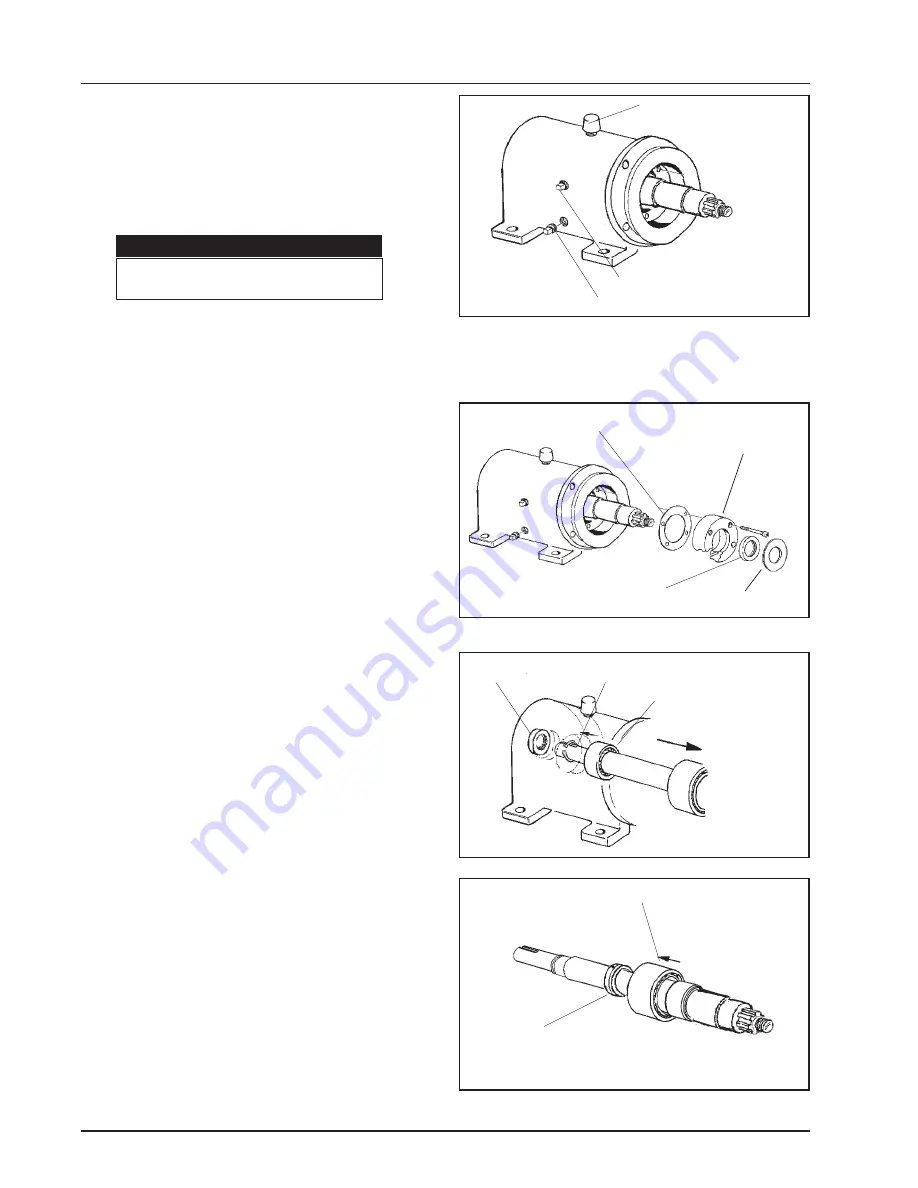
95-03028
08/2010
14
Tools required for seal and/or bearing replacement:
• Assorted hand tools including soft hammer.
• Bearing puller or press.
• Hook tool for seal removal.
• Spanner wrench for bearing retainer nut removal
• Wrench GD0019000 for rotor nut..
• Anti-seize and seal lubricating grease.
• 2 quarts DTE BB Mobil oil or equivalent.
service Preparation
1.
shut OFF and lock out all power.
2.
Remove all product and flushing from mill.
3.
Disconnect all piping to mill.
4. Remove pump anchor screws and slide gearcase
off motor coupling.
5. Place mill on sturdy work surface.
6.
Disassemble wet end of mill completely. (See
Page 11 for Disassembly)
7. Drain oil from gear case.
(Figure 18)
Front seal Replacement
(Figure 19)
1. Remove slinger.
(Pull off)
2. Remove bearing retainer assembly (front seal
inside)
(Held in place with four (4) capscrews).
4. Note seal lip position and knock out old seal, place
lubrication around new seal and press into bearing
retainer. Replace gasket, if necessary. Lubricate seal
lip and install bearing retainer and slinger.
Rear seal Replacement
(Figure 20)
1. Pull rear oil seal off drive shaft with hooked tool.
2. Place tape over shaft keyway and install new seal.
(Lubricate seal lip before sliding onto shaft).
bearing Replacement
1. Remove rear seal. Remove rear bearing retaining
ring. Press drive shaft out through front of gear case
(through rear bearing). (Figure 20)
2. Remove bearing locknut from shaft (counter-
clockwise) and press front bearing off. (Fig. 19)
3. Press the rear bearing out of the front of gear
case. (Fig. 20)
4. Clean and lubricate all parts thoroughly before
reassembling.
Do not unwrap new bearings until
ready to install.
5. Lubricate inner races and press new bearings onto
shaft. Tighten locknut on front bearing to 40 ft-lbs.
(Fig. 21)
6. Lubricate outer races and press shaft assembly
into case. Replace retaining ring and rear seal. (Fig.
17)
7. Replace mill assemblies. Torque rotor nut to 75 ft-
lbs. Refill crankcase with 2 quarts Mobil DTE BB oil.
Figure 18
Figure 19
Figure 20
Figure 21
beaRInG ReTaIneR
asseMblY
slInGeR
OIl leVel
OIl DRaIn
GaskeT
FROnT beaRInG
lOcknuT
FROnT seal
ReaR seal ReTaInInG RInG
ReaR beaRInG
GeaR case seRVIce
MaInTenance
bReaTheR caP
To avoid cutting injury, wear gloves
and handle parts carefully.
cauTIOn
Содержание Waukesha Cherry-Burrell CM
Страница 16: ...95 03028 08 2010 16 colloid mill GEAR case Figure 23 PARTS LIST ...
Страница 20: ...95 03028 08 2010 20 NOTES ...
Страница 21: ......