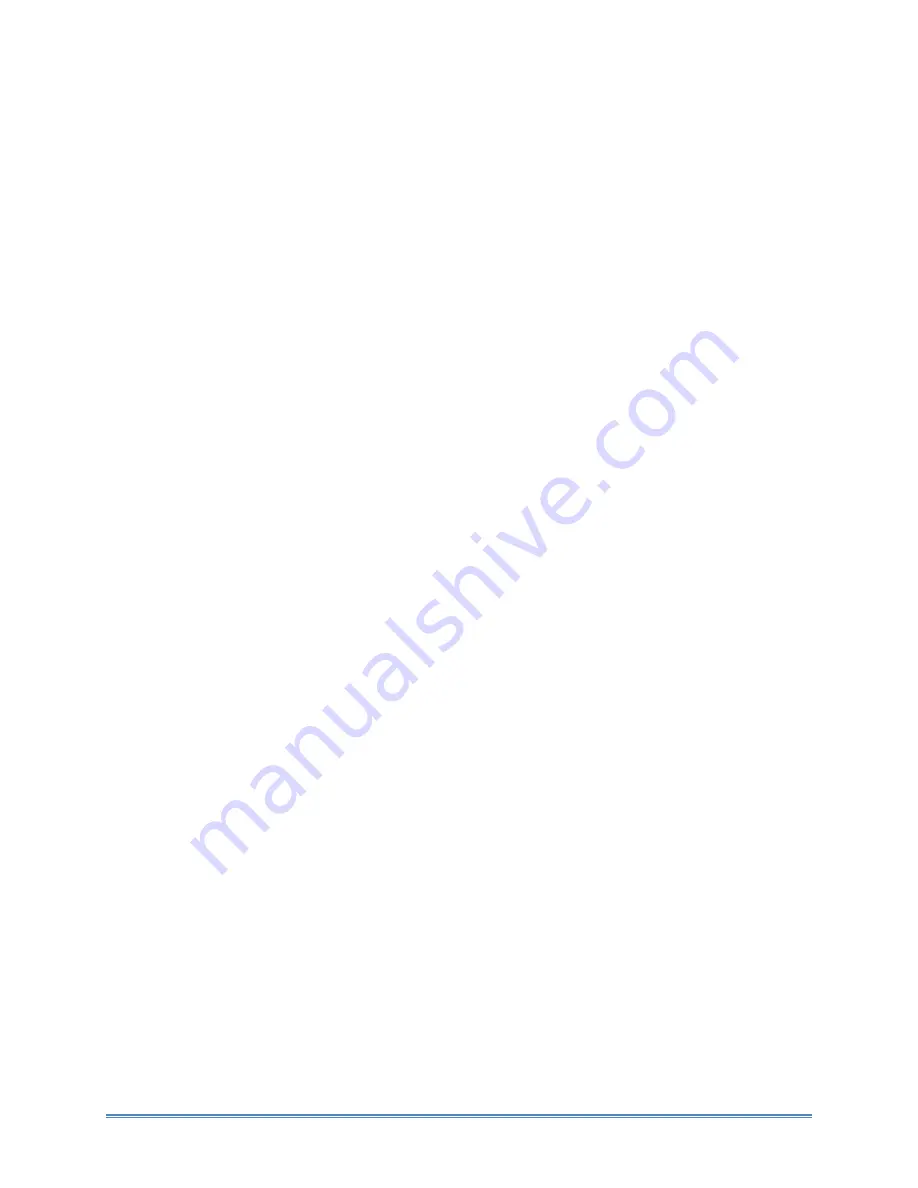
6.2.5.
ARC Counter, ARC Fault
Arcs in the HV are sensed by a current transformer in the “Low End” of the multiplier and
fed to comparator on System Control board. These comparators have a threshold that is
varied with the kV program reference level. Arc management is handled in the DSP.
The ARC signal will be received and latched by the DSP, which at Hardware speeds
disables the kV regulator with the goal of quenching the arc. This quenching is also
known as “rolling back”. The DSP is then responsibility if it is appropriate to turn the HV
back on after the arc. The DSP first increments an Arc Counter. If this is the first arc is
detected and the Arc Threshold is >1, then the DSP out an Arc Quench time roll back
interval and then re-enables the kV output. This sequence can continue until the
number of arcs detected exceeds the number of arcs programmed into the arc counter
threshold register. User can set the Arc Quench Time from 10ms to 1sec and the arc
count reset will be 100 X the Arc Quench time, 100 sec max. The arc counter threshold
setting can be set by GUI control software. Values of zero will disable the arc counter,
and allows arcs to continue without being stopped after a set count.
6.3.
Inverter Module Assembly
Inverter Module Assembly consists of EMI Filter Assembly (406577-XXX), Power Inverter
Board (460156-XXX) which includes Power Factor Correction (PFC) Circuits, DC rail voltage
filter caps(304440-XXX), L1 PFC Boost Choke ,and Temperature Switch (SW1), and cooled
by Fan B1.
When the nominal 230VAC power is applied to the Power Supply, it proceeds to EMI filter,
then arrives to the Inverter Power Board where a Line Voltage Detector monitors the AC
input line, which will issue fault signal in case the input line voltage is lower then 180VAC
and above 265 VAC. Simultaneously 230VAC arrives to the PFC circuits where the rail
capacitor bank is initial charged through the inrush current limiting resistor. When the
capacitor bank is sufficiently charged, relay activates, and its contacts short the inrush
current limiting resistor. The above-mentioned components belong to a Soft Start circuit that
limits the inrush peak current to <50A max. As soon as the SS relay is being activated, the
PFC circuit starts to operate, boosts rectified line voltage to 400VDC and supplies it to the
Half-Bridge Inverter. The DC Rail is monitored for 400 VDC +/-10% if for some reason this is
not the case, the system control board will issue a DC Rail Fault and the SS relay will be
disabled.
A Half-Bridge topology power inverter uses Insulated Gate Bipolar Transistor (IGBT) power
switches and PWM (Pulse Width Modulation) to control switching at a frequency of 25kHz.
This technique, combined with secondary resonance tuning, create Zero Current Switching
XRV SERIES
Page 24
118116-001 REV C