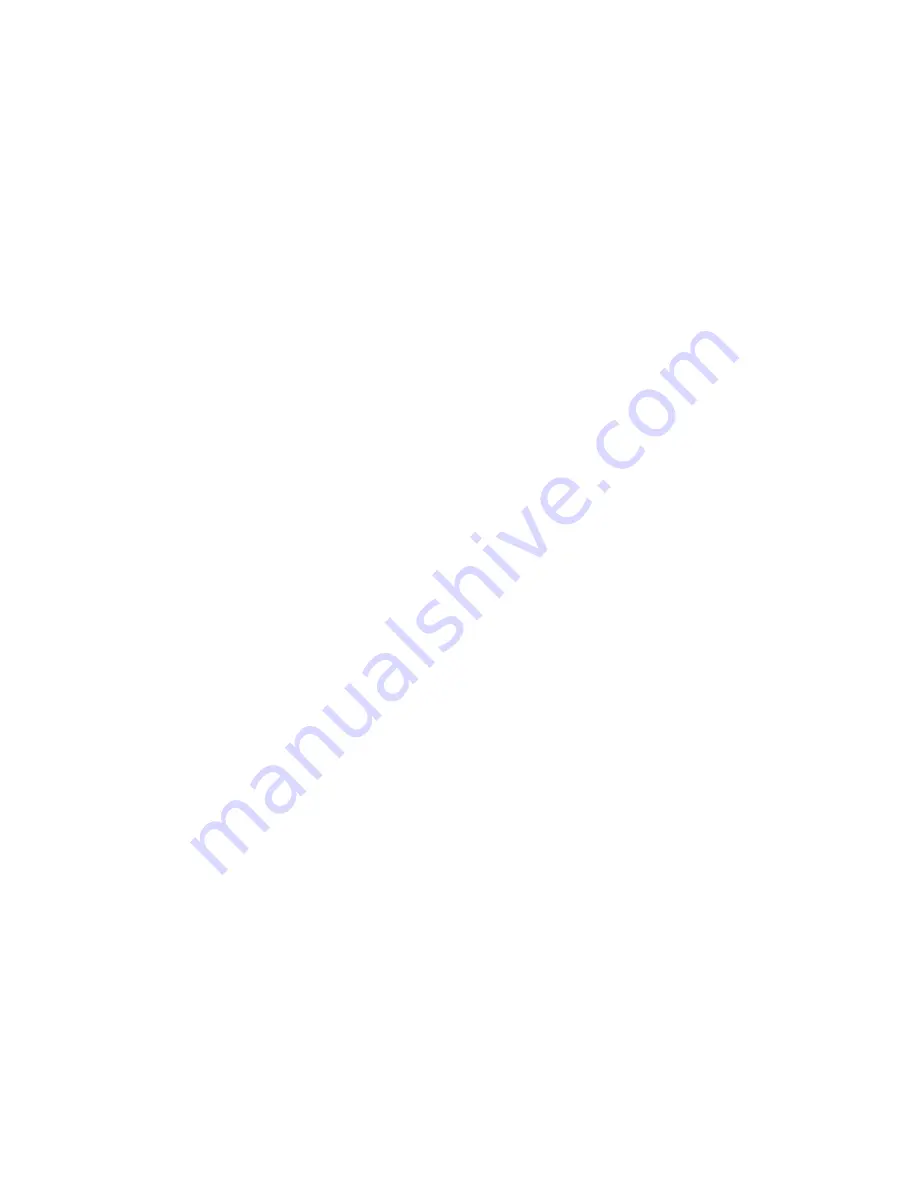
20
Membrane Cleaning
For normal cleaning, the SC
-
3 Acid Cleaning Compound is used first, then the SC
-
2 Alkaline
Cleaning Compound. If known bio
-
fouling is present (rotten egg smell) the SC
-
2 may be used
first. Using hot water if possible, up to 120° (45C) is recommended as it greatly enhances the
ability of the cleaners to do their jobs.
If the history of the system is unknown or it has been left
“
unpickled
”
for an extended length of
time and biological growth is present, it is recommended that the system is cleaned with SC
-
2,
using an alternate source of unchlorinated fresh water before the system is run under pres-
sure. A simple test can be performed to see if biological growth has occurred. Before running
the system, remove the prefilters and examine their condition. If the housings are full of smelly
discolored water, the system was not properly stored. Install clean prefilters if they were bad.
Next check the membrane. Attach the brine service hose and lead it to a bucket. Open the
pressure relief valve one turn, and run the system for 30 seconds. Examine the brine water: if
it
’
s discolored and smells bad, perform an SC
-
2 cleaning with an alternate source of unchlorin-
ated water before running the system pressurized. If the brine is fairly clean, the system can be
purged, run normally, and checked for performance. Clean the membranes only if performance
is reduced.
Heating the water is preferable. One way to do this is to find a camp stove and use a large
stainless steel pot to heat the solution in. The cleaning solution throughout the system will heat
as it circulates in and out of the pot. An alternative is to heat the one or two gallons of initial
water to 120° on the main stove before mixing in the cleaner and circulating it into the system.
Periodically stop and reheat the solution.
Perform the cleaning procedures and then test on a normal feed water supply.
The membranes need to be cleaned only when feed pressure begins to rise due to fouling or
the product quality degrades. The leading cause of fouling is from biological growth that occurs
when the system is left unused without flushing or pickling. Fouling from mineral scaling can
happen during operation under certain source water conditions, and from rust. Monitor the
product salinity and feed pressure for higher than normal readings for the existing conditions.
Other conditions can cause high pressure such as cold feed water or clogged filters
.
Low product flow is usually due to low voltage, a damaged well pump or Clark Pump problems.
Look for all other causes before cleaning the membrane as excessive cleaning shortens mem-
brane life.
There are two types of cleaners: acid and alkaline. The acid cleaner (SC
-
3) will remove mineral
scaling. The alkaline cleaner (SC
-
2) is used to remove biological by
-
products, oil, and dirt parti-
cles that get past the pre
-
filter. If membrane performance is reduced and they have not been
“
pickled
”
recently, cleaning with both chemicals is recommended. The acid cleaner should be
used first followed by the alkaline cleaner. If the membrane fails to respond to both cleanings,
this is an indication of another problem with the system, or that it is time to replace the mem-
brane. Contact Spectra Watermakers before removing a membrane.
Aquifer Membranes maintenance and Cleaning
Содержание AQUIFER 360 EXPEDITION
Страница 2: ...2...
Страница 27: ...27 Wiring Diagram...
Страница 28: ...28 John Guest Super Speedfit Fittings...
Страница 35: ...35 Clark Pump Center Block...
Страница 36: ...36 PL MTS 3 8X1 2S HP CYL SST HP CYL CCA SO HPP ECCB HP CYL EC HP CYL R HP CYL PT Clark Pump Cylinder Assembly...