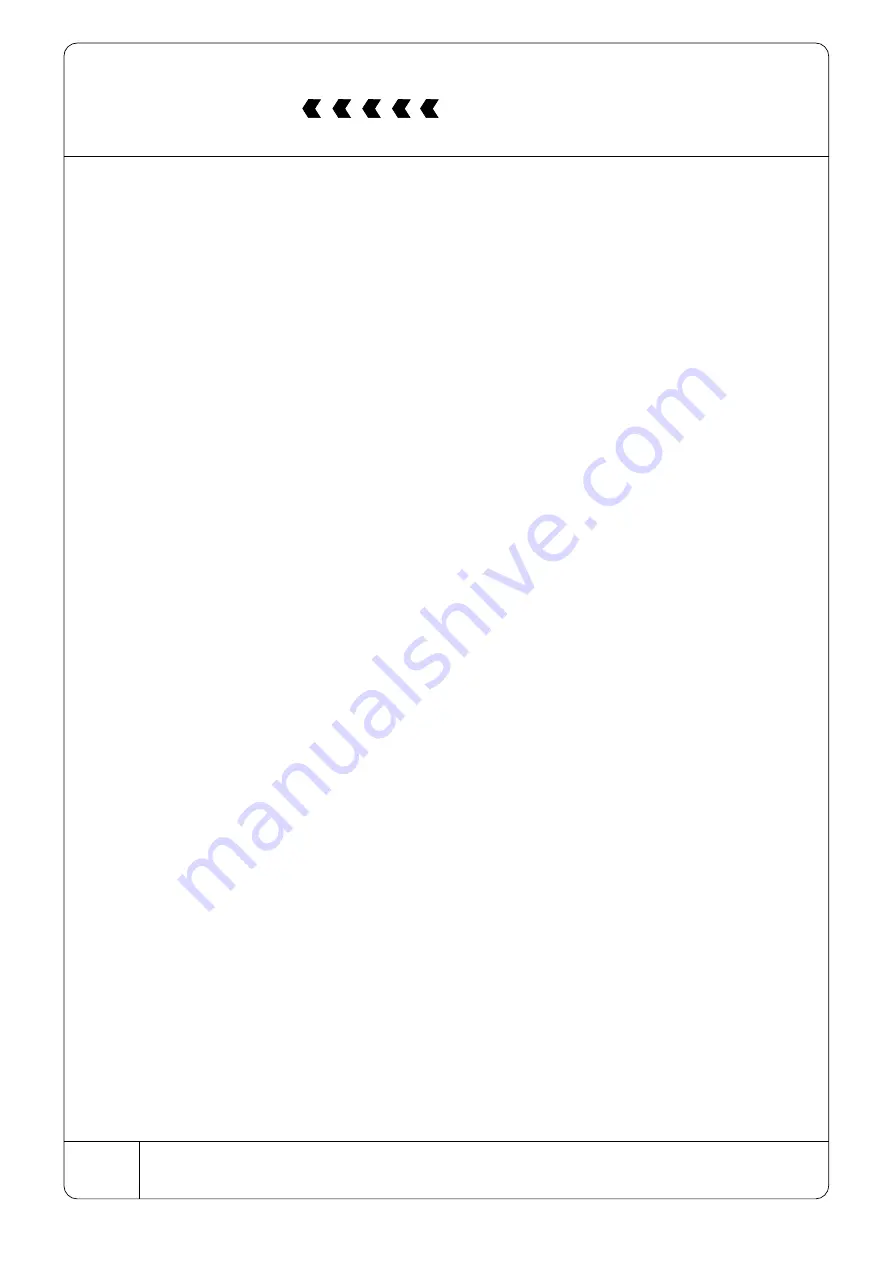
14
Q2000HD, Q2500HD & Q2800HD Flail mower
Spearhead
Servicing and maintenance
Flail Rotor (daily)
n
Grease all bearings daily.
n
Check there is no wrapping of string, plastic, grass or other debris on rotor shaft and rear
roller bearing.
n
Check the condition of flails and ensure all retaining bolts are tight. When flails are replaced
care must be taken to maintain balance of rotor shaft. Do not change to a different type.
n
Flail retaining bolt and nut torque setting is 160Ib.ft. - 200 Nm.
n
Never operate with any flails missing. This will cause severe vibration and lead to rapid
bearing wear and quickly cause the hood to crack.
n
Blunt flails leave an untidy finish and absorb excessive power, when re-sharpening always
wear protective clothing and goggles.
n
When flails are showing severe wear, damage or cracking, they must be replaced
immediately. Never attempt to weld the flails as this will make them very brittle and is extremely
dangerous. Do not take risks with the cutting flails, if in doubt replace.
n
When replacing flails always replace bolts, nuts and bushes for new.
n
Regularly check all rotor bearing bolts are tight.
n
It is imperative the grubscrews are checked on the taper locks (once bedded in, loctite glue
may prove useful).