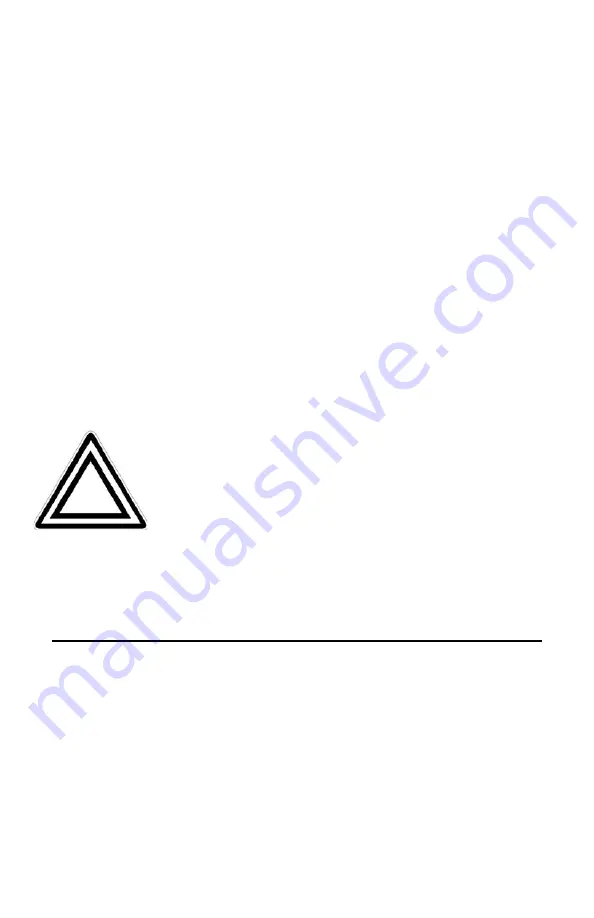
4-1
1.
Switch the ON/OFF Switch (located on the rear panel) to OFF.
2.
Connect the ground clamp cable to positive output terminal, and the TIG
torch cable to the negative output terminal.
3.
Using a secured Argon cylinder, slowly crack open then close the cylinder
valve while standing off to the side of the valve. This will remove any debris
that may be around the valve & regulator seat area.
4.
Install the regulator and tighten with a wrench.
5.
Connect the gas hose to the outlet of the Argon regulator, and tighten with a
wrench.
6.
Be sure the gas valve on the torch is closed, and slowly open the Argon
Cylinder Valve to the fully open position.
7.
Connect the ground clamp to your work piece.
8.
Plug the power cable into the appropriate outlet, and turn the switch to the
“ON” position. The power L.E.D. light should illuminate.
9.
Set the “Process Selection Switch” to LIFT TIG
10.
Set the weld current control knob to the desired amperage.
11.
The tungsten must be ground to a blunt point in order to achieve optimum
welding results. It is critical to grind the tungsten electrode in the direction
the grinding wheel is turning.
12.
Install the tungsten with approximately 1/8” to ¼” sticking out from the gas
cup, ensuring you have correct sized collet.
13.
Tighten the back cap.
14.
You are now ready to begin TIG Welding
OPEN THE GAS VALVE ON TIG TORCH HANDLE, AND
ADJUST THE PRESSURE OF REGULATOR TO 15-25
CUBIC FEET PER HOUR. THIS GAS FLOW SHOULD BE
SUFFICIENT FOR MOST TIG WELDING APPLICATIONS.
Touch the tungsten to the work piece. This closes the welding circuit, and the arc
starts by slowly LIFTING the torch off the base metal. Keep a consistent arc
length of about 1/8-1/4”.
If necessary re-adjust the amperage setting to an appropriate level.
SECTION 4:
OPERATION
4.1 General Operation
Conventional operating procedures apply when using the Welding Power Source,
i.e. connect work lead directly to work piece and electrode lead is used to hold
the electrode. The welding current range values should be used as a guide only.
Current delivered to the arc is dependent on the welding arc voltage, and as
welding arc voltage varies between different classes of electrode, welding current
at any one setting would vary according to the type of electrode in use. The
operator should use the welding current range values as a guide then fine tune
Содержание ARC-100S
Страница 48: ...5 3 5 3 System Schematic ...
Страница 49: ...5 4 5 4 Parts List ...
Страница 53: ...5 3A 5 3 Esquema del sistema ...
Страница 54: ...5 4A 5 4 Lista de piezas ...
Страница 56: ......