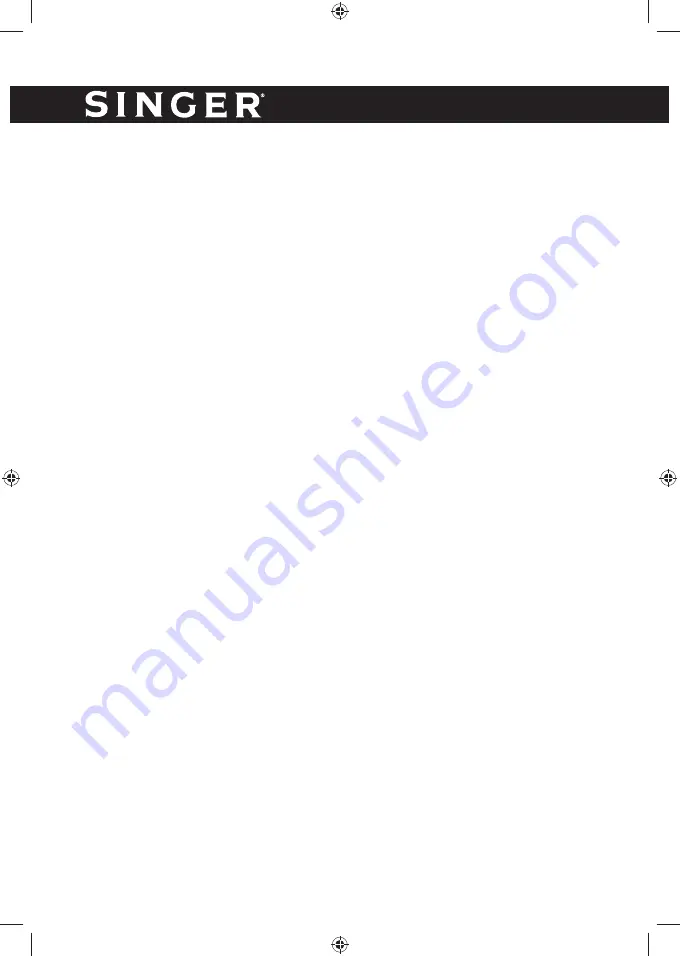
28
ENGLISH
19. Recycling
When removing refrigerant from a system, either for servicing or decommis-
sioning, it is recommended good practice that all refrigerants are removed
safely.
When transferring refrigerant into cylinders, ensure that only appropriate re-
frigerant recovery cylinders are employed. Ensure that the correct number
of cylinders for holding the total system charge is available. All cylinders to
be used are designated for the recovered refrigerant and labelled for that re-
frigerant (i.e. special cylinders for the recovery of refrigerant). Cylinders shall
be complete with pressure-relief valve and associated shut-off valves in good
working order. Empty recovery cylinders are evacuated and, if possible, cooled
before recovery occurs.
The recovery equipment shall be in good working order with a set of instruc-
tions concerning the equipment that is at hand and shall be suitable for the
recovery of all appropriate refrigerants including, when applicable,
fl
ammable
refrigerants. In addition, a set of calibrated weighing scales shall be available
and in good working order. Hoses shall be complete with leak-free disconnect
couplings and in good condition. Before using the recovery machine, check
that it is in satisfactory working order, has been properly maintained and that
any associated electrical components are sealed to prevent ignition in the
event of a refrigerant release. Consult manufacturer if in doubt.
The recovered refrigerant shall be returned to the refrigerant supplier in the
correct recovery cylinder and the relevant waste transfer note arranged. Do
not mix refrigerants in recovery units and especially not in cylinders.
If compressors or compressor oils are to be removed, ensure that they have
been evacuated to an acceptable level to make certain that
fl
ammable re-
frigerant does not remain within the lubricant. The evacuation process shall
be carried out prior to returning the compressor to the suppliers. Only electric
heating to the compressor body shall be employed to accelerate this process.
When oil is drained from a system, it shall be carried out safely.
Содержание Dry Up SDHM-20L ECO
Страница 1: ...SDHM 20L ECO DRY UP Dehumidifier GB INSTRUCTION MANUAL GR R290...
Страница 2: ...GB ENGLISH 3 GR E 30...
Страница 30: ...30 T R290 R290 ODP GWP R290 R290...
Страница 31: ...31 R290 4 m2...
Страница 32: ...32...
Страница 33: ...33 SINGER...
Страница 34: ...34...
Страница 35: ...35 1 service 2 SINGER SINGER SINGER...
Страница 36: ...36 3 Singer 4 24...
Страница 37: ...37 3 1...
Страница 39: ...39 POWER POWER TIMER POWE R HUMIDITY LOCK 3 SEC MODE 3 SEC TIMER POWE R HUMIDITY LOCK MODE 3 SEC 3 SEC...
Страница 40: ...40 LOCK LOCK 2 LOCK 2 MODE MODE AUTO Auto 50 Humidity 5 High Speed 5 Low Speed 5 HIGH DEHUMIDIFYING MODE...
Страница 41: ...41 LOW DEHUMIDIFYING ECONOMY mode MODE FAN ONLY MODE HUMIDITY INTERNAL DRYING MODE 2 MODE 2 Drying Power...
Страница 43: ...43 LED AUTO Auto Humidity AUTO...
Страница 44: ...44 1 2 Power 3 4 Auto 50 5 Mode 6 Humidity 7 Timer 8 Mode Drying 9 Lock LED...
Страница 45: ...45 5 3 15...
Страница 46: ...46 12 mm 2...
Страница 47: ...47 1 2 3 4 Drying 40 C 3 1 3...
Страница 48: ...48 2 C 2 C 30...
Страница 49: ...49 drying 30 R290 0 236ohm 0 236 ohm...
Страница 50: ...50 100m3 h...
Страница 51: ...51 1 2 3 4...
Страница 52: ...52 5 6 7 8...
Страница 53: ...53 9...
Страница 54: ...54 10 11...
Страница 55: ...55 12 13 14 25 OFN...
Страница 56: ...56 15 16...
Страница 57: ...57 17 H...
Страница 58: ...58 80 18 19...
Страница 59: ...59...
Страница 60: ...60 SSM EMC Directive 2014 30 EU LVC Low Voltage Directive 2014 35 EU ROHS Directive 2011 65 EU...
Страница 61: ...61 NOTES...
Страница 62: ...62 NOTES...
Страница 63: ...63 NOTES...