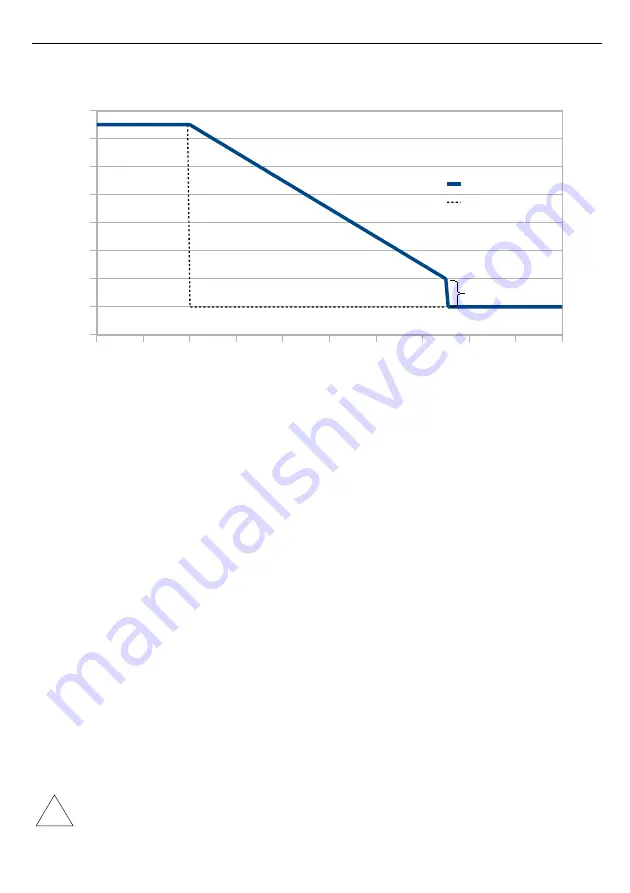
User manual - CONTROLLER PUR-94
Figure 6.8. Comparison of the PID-C controller’s response to a change in the setpoint using
and without the use of fuzzy logic
The inertial block
This is used to smooth the progress of the derivative block response, in other words to
eliminate overly dynamic changes in the output signal’s value caused by the presence of
measurement process noise. The use of the inertial block lengthens response time, but
provides protection against over-regulation that could lead to failures in the controlled system.
Dead zone
The insertion of this parameter provides the possibility of "anesthetising" the control
system to small deviations in the measured value from the setpoint. The
dEAd
parameter
specifies the minimum deviations to which the controller should react. The use of the dead
zone is justified in systems for which oscillation around the setpoint is a natural behaviour.
Auto-tuning
If the user does not know the dynamic parameters of the controlled system, and is unable
to select the suitable controller coefficients or simply doesn’t have the time or patience, the
controller auto-tuning system included in the device can be used instead.
Thanks to auto-tuning, the controlled system is identified and controller settings are
selected using the
Ziegler-Nichols
method, which involves measuring the set oscillation
parameters of the system. The auto-tuning process is divided into three phases, during which
no device settings can be changed, and after their completion the device automatically
switches to operation in the
Pid
mode. The duration of the auto-tuning process depends on the
properties of the controlled system.
During auto-tuning, the user is warned against regulating the actual technological
processes, because auto-tuning may damage the products manufactured in the
process.
25
0
20
40
60
80
100
120
140
160
180
200
0
20
40
60
80
100
120
140
160
PID-C controll loop
FuZL on
FuZL off
time
se
tp
oi
nt
Histeresis
!