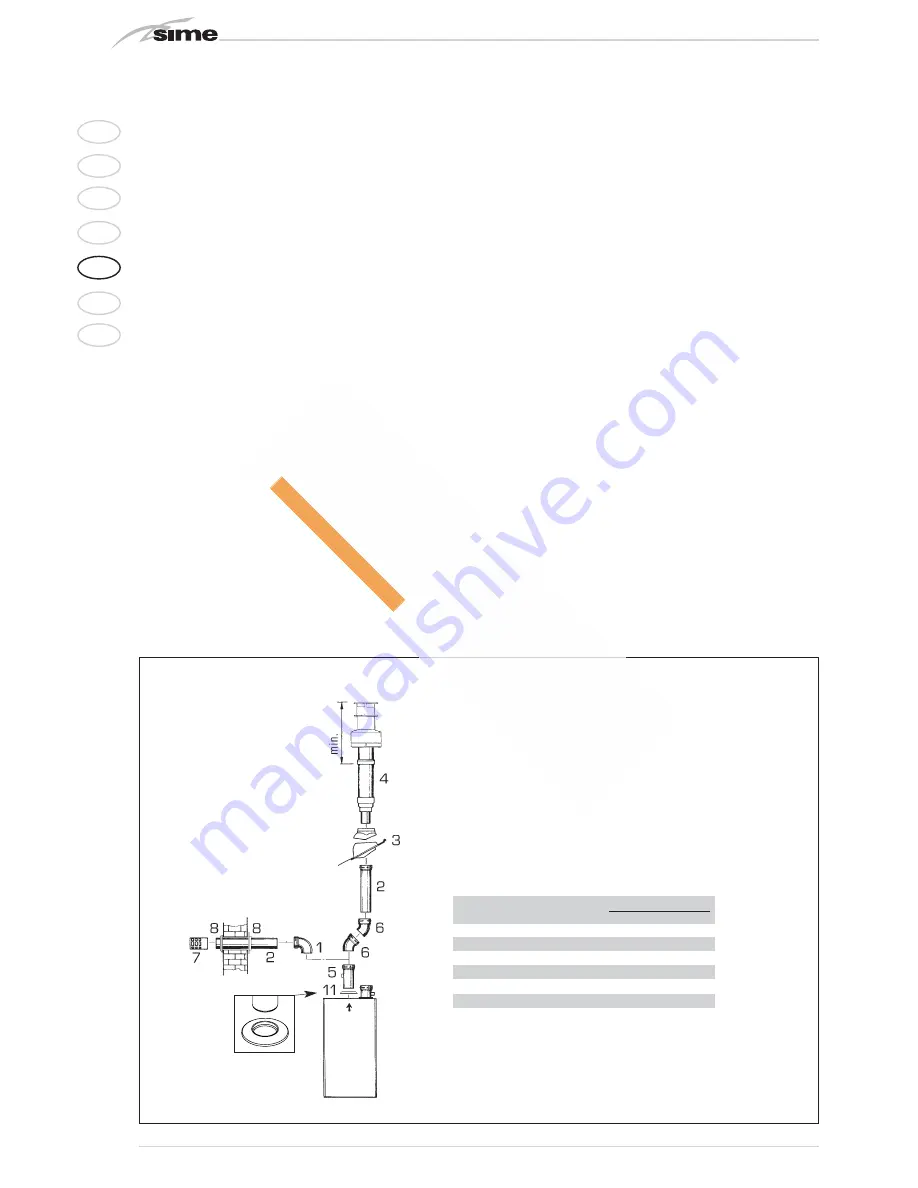
120
IT
ES
FR
BE
GB
RUS
RO
2.3
CONNECTING UP
SYSTEM
To protect the heat system from being
damaged by corrosion, incrustation or
deposits, after installation it is extremely
important to clean the system using suita-
ble products such as, for example, Sentinel
X300 or X400.
Complete instructions are provided with
the products but, for further information,
y o u m a y d i r e c t l y c o n t a c t S E N T I N E L
PERFORMANCE SOLUTIONS LTD.
For long-term protection agains corrosion
and deposits, the use of inhibitors such as
Sentinel X100 is recommended after clea-
ning the system.
It is important to check the concentration
of the inhibitor after each system modifica-
tion and during maintenance following the
manufacturer’s instructions (specific tests
are available at your dealer).
The safety valve drain must be connected
to a collection funnel to collect any dischar-
ge during interventions.
WARNING: Failur e t o clean the heat
system or add an adequate inhibitor inva-
lidates the device’s warranty.
Gas connections must be made in accor-
dance with current standards and regula-
tions. When dimensioning gas pipes from
the meter to the module, both capacity
volume (consumption) in m
3
/h and gas
density must be taken into account.
The sections of the piping making up the
system must be such as to guarantee a
supply of gas sufficient to cover the maxi-
mum demand, limiting pressure loss
between the gas meter and any apparatus
being used to not greater than:
– 1.0 mbar for family II gases (natural gas);
– 2.0 mbar for family III gases (butane or
propane).
A sticker inside the module includes identifi-
cation and gas type data specific to the
module.
2.3.1
Condensation drain
installation.
A siphoned drain must be connected to the
civil drain by a pipe with minimum 5 mm
per meter gradient for condensation collec-
tion.
Only normal plastic civil drain pipes are
suitable to convey condensation to the
building's sewer drain.
2.3.2
Gas pipe filter
The gas valve is fitted with a standard filter.
This filter is not capable of filtering all impuri-
ties and to prevent poor gas valve operation
or failure of any gas valve safety feature, it is
advisable to fit a suitable filter on the gas
supply pipe.
2.5
FILLING THE SYSTEM
Cold system filling pressure must be 1 bar.
The system must be filled slowly so that air
bubbles are released through the specific
escapes.
2.6
EXHAUST
The boiler is supplied with a 80mm gasket,
which must be fitted over the exhaust ter-
minal prior to the flue being installed. (11
fig. 4-4/a-4/b).
2.6.1
Type B
(fig. 4)
If the inlet is not connected, the boiler
should be regarded a Class B device. When
installing the boiler in locations where it
needs to be protected from water, replace
the intake terminal inserted in the flange
with terminal code 8089510. For informa-
tion on how to configure the boiler in this
mode see figure 4.
The maximum overall length of ø 80
exhaust flues is determined by the load
losses of the single accessories installed
and should not exceed 16 mmH
2
O (“60
BFR”) and 28 mmH
2
O (“100 BFR”).
2.6.2
Type C
(figg. 4/a-4/b)
The boiler becomes a Class C device when
the intake terminal is removed from the
flange and the intake is connected to sepa-
rate exhaust ducts (fig. 4) or with coaxial
exhaust (fig. 4/b).
ø 80 ACCESSORY LOAD LOSS TABLE
WARNING: Before installing accessories, lubricate
the internal part of gaskets with silicon-based pro-
ducts. Avoid using oils and greases.
KEY
1
90° MF polypr. curve (6 pcs.) code 8077450
2 a Polypr. extension L.1000 (6 pcs.) code 8077351
2 b Polypr. extension L. 500 (6 pcs.) code. 8077350
3
Hinged tile code 8091300
4
Roof Terminal kit L 1285 code 8091205
5
Polypropylene extension L. 250 with test outlet code 6296513
6
45° MF polypr. curve (6 pcs.) code. 8077451
7
Exhaust terminal code 8089501
8
Internal-external ring nut kit code 8091500
11
Rubber gasket ø 80 (supplied as standard)
Load loss (mm H
2
O)
“60 BFR”
“100 BFR”
90° MF polypropylene curve
1,30
3,00
45° MF polypropylene curve
0,70
2,00
Polypr. extension L. 1000
0,60
1,20
Polypr. extension L. 500
0,30
0,60
Roof exit terminal L. 1381
1,20
4,30
Exhaust terminal
1,30
3,60
Polypropylene extension L. 250
0,15
0,30
Type B
Fig. 4
600