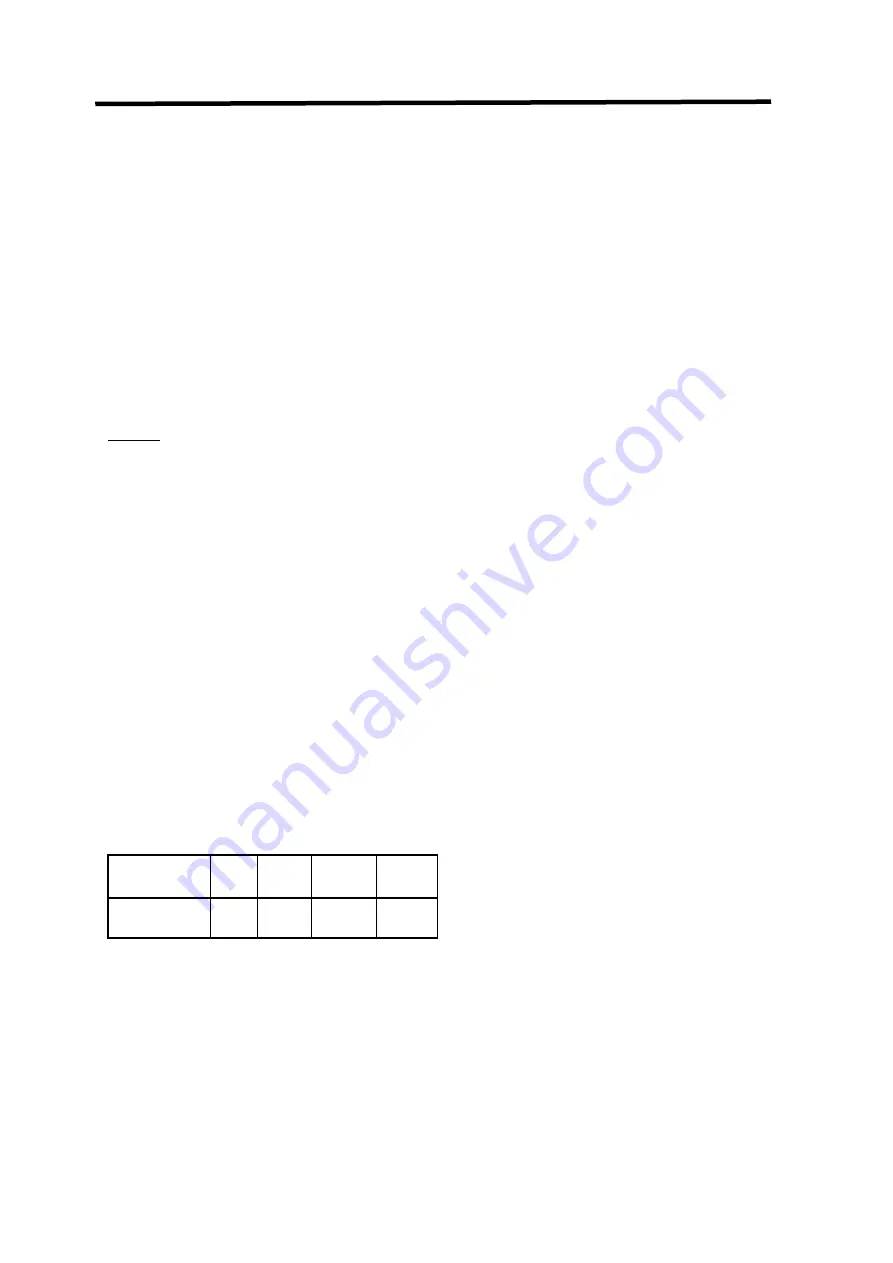
18
Lubrication and Maintenance
Tank, Pump and Spray Lines
At the end of each day run clean water through
the pump, spray lines and nozzles to purge them
of chemicals. Rinse out the tank to remove any
powdered material.
In the case of frost or freezing conditions run the
pump dry to prevent water freezing in it or the
spray lines and damaging components.
Never leave chemicals in the tank that may settle
to the bottom, harden and break into lumps as this
may block the suction filter.
Dispose of unused chemical, chemical mix, rinse
water and chemical containers as recommended
by the chemical manufacturer or the relevant
government authority.
Caution
Do not use a high pressure washer to
clean around fan bearings, pump seals or
electrical valves if fitted.
Tyres
Inspect the tyres regularly and inflate to 250 kpa
(36 psi) if necessary.
Diaphragm Pump
Drain the oil from the pump annually, or at the end
of each spraying season. Refill with SAE 20W-50
multi-grade engine oil.
Remove the pump heads, carefully inspect the
diaphragms and replace if necessary. Also check
the inlet and outlet valves, seats and springs for
wear, damage or chemical corrosion and replace
as necessary.
Check the air pressure in the surge chamber on
the pump. The air pressure behind the surge
chamber’s diaphragm smoothes out the
pulsations in fluid flow and should be set in
accordance with the spraying pressure being
used, as shown in the chart below.
Spraying (Bar)
pressure (psi)
2 - 5
29 - 73
5 - 10
73 - 145
10 - 20
145 - 290
20 - 50
290 - 725
Surge air (Bar)
pressure (psi)
2
29
2 - 5
29 - 73
5
– 7
73 - 102
7
102
Adjust the pressure at the valve fitting on the
chamber using a compressed air hose fitted with
a tyre valve connection and a reliable pressure
gauge.
Refer to the pump instruction manual for further
details on the above maintenance operations.
Wheel Hubs
Remove the wheel hubs annually and check that
the bearings and seals are in good condition.
Repack the bearings with multi-purpose grease
as required.
Adjust the wheel bearings by tightening the axle
nut, then backing it off by approximately 1/6 turn
before installing the cotter pin. Check that the
hubs are free to rotate without any end play.
Annual Inspection (or 350 hours)
At the end of each season or every 350 hours
inspect the sprayer for any signs of damage,
corrosion or leakage.
Replace any parts that are affected by chemical
contamination.
Check that all bolts are securely tightened,
including the tank mounting bolts, axle U-bolts
and wheel nuts. Check that all hose connections
are tight.