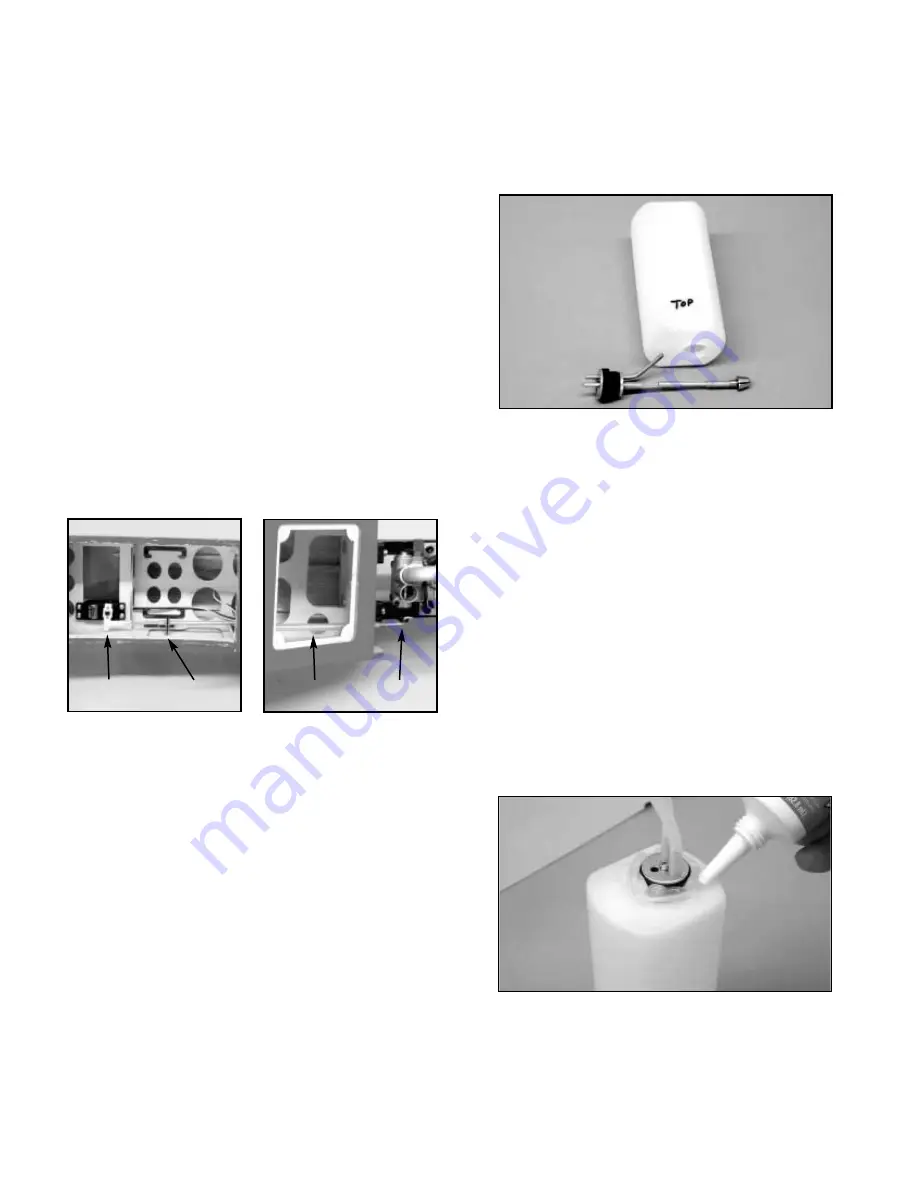
❑
16) Insert the clunk fuel pick-up weight into one end of the
silicone fuel line that was inside of the tank. Lower this assembly
into the tank until the clunk touches the back of the tank and mark
this distance. Measure 1/2" towards the clunk from this mark and
cut the tubing off at that point. Slide this tube onto the pickup tube
on the back of the stopper assembly and inset this assembly into
the tank. The clunk should be about 3/8" from touching the back
of the tank, allowing it to swing free within the tank body.
The vent tube should just touch the top of the tank at an angle.
Adjust as needed before tightening the stopper into place, using
the supplied M3 x 20mm compression bolt.
Tighten this bolt
sufficiently to compress the rubber stopper, creating a good tank
seal. Attach an 8" length of fuel line to each tube at the front of the
tank and use tape to identify each line as the "vent" and "fuel" line.
Pressure test the tank and fuel line, then repair leaks, (if any). The
fuel tank is now ready to install in the fuselage.
❑
17) Working through the wing opening in the bottom of the
fuselage, slide the fuel tank into position while routing the fuel lines
through the firewall. Because of the offset neck, it will only line up
with hole in the firewall one way. When you are satisfied with the
fit, remove the tank and apply a generous bead of clear silicone
RTV around the stopper/neck of the tank, where it will contact the
firewall. Slide the tank and fuel lines back into place, pressing it
firmly to the back of the firewall. The 8mm x 12mm x 100mm balsa
fuel tank retainer is now pressed in place against the back of the
tank. Use a little thin CA glue to glue it in place. To help hold the
tank in place and provide some cushioning from vibration, squeeze
some RTV between the fuel tank and the rear bulkhead and on the
retainer block before installing it behind the tank.
MOUNTING THE COWL:
❑
18) Inspect the inside rear edges of the cowl. If needed, use
sandpaper to smooth the inside rear surface, making it free of any
bumps or ragged edges that may scratch or dent the fuselage
when pressed in place. Also, make sure the six mounting holes
in the sides of the cowl are open and free of any debris. For
8
Adjustable
Arm
Pushrod
Guide
Outer
Tube
Z-bend
the inside of the fuselage, about 2" ahead of the throttle servo,
using epoxy or thick CA. Trim the throttle housing tube so that it
only extends about 1/4" past the guide.
❑
14) With the outer pushrod housing tube in place, the
inner throttle pushrod is now prepared.
Thread the provided
2mm x 36mm Z-bend link into one end of the inner nylon pushrod.
Drill out the hole in the carburetor throttle arm with a #46 drill, to
allow the Z-bend to fit. Insert the Z-bend into the throttle arm, slide
the inner pushrod into the outer housing tube and mount the
engine with 2 bolts to hold it in the proper position. Move the
throttle arm to the closed position and note if this moves the
pushrod in or out of the firewall. Turn on your radio and use the
reversing function to make the throttle servo move in the correct
direction when you pull the throttle down to idle.
Adjust the
throttle trim to its lowest setting, making sure the carburetor is at
its lowest idle/cutoff position. Now trim the inner pushrod to make
the end 1-1/2" short of the servo output arm hole you will be using.
Now thread the 2mm x 22mm stud about 1/2 way into the servo
end of the inner pushrod and then thread a nylon R/C link onto the
stud. Adjust until the servo drives the throttle arm to just touch the
idle stop when the trim is full down on the transmitter. Next move
the throttle stick to full throttle and the trim to full up. Adjust the
endpoint in the transmitter until the throttle is fully open.
It is
important that the servo should not growl or the pushrod flex at
either end of these throws. If you are using a non-computerized
transmitter, an easy way to adjust the throw is to use the adjustable
servo arm that comes with most servos as shown in the photo.
FUEL TANK ASSEMBLY:
❑
15) Locate the parts bag containing the fuel tank assembly. We
use a simple two-line fuel delivery system for this airplane. Note
that the rubber fuel stopper has two holes all the way through it.
Use these two holes for the two aluminum fuel lines.
Two pieces 1/8" aluminum tubing have been provided for venting
the fuel tank. The first piece is 2-3/8" in length and the second
is 2". Holding the front and rear metal compression disks in place
to the front and back side of the rubber stopper, insert the 2" piece
of aluminum tubing into the rubber stopper for the fuel pick up tube,
leaving 1/2" of the tube protruding out the front of the stopper.
Next, make a gentle 60
O
bend in the middle of the 2-3/8" aluminum
tubing, (making two equal sides), to make the overflow vent tube.
Insert this piece completely through the stopper assembly in the
same orientation as shown in the photo, again leaving a 1/2" of the
tubing protruding from the front face of the stopper.
Note: The neck of the fuel tank is NOT located in the center of the
tank body and is offset to one side. When looking at the front of
the tank, the neck should be offset to the right. The side of the tank
that is up will be top of the tank when mounted in the airplane and
should be marked for reference.