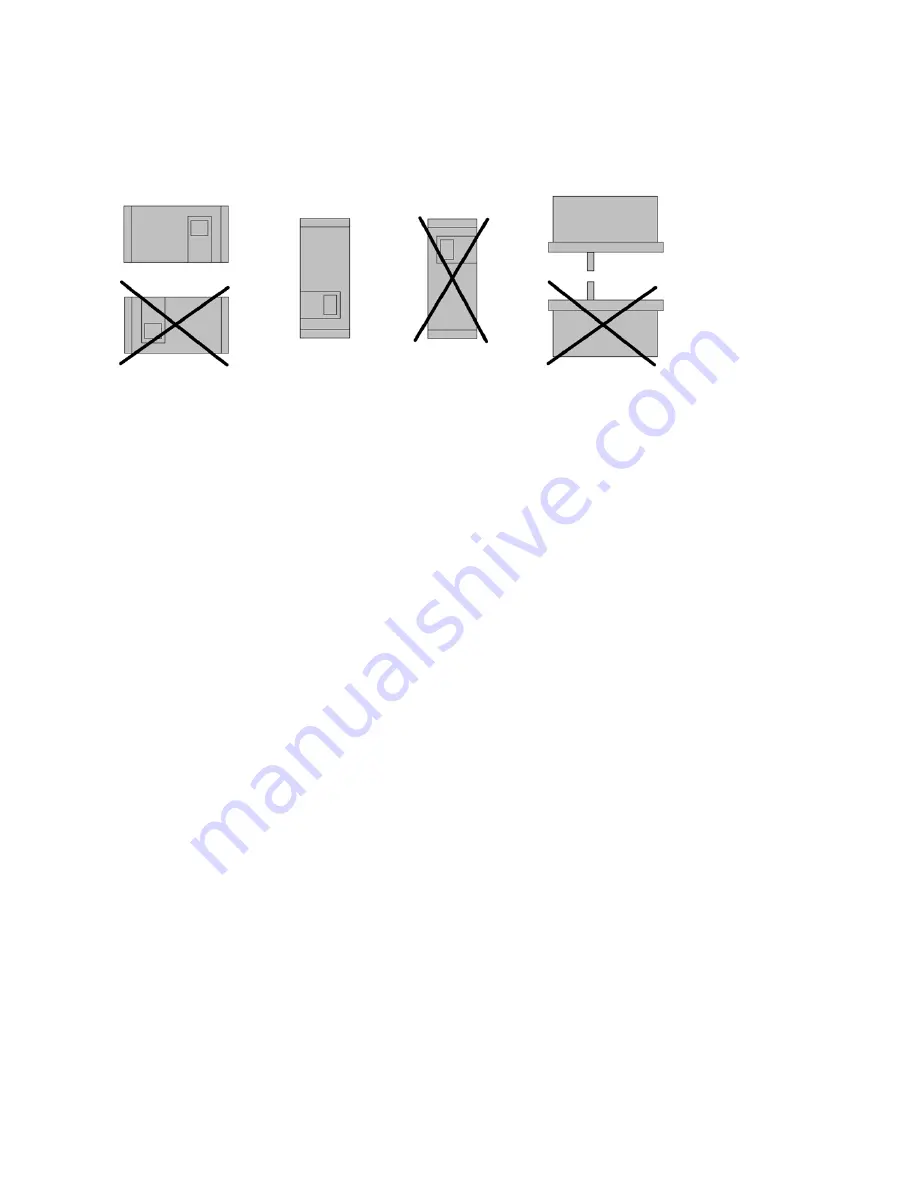
SIPART PS2 (6DR5...)
A5E03436620-AB, 01/2017
11
Favorable and unfavorable mounting positions
Avoid the unfavorable mounting positions:
●
To prevent fluids seeping through during normal operation of the device, e.g. through exhaust air openings.
●
Otherwise the display becomes poorly legible.
Figure 3-1
Favorable and unfavorable mounting positions
Additional measures to prevent liquids from seeping through
Take additional measures to prevent liquids from seeping through if the conditions force you to operate the positioner in an
unfavorable mounting position.
Additional measures required to prevent liquids from seeping through depend on the selected mounting position. You may
also require:
●
Gland with sealing ring, e.g. FESTO: CK - 1 / 4-PK-6
●
Approximately 20 to 30 cm plastic hose, e.g. FESTO: PUN - 8 x 1.25 SW
●
Cable tie; the number and the length depend on the local conditions.
Procedure
1.
Install the casing such that rain water or condensate running along the pipes can be drained before the terminal strip of
the positioner.
2.
Check the seals of electrical connections for perfect fitting.
3.
Check the seal in the enclosure cover for damage and contaminations. Clean and/or replace if required.
4.
Install the positioner such that the sintered bronze attenuator at the bottom side of the enclosure points downwards in the
vertical mounting position. If this is not possible, replace the attenuator with a suitable gland with a plastic hose.
Procedure for installing the plastic hose on the gland
1.
Unscrew the sintered bronze attenuator from the exhaust air opening at the bottom side of the enclosure.
2.
Screw in the aforementioned gland into the exhaust air opening.
3.
Install the aforementioned plastic hose into the gland and check whether it fits firmly.
4.
Fasten the plastic hose with a cable tie onto the control valve such that the opening points downwards.
5.
Ensure that the plastic hose does not have any kinks and the exhaust air flows out without any hindrance.
3.5
Positioners subjected to fast acceleration or strong vibration
The electropneumatic positioner has an gear latch for the friction clutch and for the transmission ratio selector.
Strong acceleration forces act on control valves that are subjected to heavy mechanical loads, e.g. breakaway valves,
strongly shaking or vibrating valves, as well as in case of "vapor shocks". These forces may be much higher than the
specified data. This may cause the friction clutch to move in extreme cases.
The positioner is equipped with an gear latch for the friction clutch to counter these extreme cases. The setting of the
transmission ratio selector can also be locked.
The locking procedure is illustrated and described below.
Содержание SIPART PS2 6DR5xx0 series
Страница 1: ......