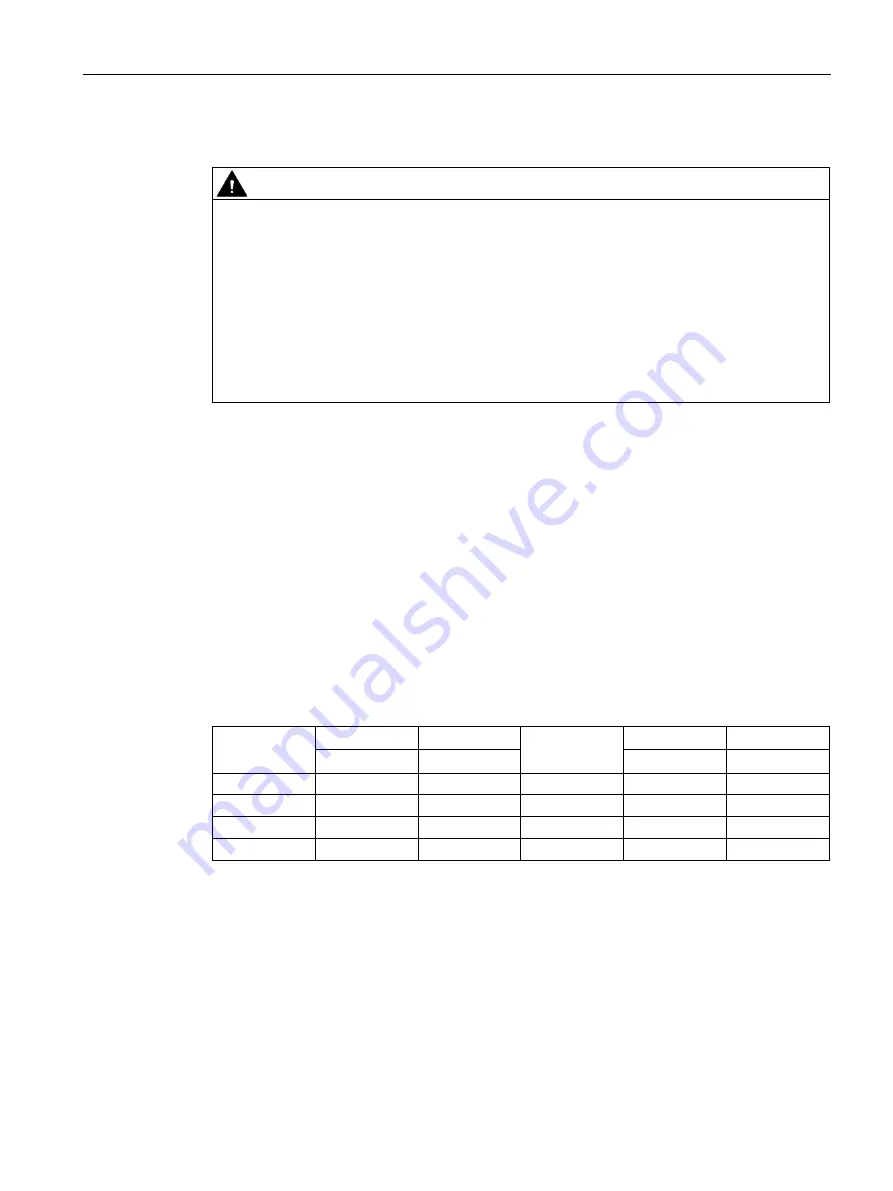
Preparing for use
3.2 Transportation and storage
SIMOTICS S-1FG1 servo geared motor
Operating Instructions, 07/2019, A5E47360747B AA
43
Lifting and transporting the motor using a crossbar
WARNING
Danger to life due to falling servo geared motors
The threads for eyebolts in the motor housing are not designed for carrying the entire servo
geared motor.
If you lift the servo geared motor only by the eyebolts in the motor housing, the eyebolts
can be ripped out of the threads and cause death or serious injury.
•
For transporting, screw the eyebolts into the threads in the gearbox housing depending
on the position.
•
Use the threads for the eyebolts in the motor housing only for position stabilization.
•
Observe the maximum load of the eyebolt in accordance with the table below.
Transport the servo geared motor by the lifting eyes or eyebolts in the gearbox housing.
Because they are designed only for the weight of the geared motor, it is not permissible to
add additional loads to the lifting eyes and eyebolts.
Use a crossbar for lifting and transporting the servo geared motor.
Procedure
1.
Screw the lifting eyes (eyebolts) in at appropriate locations for the orientation of the servo
geared motor during transportation. Use laminated fiber washers.
2.
Hook the beam into the lifting eyes (eyebolts).
You have suspended the servo geared motor for safe transportation.
❒
Table 3- 2
Maximum load of the eyebolt on the gearbox
Thread size
m
d
3
Thread size
m
d
3
kg
mm
kg
mm
M8
140
36
M20
1 200
72
M10
230
45
M24
1 800
90
M12
340
54
M30
3 200
108
M16
700
63
-
-
-
Setting the servo geared motor down
Procedure
1.
Set the servo geared motor down on a hard, level surface.
2.
Secure the servo geared motor against unintentional movements.
You have set the servo geared motor down in a stable position.
❒
Содержание SIMOTICS S-1FG1
Страница 1: ...SIMOTICS S 1FG1 servo geared motor ...
Страница 2: ......
Страница 8: ...Introduction SIMOTICS S 1FG1 servo geared motor 6 Operating Instructions 07 2019 A5E47360747B AA ...
Страница 12: ...Table of contents SIMOTICS S 1FG1 servo geared motor 10 Operating Instructions 07 2019 A5E47360747B AA ...
Страница 140: ...Faults SIMOTICS S 1FG1 servo geared motor 138 Operating Instructions 07 2019 A5E47360747B AA ...
Страница 168: ......
Страница 170: ......