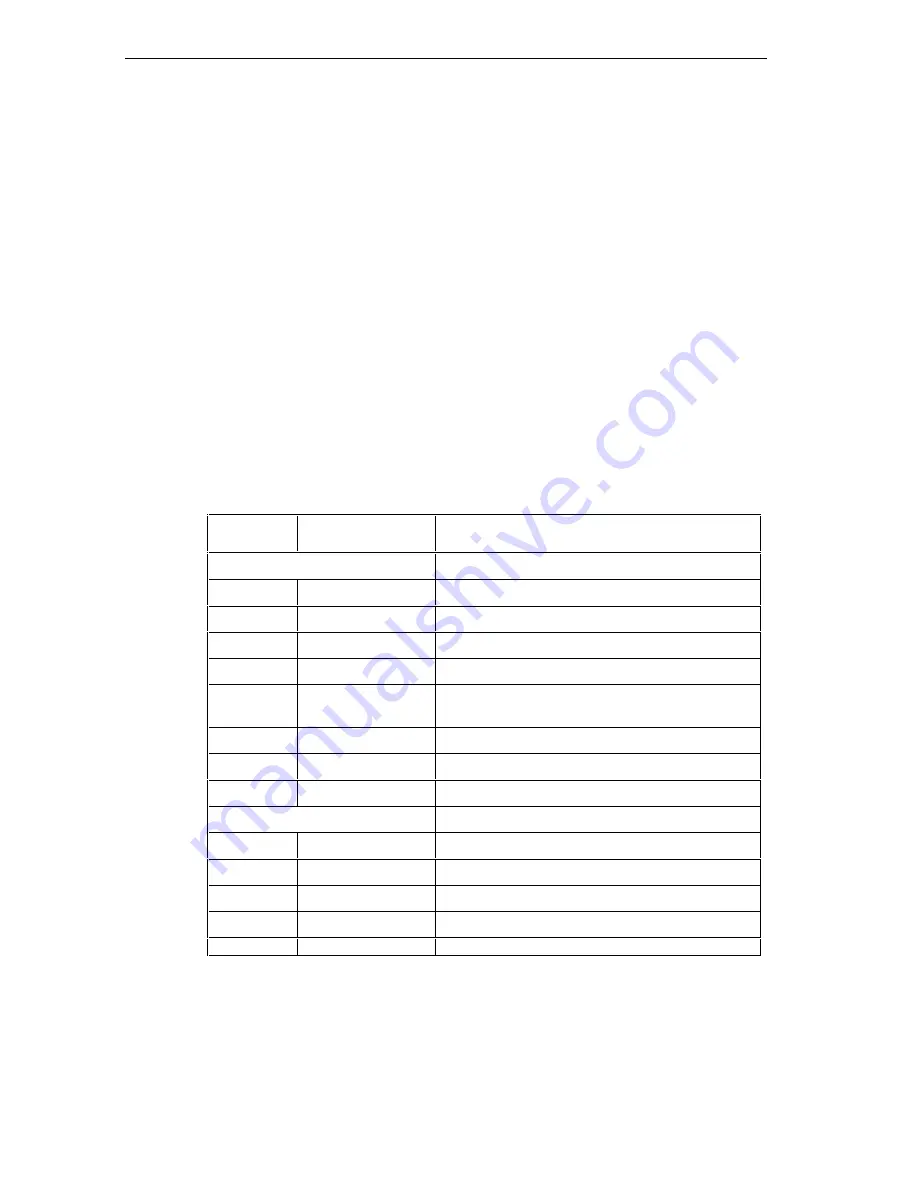
Designing a Sequential Control System based on the Example of a Drill
S7-GRAPH for S7 300/400 Programming Sequential Control Systems
3-6
C79000-G7076-C526-01
3.3
Defining the System Signals
Once you have broken down the drilling operation into individual steps, you should
then define the input and output parameters for each step. The basis of the
concept design is the technological drawing and the flowchart.
Defining Inputs and Outputs
List the inputs and outputs for the drill in the form of a table.
If you want to program symbolically, enter the required symbolic names (for
example input I 0.4 "Cl_press_ok") for the absolute inputs and outputs and any
comments that will make the program easier to understand (for example
"Workpiece clamping pressure reached").
In the drill example, it is assumed that the switches and contactors of the drill are
controlled via the inputs and outputs of the digital input/output module of the
S7-300 programmable controller. The input/output module has 8 inputs and 8
outputs. The default values of the input and output addresses of the module
inserted in slot 4 are as follows: I 0 to I 0.7 and Q =0.0 to Q 0.7.
Absolute
Addresses
Symbolic
addresses
Explanation
Inputs
in the program (I)
I 0.0
Dr_mot_running
Feedback signal for drill running at selected speed
I 0.1
Dr_mot_stopped
Feedback signal for drill stopped
I 0.2
Drill_down
Limit switch for drill in lower position
I 0.3
Drill_up
Limit switch for drill in upper position
I 0.4
Cl_press_ok
Feedback signal for work piece clamping pressure
reached
I 0.5
Coolant_sel
Selector for coolant (dependent on work piece)
I 0.6
Cool_press_ok
Feedback signal for coolant pressure reached
I 0.7
Start_button
Start button of the drill
Outputs
in the program (Q)
Q 0.0
Dr_mot_on
Turn on drill motor
Q 0.1
Cool_pump_on
Turn on cooling pump (dependent on work piece)
Q 0.2
Lower_drill
Lower drill and carriage to bottom limit position
Q 0.3
Raise_drill
Raise drill and carriage to the upper limit position
Q 0.4
Clamp_workp
Clamp work piece at required pressure