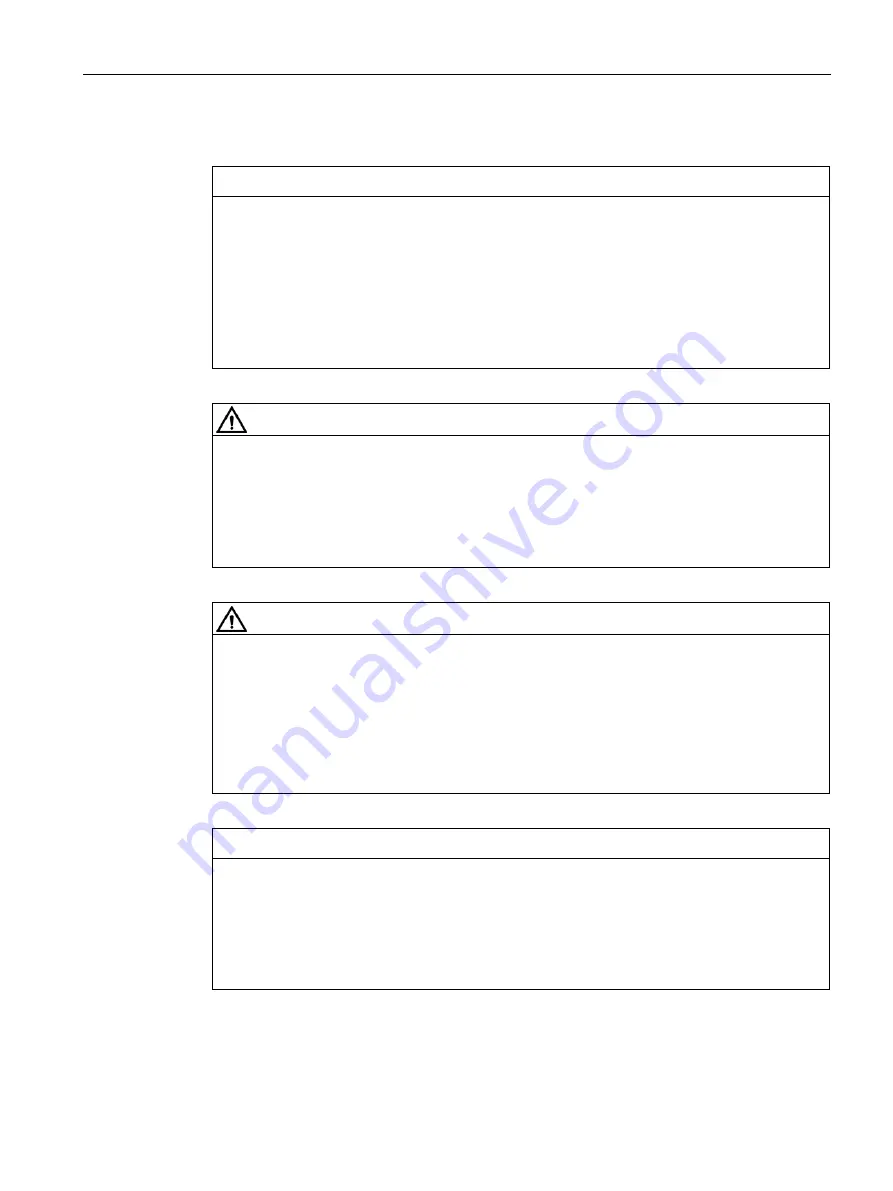
Fundamental safety instructions
1.1 General safety instructions
SIMATIC ET 200pro FC-2 converter
Operating Instructions, 04/2018, FW V4.7 SP10, A5E34257324B AF
13
NOTICE
Damage to motor insulation due to excessive voltages
When operated on systems with grounded line conductor or in the event of a ground fault in
the IT system, the motor insulation can be damaged by the higher voltage to ground. If you
use motors that have insulation that is not designed for operation with grounded line
conductors, you must perform the following measures:
•
IT system: Use a ground fault monitor and eliminate the fault as quickly as possible.
•
TN or TT systems with grounded line conductor: Use an isolating transformer on the line
side.
WARNING
Fire due to inadequate ventilation clearances
Inadequate ventilation clearances can cause overheating of components with subsequent
fire and smoke. This can cause severe injury or even death. This can also result in
increased downtime and reduced service lives for devices/systems.
•
Ensure compliance with the specified minimum clearance as ventilation clearance for
the respective component.
WARNING
Unrecognized dangers due to missing or illegible warning labels
Dangers might not be recognized if warning labels are missing or illegible. Unrecognized
dangers may cause accidents resulting in serious injury or death.
•
Check that the warning labels are complete based on the documentation.
•
Attach any missing warning labels to the components, where necessary in the national
language.
•
Replace illegible warning labels.
NOTICE
Device damage caused by incorrect voltage/insulation tests
Incorrect voltage/insulation tests can damage the device.
•
Before carrying out a voltage/insulation check of the system/machine, disconnect the
devices as all converters and motors have been subject to a high voltage test by the
manufacturer, and therefore it is not necessary to perform an additional test within the
system/machine.