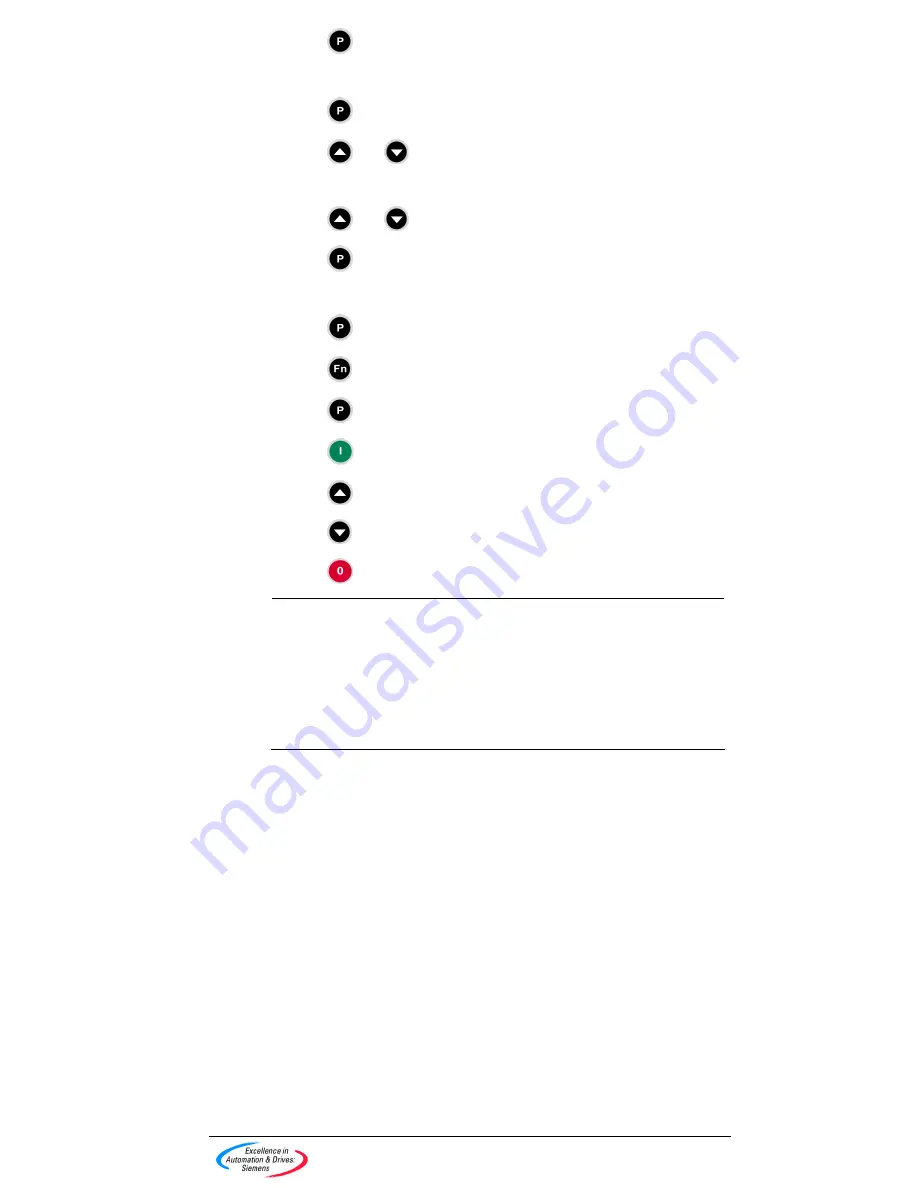
5
AOP Operating Instructions – Issue 07/05
6SE6400-5AP00-0BB0
14. Press to edit the parameter value.
15. Set P0700 = 4 (AOP).
16. Press to confirm selection.
17. Using and
select P1000.
18. Set P1000 = 1 (MOP Setpoint).
19. Using and
select P0010
20. Press to edit the parameter value.
21. Set P0010 access level to 0
22. Press to confirm selection.
23. Press to return to r0000.
24. Press to display the standard screen.
25. Press to start the inverter/motor.
26. Using the output will increase
27. Using the output will decrease
28. Press to stop the inverter/motor.
Note
¾
If the AOP is to be used as the normal control means for the
inverter it is recommended that the user Set P2014.1 = 5000. To
do this first set P0003 = 3. This setting will cause the drive to trip if
communication with the control source, the AOP, is lost.
¾
If you have problems connecting to the inverters – set the Auto
Baud to OFF and the default baud rate to the same as the
inverter. See Section 2.5 on page 10.
2.2
Network Setup (RS 485 With Panel Mounting Kit)
There are two main modes of operation for the AOP when connected to a
network of Micromaster 4
th
generation drive. These modes are both under the
Master mode of operation on the AOP allowing a single drive to be accessed on
the network with full control/parameter access or selecting B or broadcast mode
all drives on the network can be set to start/stop at the same time.
The AOP has the capability to control up to 31 inverters connected as a network.
A unique two-digit number identifies each inverter.
To set-up a network of inverters under the control of an AOP, the following
procedure should be performed: