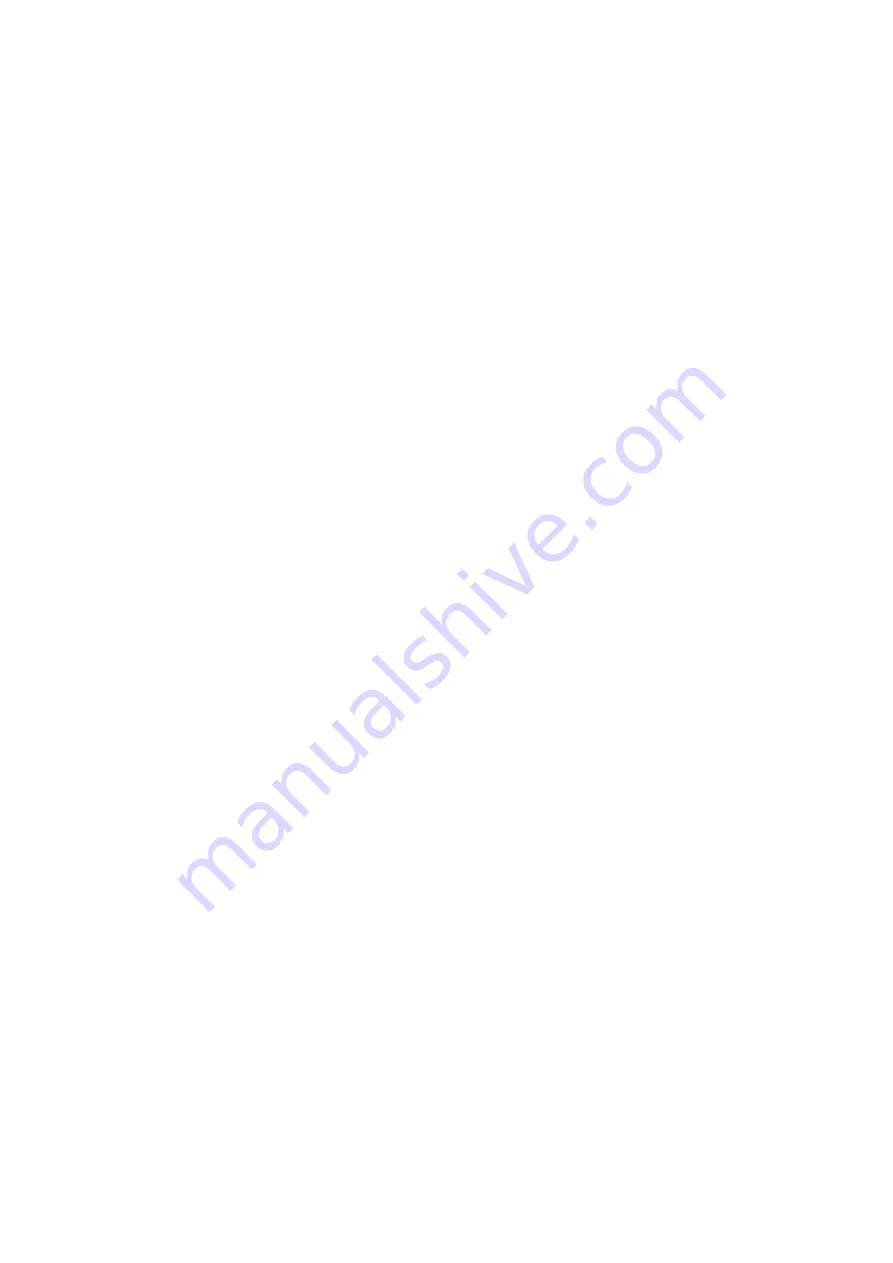
Preparations for use
4
Good planning and preparation of machine applications are essential in terms of keeping
installation simple and avoiding errors, ensuring safe operation, and allowing access to the
machine for servicing and corrective maintenance.
This chapter outlines what you need to consider when configuring your plant in relation to this
machine and the preparations you need to make before the machine is delivered.
4.1
Safety-related aspects to consider when configuring the plant
A number of residual risks are associated with the machine. These are described in the chapter
titled "Safety information" (Page 13) and in related sections.
Take appropriate safety precautions (covers, barriers, markings, etc.) to ensure the machine
is operated safely within your plant.
4.2
Observing the operating mode
Observe the machine's operating mode. Use a suitable control system to prevent overspeeds,
thus protecting the machine from damage.
4.3
Ensuring cooling
Ensure that the machine is sufficiently cooled by the cooling air flow at the installation site:
● Ensure that the cooling air can flow in and out unobstructed. The full air flow provided by
the fan is only possible if air can freely enter the impeller. In the axial direction, ensure a
clearance of at least 1 x air intake diameter.
● Make sure that the machine does not draw in the hot discharged air again.
● For machines with a vertical type construction with an air intake from above, ensure that
the air inlets are protected against the ingress of foreign bodies and water.
4.4
Cooling water quality
● The cooling water must circulate in a closed cooling circuit.
● Avoid fluctuations in the oxygen content of the cooling water.
SIMOTICS TN Series N-compact 1LH8
Operating Instructions 06/2017
25
Содержание 1PQ8
Страница 2: ...06 06 2017 10 16 V15 00 ...
Страница 80: ...Start up 7 8 De energizing SIMOTICS TN Series N compact 1LH8 80 Operating Instructions 06 2017 ...
Страница 92: ...Operation 8 10 faults SIMOTICS TN Series N compact 1LH8 92 Operating Instructions 06 2017 ...
Страница 112: ...Maintenance 9 2 Corrective Maintenance SIMOTICS TN Series N compact 1LH8 112 Operating Instructions 06 2017 ...
Страница 128: ...Disposal 11 4 Disposal of components SIMOTICS TN Series N compact 1LH8 128 Operating Instructions 06 2017 ...
Страница 130: ...Service and Support SIMOTICS TN Series N compact 1LH8 130 Operating Instructions 06 2017 ...
Страница 134: ...Quality documents SIMOTICS TN Series N compact 1LH8 134 Operating Instructions 06 2017 ...
Страница 139: ......