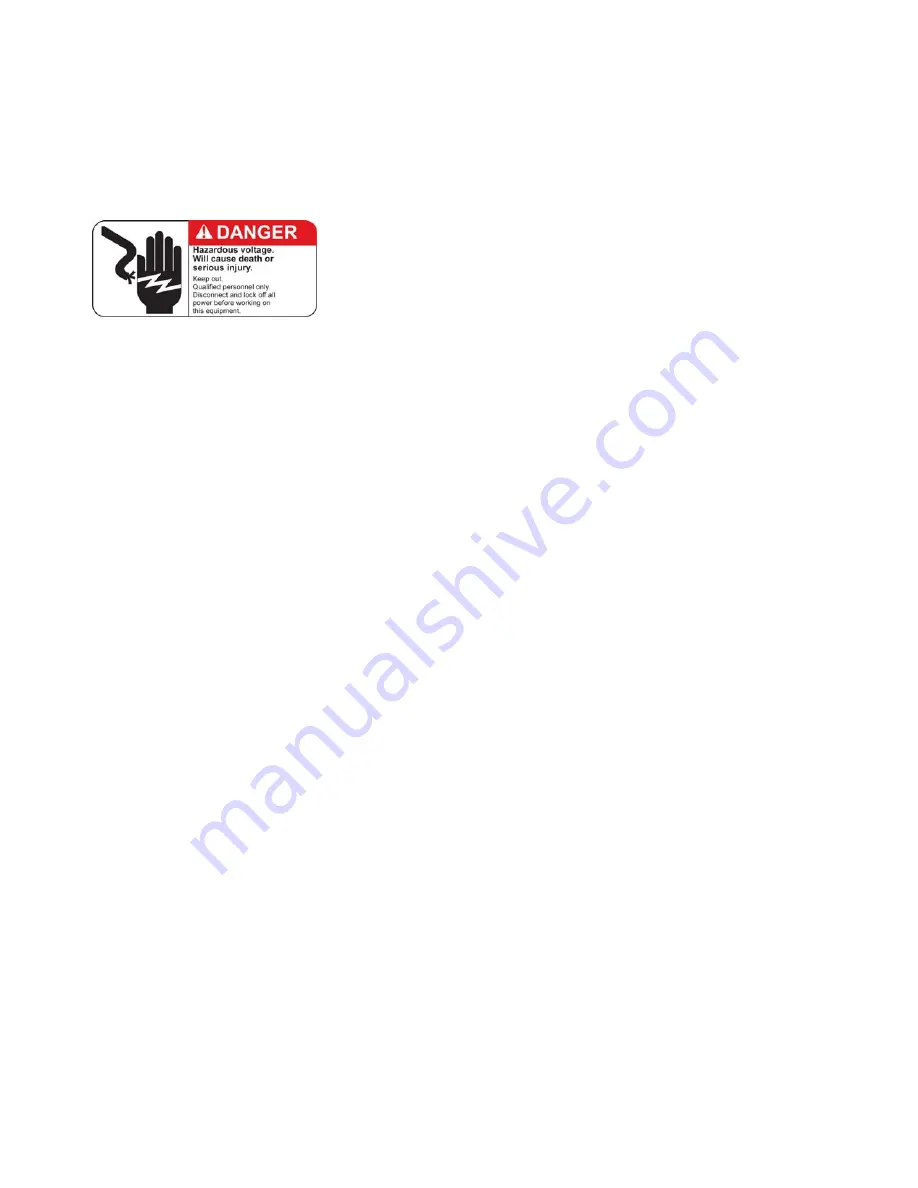
Safety Precautions
(a) Only qualified persons familiar
with the construction and operation
of this equipment should perform
work described in this set of
instructions. Such work should be
performed only after reading this
complete set of instructions.
(b) Follow safety related work
practices, as described in NFPA 70E,
part II, at all times.
(c) Hazardous voltages in electrical
equipment can cause severe personal
injury or death. Energizing this
equipment for the first time after
initial installation or maintenance is
potentially dangerous. Inspection
and maintenance should be
performed on this equipment and
equipment to which power has been
cut off, disconnected, and electrically
isolated so that no accidental contact
can be made with energized parts.
(d )Some types of electrical
equipment will cause harmonics in
the electrical system which may
result in overheating. Consider this
condition when determining this
equipment loading, as possible
de-rating of equipment may be
necessary.
Important
The information contained herein is
general in nature and not intended
for specific application purposes. It
does not relieve the user of
responsibility to use sound practices
in application, installation, operation,
and maintenance of the equipment
purchased. Siemens reserves the
right to make changes in the
specifications shown herein or to
make improvements at any time
without notice or obligations. Should
a conflict arise between the general
adhere to the following warnings:
(a)
Danger!
High Voltage. Qualified
personnel only. Lock off all power to
this equipment before working
inside. Always work on de-energized
equipment. Always de-energize
equipment before performing any
tests, maintenance or repair.
(b)
Warning!
Always perform
maintenance on the interrupting
device after the closing
mechanism(s) are discharged.
(c)
Caution!
Always let an interlock
device or safety mechanism perform
its function without forcing or
defeating the device.
(d)
Caution!
Hydrocarbon spray
propellants and hydrocarbon
compounds will cause degradation of
certain plastics. Contact your local
Siemens representative before using
these products to clean or lubricate
components during installation or
maintenance.
information contained in this
publication and the contents of
drawings or supplementary material
or both, the latter shall take
precedence.
Qualified Person
For the purpose of this manual and
product labels, a qualified person is
one who is familiar with the
installation, construction, operation
or maintenance of the equipment
and the hazards involved. In addition,
this person has the following
qualifications:
(a)
is trained and authorized
to
de-energize, clear, ground, and tag
circuits and equipment in accordance
with established safety practices.
(b)
is trained
in the correct care and
use of protective equipment such as
rubber gloves, hard hat, safety
glasses or face shields, flash clothing,
etc., in accordance with established
safety practices.
(c)
is trained
in rendering first aid.
Signal Words
The signal words
"Danger,"
"Warning"
and
"Caution"
used in this
manual indicate the degree of hazard
that may be encountered by the user.
These words are defined as:
Danger -
Indicates an imminently
hazardous situation which if not
avoided, will result in death or
serious injury.
Warning -
Indicates a potentially
hazardous situation which, if not
avoided, could result in death or
serious injury.
Caution -
Indicates a potentially
hazardous situation which, if not
avoided, may result in minor or
moderate injury.
Dangerous Procedures
In addition to other procedures
described in this manual as
dangerous, user personnel must
P1 Panel with i-3 Control Technology
TM
1