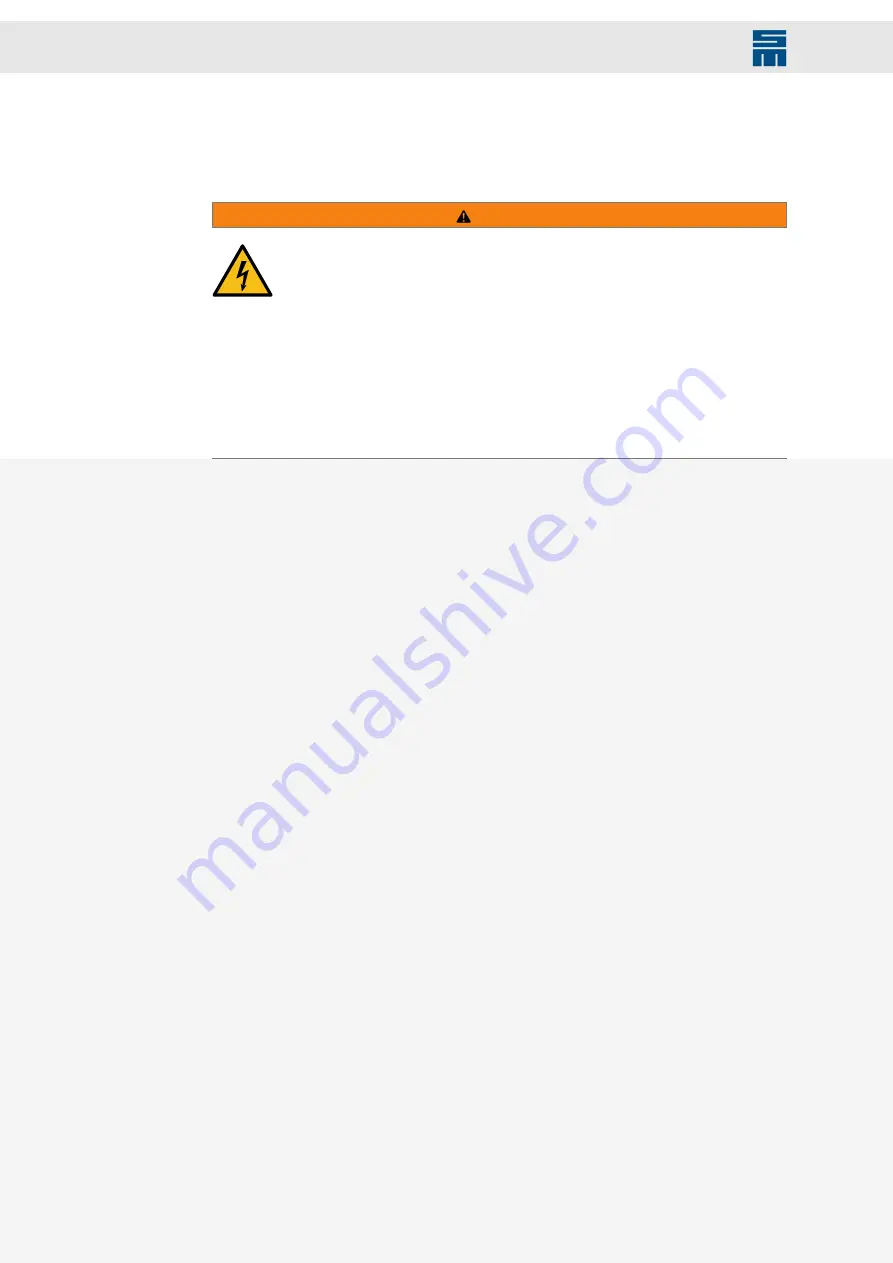
Safety Circuit / Restart Lock (STO)
12
Safety Circuit / Restart Lock
(STO)
WARNING
STO function acc. to EN ISO 13849-1:2008-12, DIN EN 62061:2005 SIL
3 not possible
The integrated safety circuit/restart lock (STO) of the device series SD2M
cannot completely guarantee the necessary safety parameters.
→ Therefore, please check whether or not the safety circuit/restart lock
(STO) is relevant for the safety concept of your machine. If that is the
case, you must implement the STO function by means of alternative
safety components. Otherwise the required safety level or machine
safety is not guaranteed.
→ For further information or if you have any questions, please do not
hesitate to contact us.
▶
according to EN ISO 13849-1:2008-12, DIN EN 62061:2005 SIL 3
The restart lock is provided for preventing an unintentional start of a speed-variable drive
from the standstill and can, for example, be used in the machine function “Safe stop”.
The stop function is used to shut down the drive in normal operation.
SIEB & MEYER drives provide a restart lock approved according to EN ISO 13849-1
and a stop function according to DIN EN 60204-1, stop category 0 (see stop categories
below). A stop category 1 can be achieved by using an approved safe emergency stop
device with delay or a safe PLC according to DIN EN 60204-1.
The stop functions are defined according to DIN EN 60204-1 (VDE 0113-1) paragraphs
9.2.1 and 9.2.2.3. The following categories of stop functions are available:
Category 0
Standstill by immediate interruption of the energy supply to the machine drives ele-
ments, i.e. uncontrolled standstill.
Category 1
A controlled standstill where the energy supply between motor and machine drive
elements is maintained to reach the standstill. The energy supply is interrupted at
that moment the machine is at a secure standstill.
Category 1b
A controlled standstill where the energy supply between motor and machine drive
elements is maintained to reach the standstill. The maintenance of the stop condi-
tion is monitored. If the stop condition is no longer applicable, the energy supply is
interrupted without creating a dangerous situation.
Category 2
A controlled standstill where the energy supply between motor and machine drive
elements is maintained.
Every machine must be equipped with a stop function according to category 0. Stop
functions according to category 1 and/or 2 must be integrated into the machine if they
are necessary for safety and/or operational reasons.
The disadvantages of the disconnection can be eliminated by the consequent use of
electronic elements. The DIN EN 60204-1 standard “Safety of machinery - Electrical
equipment of machines” also allows the use of electronic equipment for the stop function
in case of an emergency, if these – under application of the standards EN ISO 13849-1
and/or – meet the same safety requirements as required according to DIN EN 60204-1.
This approved safety circuit was conceived according to the concept paper by Drivecom
“Technical Guide for Safety Drives” from 04/23/2004. The concept paper was approved
by the BIA and the TÜV Rheinland: It was confirmed that the required standards and
regulations were met.
100
Drive System SD2M - Hardware Description 036228xxF
STO
function
acc.
to
EN
ISO
13849-1:2008-12,
DIN
EN
62061:2005
SIL
3
not
possible