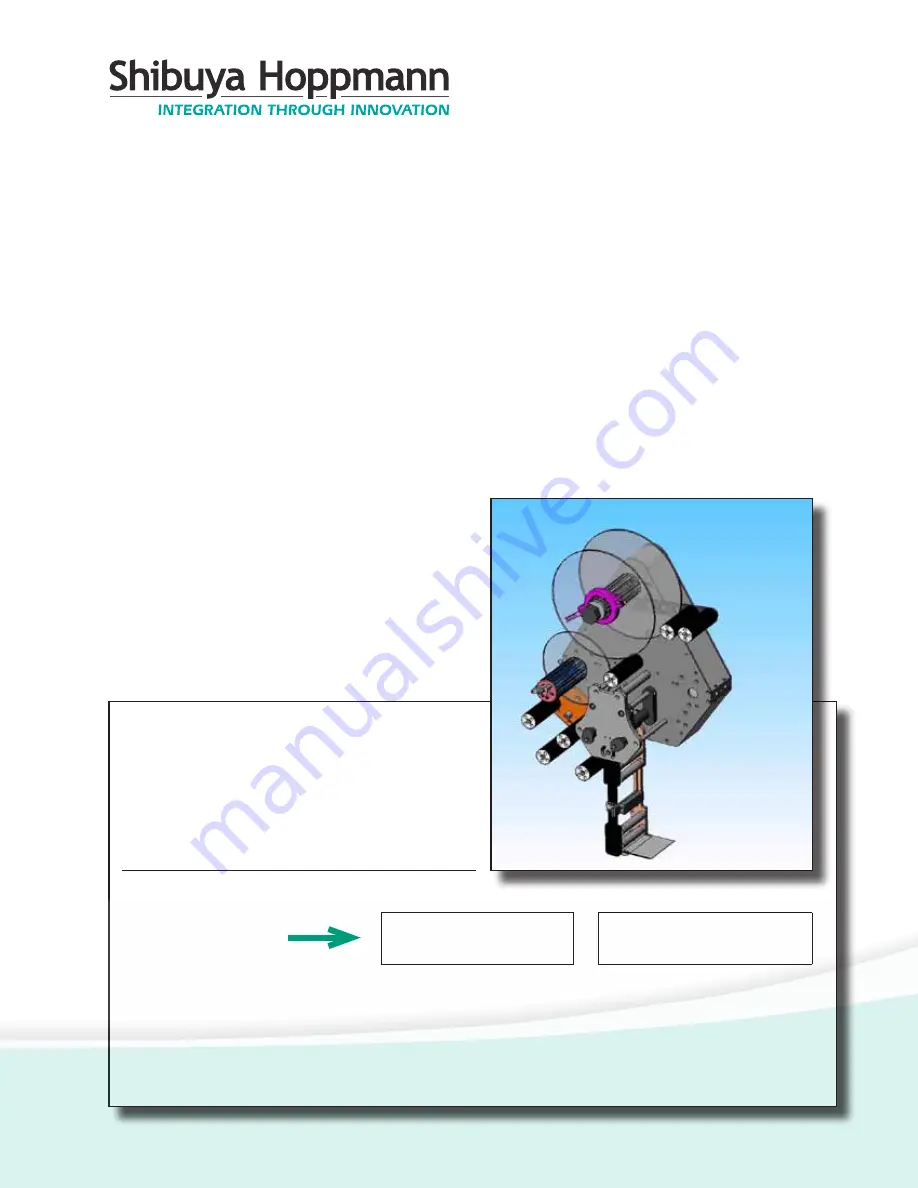
TM
L500A V2 High
Speed Labeler
Installation/Maintenance
Manual
Publication Version, Revision 1, All rights reserved.
© 2011 Shibuya Hoppmann Corporation
13129 Airpark Drive, Suite 120 • Elkwood, Virginia 22718 • USA
Tel: (540) 829-2564 • Fax: (540) 829-1726 • E-mail: [email protected]
Duplication of this manual, in whole or in part, requires written consent of Shibuya Hoppmann Corporation.
Model Name:
Model Inventory Number:
Refer all servicing to qualified personnel.
This manual is intended for use by qualified
mechanic and electricians who install or service
the L500A V2 High Speed Labeler.
Please copy this information from
the L500A V2 High Speed Labeler’s
serial plate.
Содержание L500A V2
Страница 12: ...L500A V2 High Speed Labeler Manual 12 Notes ...
Страница 14: ...L500A V2 High Speed Labeler Manual 14 Notes ...
Страница 22: ...L500A V2 High Speed Labeler Manual 22 Notes ...
Страница 50: ...L500A V2 High Speed Labeler Manual 50 Notes ...
Страница 80: ...L500A V2 High Speed Labeler Manual 80 Notes ...
Страница 84: ...L500A V2 High Speed Labeler Manual 84 Notes ...
Страница 89: ...89 Appendix Figure 8 1 Wiring Diagram 8 ...
Страница 90: ...L500A V2 High Speed Labeler Manual 90 Figure 8 2 Wiring Diagram ...