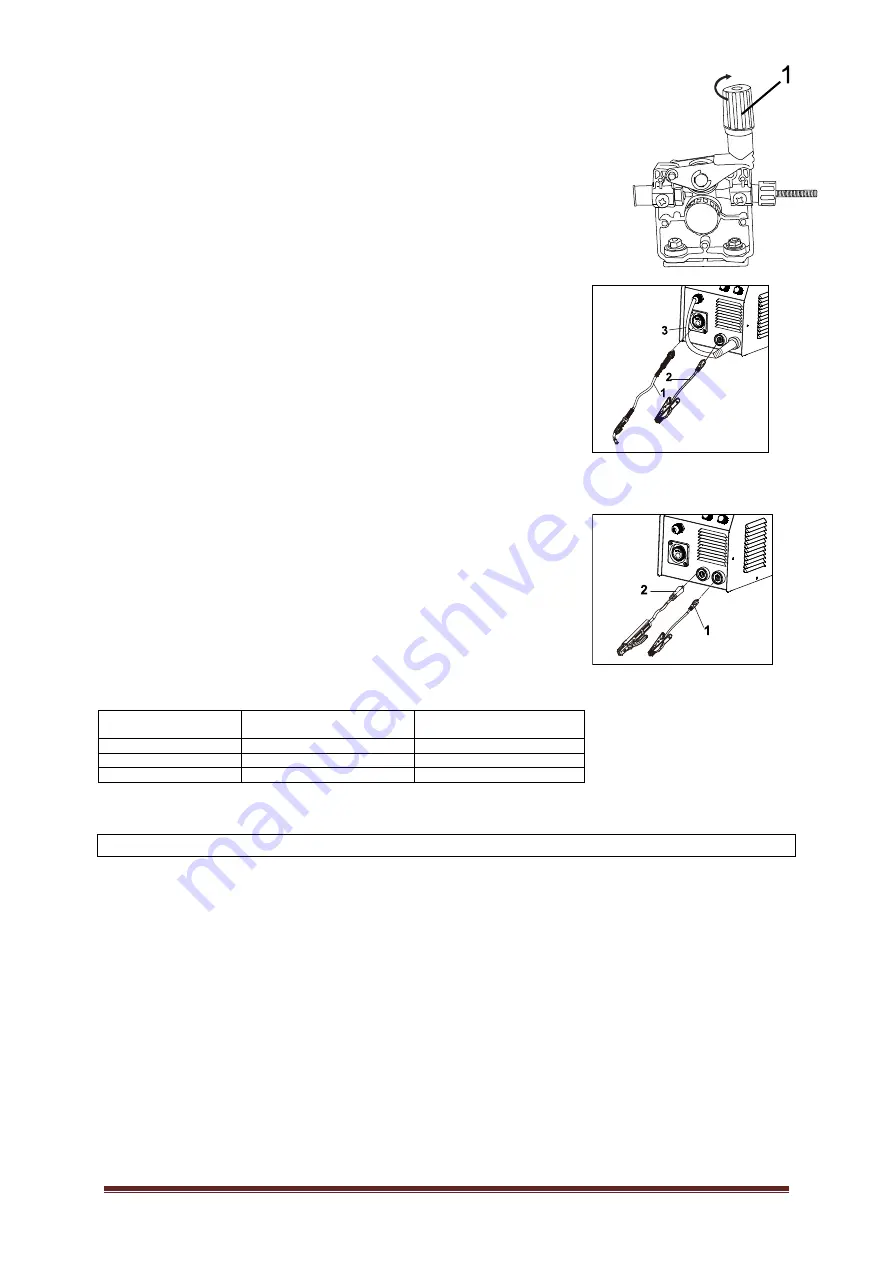
420 774 335 397 www.sharks-shop.cz Stránka 30
Setting Welding Roller
Turn the knob of the welding wire adjustment knob (1) to set the roller pressure. Do not
exert too much pressure. Higher pressure settings may cause the motor to lock and
power failure. Ensure that the pressure is set to smooth, gradually increase the
pressure until the wire is gradually transferred. Rotating the knob clockwise
increases the pressure. In the opposite direction the pressure is reduced.
Welding in shielding gas environment
1. Set the welding device switch to "ON". Open the gas bottle valve,
release the pressure bar, press the burner switch, and set the desired
flow rate.
2. Select the hole diameter of the welding torch according to the
diameter of the wire.
3. Depending on the thickness and technique of the workpiece, set the
rotary push-button and the speed button to the desired position.
4. Electric arc buttons are used to adjust softness and arc hardness to
achieve the best welding effect; If the current is small, it is difficult to
reduce the arc when arcing is interrupted. At high currents, the electric
arc must be soft to reduce splashing
5. Connect the earthing terminal to the workpiece, when the burner switch is pressed, the welding
machine works, if the burner switch releases the burner, the machine stops working.
Manual Arc Welding (MMA)
Connect the welding wires.
Press and rotate the electrode holder cable to the welding electrode
clamp (+ contact), press and rotate the grounding cable to the
grounding terminal (-). Connect the ground terminal as close as
possible to the welding point.
Adjust the welding current.
Turn the current control knob to set the desired value. For the optimal
current selection mode for material thickness and electrode diameter,
use the table below.
Output current(A)
diameter
of
the
electrode(
Φ
,
мм
)
thickness of the material
(
мм
)
20-50
1.6-2.5
1.0-2.0
50-130
2.5-3.2
2.0-4.0
130-160
3.2-4.0
4.0-8.0
MAINTENANCE
- Any work on the instrument, including repairs, may only be performed by a qualified technician.
During the warranty period, repairs may only be performed by an authorized Sharks Service.
• Always unplug the unit and wait for the fan to stop. There are residual high voltages and currents
inside the device that can endanger life.
• It is recommended to periodically remove the unit cover and bleed it with compressed air at low
pressure. At the same time, check the contact state with an isolated tool.
• Check the cables regularly. Cables should not have cracks or cuts.
• Avoid getting metal particles into the machine, as this may cause a short circuit or damage to the
unit.
• When transporting and storing the welding machine, try to protect it from moisture. It is
recommended to store the welding machine in a dry, well-ventilated place and not to expose it to high
humidity, away from flammable substances and dust.