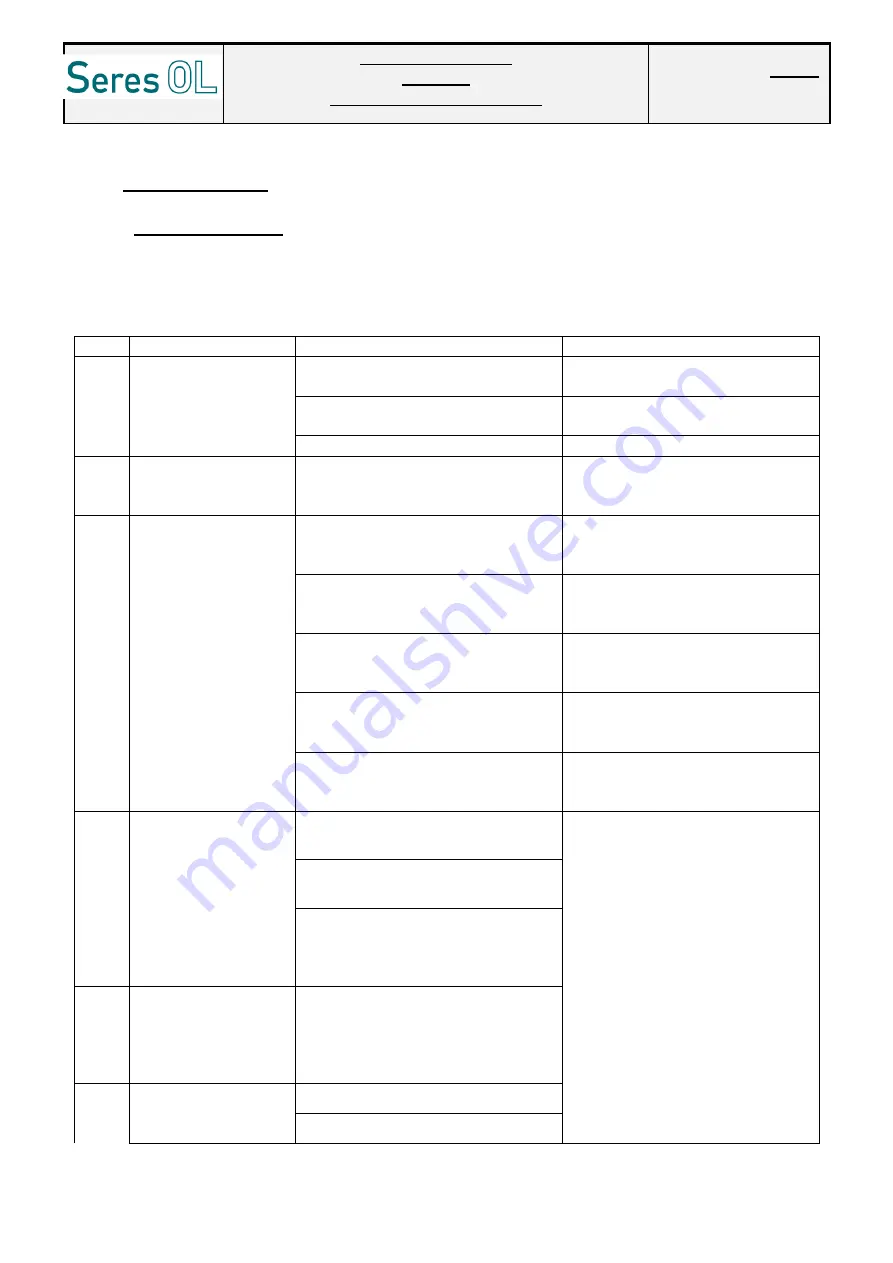
TOC EVOLUTION:
USER &
MAINTENANCE MANUAL
Page:
72/74
Instructions No.: 10844
This document is the property of SERES and cannot be reproduced without authorization
12 Repair manual
12.1 Failure diagnosis
The following tables list the most common failures and their solutions. To prevent a failure, ensuring the
cleanliness of the different components is essential. It will be necessary, before any failure diagnosis, to clean them
before removing them. We suggest you read the troubleshooting instructions before working on the detector.
No.
Problems
Possible causes
Solutions
1
The device cannot be
switched on.
Power failure or fuses outside the
terminal strip.
Check the power supply voltage or
that the fuses are installed properly.
The power supply is off-line.
Check the power supply output
(24V).
The touch screen is not powered.
Check the power supply connector.
2
The application does
not start.
The device starts up but not the
interface.
Check that the screen is powered
and check that the Ethernet cables
are connected.
3
The "water defect"
alarm is generated
when the sample is
provided correctly
(correct flow rate and
pressure at the
sampling point).
The filling solenoid valve does not
operate correctly.
Check that the filling solenoid valve
is connected properly and that the
LED lights up.
One or more hydraulic pipes are
blocked or pinched.
Check the condition of the pipes.
The supply feed pump is not working.
Check that the pump is connected
correctly.
The water sensor on the fast loop is
faulty.
Check that the sensor is connected
and that the sensor is not blocked.
The water sensor is faulty.
Check that the sensor is connected
and that the pipe is correctly clipped
onto the sensor.
4
The reactor does not
empty itself.
The sewer system is blocked.
Check the condition of the pipes
(internal and external).
The draining solenoid valve does not
operate correctly.
Check that the solenoid valve is
connected correctly.
The draining pipe is pinched and
prevents flowing.
Check that the draining pipe is not
pinched when the door is closed. If it
is pinched, unblock it. Possibly
shorten the pipe.
4
The measurement is
not updated.
The new measurement is identical to
the first or the measuring cycle is
stopped or paused.
Restart the measuring cycle.
5
The screen is not
responding.
The touch screen is damaged.
Switch the device OFF and then ON.
If the problem persists, contact the
after sales department.
The PC PNAL does not respond.