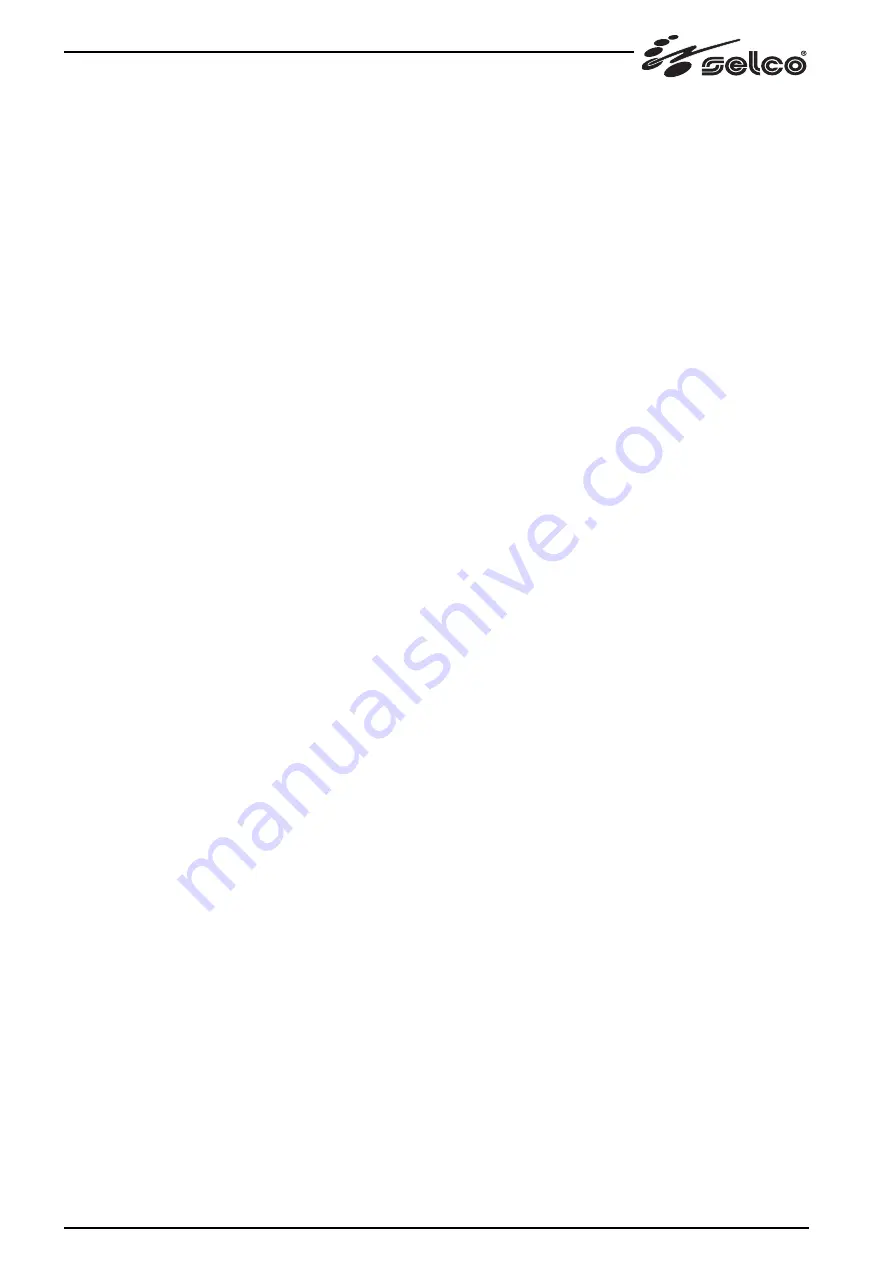
98
Description of machine operation
The connector for connection of the RC16 and RC12 remote
controls is also provided.
For operation in MMA, see previous directions.
With the selector set to TIG H.F., operation is as follows.
With the selector set to TIG 2-strokes, the sequence is as fol-
lows:
1st stroke - Torch button pressed: opening of gas solenoid
valve and, after a settable pre-gas time, triggering of H.F. (if
the arc is not sparked, the H.F. is maintained for approxima-
tely 1.5 sec) and power command (possible slope-up).
2nd stroke - Torch button released: current descent ramp
followed by inverter switch-off while the solenoid valve is
kept open for a variable time (post-gas time).
With the selector set to TIG 4-strokes, we have the following
sequence:
1st stroke - Torch button pressed: gas solenoid valve opens.
2nd stroke - Torch button released: H.F. triggered (if the arc is
not sparked, the H.F. is maintained for approximately 1.5
sec.) and power command (possible slope-up).
3rd stroke - Torch button pressed: current descent ramp fol-
lowed by inverter switch-off while the solenoid valve is kept
open.
4th stroke - Torch button released: the solenoid valve is kept
open for a variable time (post-gas time).
With the selector set to TIG bilevel the sequence is as follows:
1st stroke - Torch button pressed: opening of gas solenoid
valve and, after a settable pre-gas time, triggering of H.F. (if
the arc is not sparked, the H.F. is maintained for approxima-
tely 1.5 sec) and power command with welding current level
equal to initial current (= % of welding current).
2nd stroke - Torch button released: welding current level
equal to level set I (possible slope-up).
Bilevel - Torch button pressed and immediately released: wel-
ding current level equal to I2 (without slope).
Bilevel - Torch button pressed and immediately released: wel-
ding current level equal to I (without slope).
.
3rd stroke - Torch button pressed: current slope down. At the
end of slope down, the current is maintained equal to the
final current If.
4th stroke - Torch button released: the inverter switches off
and the solenoid valve is kept open for a variable time (post-
gas time).
With the selector set to TIG LIFT, operation is the same as TIG
H.F. with the following variations in the initial triggering phase.
With the selector set to TIG 2-strokes:
1st stroke - Torch button pressed and torch in contact with piece:
opening of gas solenoid valve and, after a settable pre-gas time,
power command with current limited to approximately 30A (the
current reaches the set level when the electrode is lifted).
With the selector set to TIG 4-strokes:
1st stroke - Torch button pressed and torch in contact with
piece: opening of gas solenoid valve.
2nd stroke - Torch button released: power command with
current limited to approximately 30A (the current reaches the
set level, possibly with slope up, when the electrode is lifted).
With the selector set to TIG bilevel the sequence is as follows:
1st stroke - Torch button pressed and torch in contact with the
piece: opening of gas solenoid valve and, after a settable pre-gas
time, power command with current limited to approximately
30A.
When the torch is raised the welding current reaches the
initial current value (=% of welding current).
On board 15.14.236, but accessible only with the machine
open, there is also a welding current maximum calibration
potentiometer with reference provided by the remote control.
The torch button command arrives at the same board
(15.14.236). This command is electrically disconnected by relay
from the electronic control and adjustment circuits.
The board generates the following voltages inside (referring to
different grounds):
+5 Vdc (command circuits power supply)
+24 Vdc (torch button insulation relay power supply)
+5 Vdc (remote controls RC12 and RC16 power supply)
converting the input voltages supplied by the auxiliary transformer (l):
9 Vac
24 Vac
It also receives the voltages (ground with same +5 Vdc power
supply as above command circuits) :
+15 Vdc
-15 Vdc
from board 15.14.254 .
Содержание Genesis 240 TLH
Страница 1: ...REPAIRS MANUAL E N G L I S H Genesis 240 Genesis 240 TLH...
Страница 9: ...Description of machine operation 91 n m k a o q r l c b i p j d s e f g h e FIG 6...
Страница 11: ...Description of machine operation 93 n m k a o q r l c b i p j d s e f g h e FIG 8...
Страница 20: ...102 Description of machine operation n m k a o q r l c b i p j d s e f g h e FIG 16 F1 F2 FIG 17...
Страница 22: ...LAY OUTS OF CARDS...
Страница 23: ...Lay outs of cards 105 Card 15 14 233 Fig 20...
Страница 24: ...106 Lay outs of cards Card 15 14 236 side A Fig 21...
Страница 25: ...Lay outs of cards 107 Card 15 14 236 side B Fig 22...
Страница 26: ...108 Lay outs of cards Card 15 14 236 side C Fig 23...
Страница 27: ...Lay outs of cards 109 Card 15 14 254 side A Fig 24...
Страница 28: ...110 Lay outs of cards Card 15 14 254 side B Fig 25...
Страница 29: ...Lay outs of cards 111 Card 15 14 254 side C Fig 26...
Страница 30: ...112 Lay outs of cards Card 15 14 254 side D Fig 27...
Страница 31: ...Lay outs of cards 113 Card 15 14 192 Fig 28...
Страница 32: ...114 Lay outs of cards Card 15 14 239 Fig 29...
Страница 33: ...Lay outs of cards 115 Card 15 14 240 Fig 30...
Страница 42: ...124 Diagnosis procedure Card 15 14 254 soldering side FIG 35A Card 15 14 254 soldering side FIG 35B...
Страница 58: ...140 Diagnosis procedure J9 connector frontal side FIG 36 Card 15 14 192 FIG 37...
Страница 59: ...Diagnosis procedure 141 FIG 38 Card 15 14 233 FIG 39...
Страница 60: ...142 Diagnosis procedure Card 15 14 254 version 1 soldering side FIG 40A...
Страница 61: ...Diagnosis procedure 143 Card 15 14 254 version 2 soldering side FIG 40B soldering side view...
Страница 62: ...144 Diagnosis procedure Card 15 14 236 FP106 FIG 41...
Страница 63: ...Diagnosis procedure 145 FIG 43 H F 15 14 192 wring diagrama FIG 42...
Страница 64: ...146 Oscillograms Oscillogram 1 Oscillogram 2...
Страница 65: ...Oscillograms 147 Oscillogram 3 Oscillogram 4...
Страница 66: ...148 Oscillograms Oscillogram 5 Oscillogram 6...
Страница 67: ...Oscillograms 149 Oscillogram 7 Oscillogram 8...
Страница 68: ...150 Oscillograms Oscillogram 9 Oscillogram 10...
Страница 69: ...Oscillograms 151 Oscillogram 11...
Страница 73: ...Parts dismantling and re installation procedure 155 FIG 44...
Страница 74: ...156 Parts dismantling and re installation procedure FIG 45...
Страница 75: ...Parts dismantling and re installation procedure 157 FIG 46 FIG 47...
Страница 76: ...158 Parts dismantling and re installation procedure FIG 48...
Страница 79: ...Operating tests and settings 161 Card 15 14 239 FIG 49...
Страница 80: ...162 Operating tests and settings Card 15 14 254 FIG 50...
Страница 81: ...Operating tests and settings 163 FP106 FIG 51...