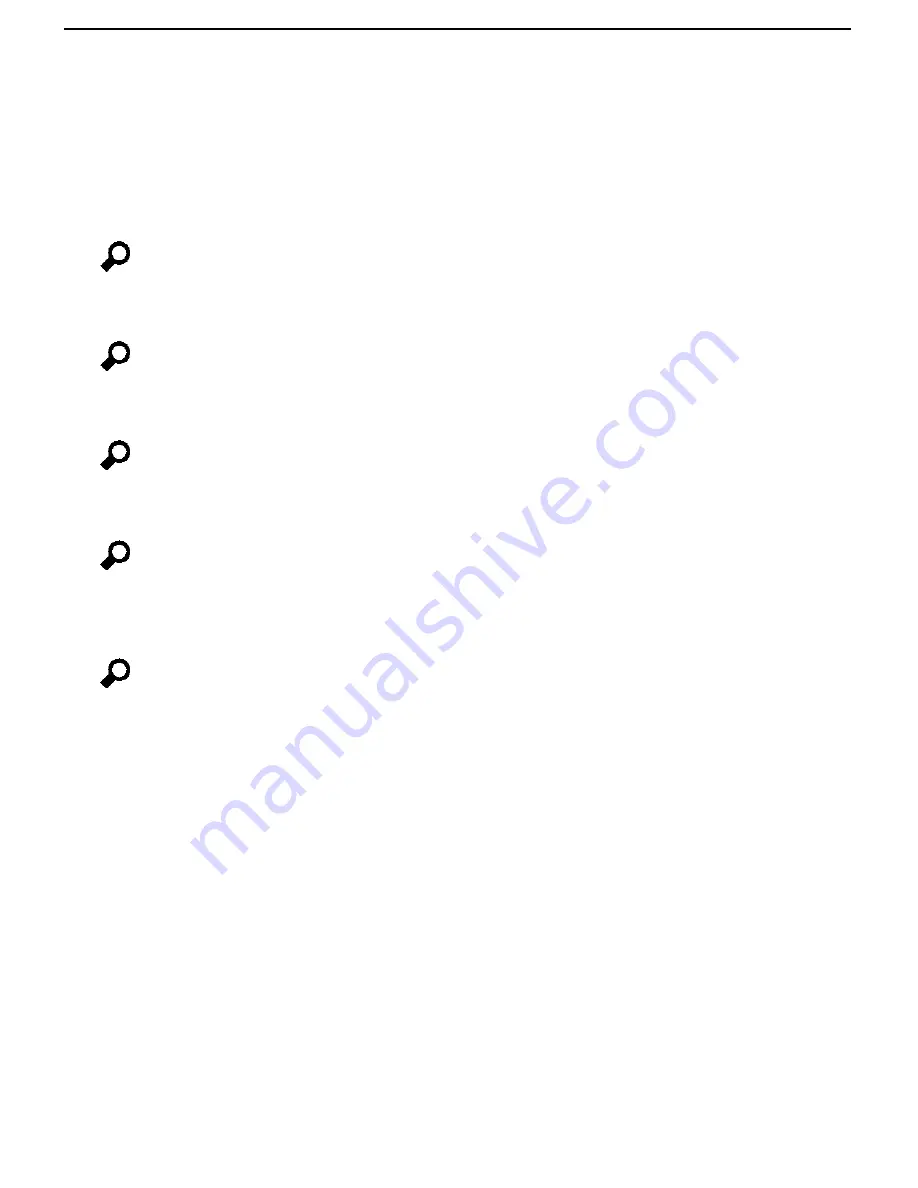
52
c)
Remove the pH neutralizer filter bowl from the pH neutralizer filter, drain the product water from it and clean
the inside of the bowl. Replace the pH neutralizer bowl back onto the pH neutralizer filter.
d)
Disconnect the top and bottom tube fittings from the ultraviolet sterilizer and drain the product water from
the UV sterilizer chamber. Reconnect the top and bottom tube fittings back onto the UV sterilizer.
e)
Disconnect the freshwater line from the potable water storage tank to the freshwater flush pump or, if a valve
is installed in this line, close it to isolate the potable water line from the freshwater flush pump.
f)
f) Remove the freshwater flush charcoal filter bowl; drain and clean the inside of the bowl. Replace the
freshwater flush charcoal filter element with a new Sea Recovery freshwater flush charcoal filter element,
and replace the bowl with new element back onto the housing.
The system may now be left unattended for up to 3 to 6 months. With ideal conditions, including a relatively
new RO Membrane Element, a clean system prior to storage, cool temperatures and no leakage of
storage chemical
within the system, it provides protection for up to 6 months. Adverse conditions may provide less
protection. Evaluate these factors before determining the proper interval between repeated rinsing and
storage periods.
RO Membrane Element Cleaning Procedures
Important: Do not arbitrarily clean the RO Membrane in a new system. If a new system experiences low
production or high salinity, then the system should be operated for up to 48 hours continuously to clear and
saturate the RO Membrane Element product water channel. If a new system still experiences low production
and or high salinity after 48 hours of continual operation, then contact the factory.
Important: The membrane element requires cleaning from time to time. Biological growth and salt accumulation
eventually make replacement necessary. The frequency of required cleaning depends on the amount of
production loss and salt-rejection loss resulting from normal use and exposure to feed water. In order to
properly assess performance changes, it is important to maintain daily log readings for comparison.
Important: During performance comparisons, feed water temp, feed water salinity and system operating
pressure must be taken into consideration and compensated for. After compensations, a 10% decline in
productivity (GPH Flow) and/or a 10% increase in salt passage indicate that the RO Membrane Element may
require cleaning.
Important: If the production rate has dropped dramatically since the last time the system was used, this may be due to
drying out of the RO Membrane Element and/or fouling during storage. If the system has not been used for several months
and the production rate has dropped dramatically since the last time used, try operating the system for 48 or more
continuous hours to saturate the product water channel within the RO Membrane Element.
Important: A dramatic increase in product water production from one day to the next may be the result of a
mechanical failure such as a broken O-ring or damaged RO Membrane Element.
RO Membrane Element Cleaning Water and Chemical Requirements
1. The Sea Recovery cleaning compounds are designed to clean in a closed loop configuration moderate fouling
from the RO Membrane Element. If the RO Membrane Element is excessively fouled and in-field cleaning is
not successful, the RO Membrane Element may be returned to Sea Recovery or to one of Sea Recovery’s
many service dealers for professional chemical cleaning. If your membrane requires professional cleaning,
please contact Sea Recovery for a return authorization number, price quotation and return instructions. Note:
Very heavily fouled RO Membrane Elements may be more cost-effective to replace rather than clean as the
cleaning process will take several hours of labor, chemical cost and packaging and shipping charges to and
from the factory.
2. SRC MCC-1, Membrane Cleaning Compound "No. 1" is an alkaline cleaner designed to clean biological fouling
and slight oil fouling from the RO Membrane Element. Biological fouling is usually the first cause of the RO
Membrane Element fouling. The system is constantly exposed to seawater and biological growth. If exposed
to seawater and left to sit, the RO Membrane Element becomes fouled even with no actual system use. This
Ultra Whisper 400-600
Содержание Ultra Whisper Compact 400
Страница 2: ......
Страница 3: ...Ultra Whisper 400 600 Owner s Manual Manual PN B651380001D...
Страница 4: ......
Страница 8: ......
Страница 18: ...1 6 UltraWhisper400 600...
Страница 24: ...22 UltraWhisper400 600...
Страница 36: ......
Страница 37: ......
Страница 38: ......
Страница 48: ...46 UltraWhisper400 600...
Страница 58: ......
Страница 59: ......
Страница 60: ......
Страница 66: ...Ultra Whisper 400 600 64...
Страница 71: ...Chapter 12 Exploded Parts View 69...
Страница 81: ...79 7 8 6 4 1 3 1 2 4 9 5...
Страница 89: ...Exploded Parts View 5 11 22 17 13 2 1 16 15 12 14 20 10 19 4 16 18 21 9 7 24 6 8 3 18 5 21 23 87...
Страница 97: ...95 Exploded Parts View 6 7 5 2 3 2 4 10 5 8 9 1...
Страница 99: ...12 8 9 2 10 13 1 3 5 4 14 11 6 15 7 97...
Страница 105: ...Chapter 13 Appendix 103...
Страница 106: ......
Страница 107: ......
Страница 108: ......
Страница 109: ......
Страница 110: ......
Страница 111: ......
Страница 113: ......
Страница 118: ......
Страница 119: ......
Страница 120: ......