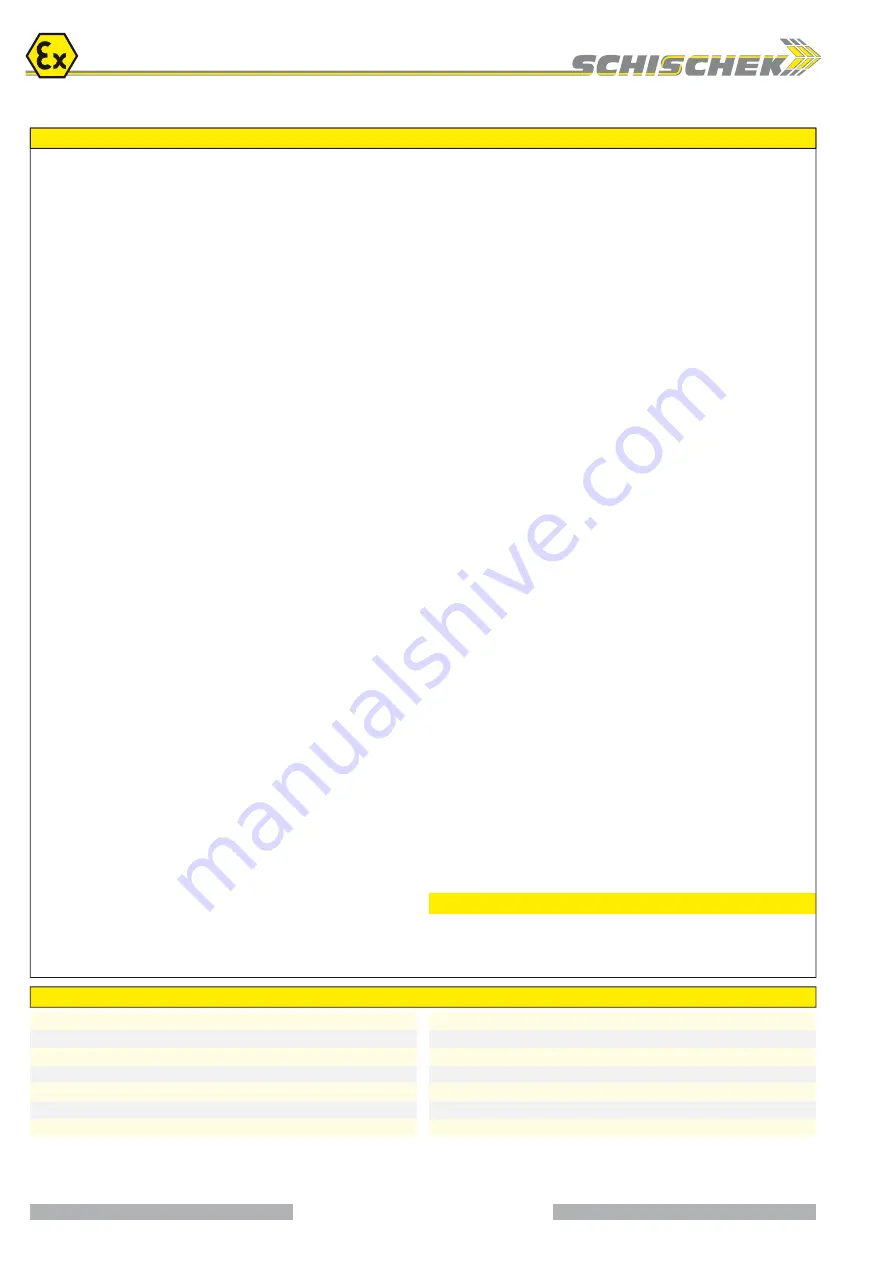
E X P L O S I O N P R O O F
www.schischek.com
Schischek GmbH
Germany, Muehlsteig 45, Gewerbegebiet Sued 5, 90579 Langenzenn, Tel. +49 9101 9081-0, Fax +49 9101 9081-77, E-Mail [email protected]
ExMax-S-F1_en
V07 – 19-Oct-2021
ExMax-...-F1
ExMax-...-SF1
ExMax-...-BF1
Special options
... -CTS
... -VAS
Important information for installation and operation
Extra information (see additional data sheet)
Additional technical information, dimensions, installation intruction, illustration
and failure indication
A. Installation, commissioning, maintenance
All national and international standards, rules and regulations for hazardous Ex-areas
must be complied with. Certified apparatus must be installed in accordance with manufacturer
instructions. If the equipment is used in a manner not specified by the manufacturer, the
safety protection provided by the equipment may be impaired. For electrical installations
design, selection and erection, EN/IEC 60079-14 can be used.
For electrical connection an Ex-e terminal box is required (e.g. ExBox-...).
Attention:
If the actuator is put out of operation all Ex rules and regulations must be
applied. You have to cut the supply voltage before opening the terminal box!
The cables of the actuator must be installed in a fixed position and protected against
mechanical and thermical damage. Connect potential earth. Avoid temperature transfer
from armature to actuator! Close all openings with min. IP66.
For outdoor installation a protective weather shield against sun, rain and snow should be
applied to the actuator as well as a constant supply at terminal 1 and 2 for the integrated
heater. During commissioning apply a self adjustment drive.
Actuators are maintenance free. An annual inspection is recommended. For electrical
installations inspection and maintenance, EN/IEC 60079-17 can be used. Ex-actuators
must not be opened by the customer.
B. Manual override
Manual override only if supply voltage is cut. Use delivered socket wrench with slow
motions, usage can be tight.
Attention:
Releasing or letting go the Allen key too fast at manual operating actuators
with spring return causes risk of injury!
C. Shaft connection, selection of running time
Actuators are equipped with a direct coupling double square shaft connection of 12 × 12 mm.
For round shafts adaptors/clamping connection (accessories, e.g. KB-S) are available.
The housing of the actuator is axially symmetrically built to select Open-close direction
of the spring return function by left-right mounting. Using the 10-position switch different
motor running times and spring return running times can be selected on site in acc. to
the actuator type.
D. Temperature trigger ...Pro-TT-...
The actuator ...Max-...-BF1 will work only with the temperature trigger ExPro-TT-...
E. Operation with 3 sec. motor running time
Note following:
1. The 3 sec. motor running time mode is only available in switch position 0 and 5 and
at a constant supply voltage applied for a minimum of 1 minute on terminal 1 and 2.
2. The actuator opens at voltage on terminal 3 (resp. closes) and closes at voltage on
terminal 4 (resp. opens) – depending on mounting position of the actuator.
3. The max. duty ratio is 10 % resp. 1 cycle/minute. Between two fully 3 sec. cycles in
the same direction there must be a minimum intermission of 1 minute. Trying to run
the actuator in the same direction in less than the required minimum of 1 minute the
function will be blocked for the rest of the idle period. Later the release for the next
cycle is made automatically by an internal timing relay.
4. Same function is applied on spring return actuators, fail safe operation is regarded
same as a motor running cycle.
5. Trying to use the 1 wire On-off methode in switch position 0 and 5, software changes
the motor running time temporarily and automatically to 15 s/90° to protect the actuator
for overheating due to uncontrolled duty ratio.
F. Spring return
Spring return function works only if the supply voltage for terminal 1 or 2 is cut. In the
event of an electrical interruption, the spring returns to its end position even if supply
voltage is available again during return function. Thereafter operation will continue.
G. Operation at ambient temperatures below −20 °C
All actuators are equipped with a regulated integrated heating device designed for
employments down to
−
40 °C ambient temperature. The heater will be supplied automatically
by connecting the constant voltage supply on the clamps 1 and 2.
1. After mounting the actuator must be immediately electrically connected.
2. The heater switches on automatically when actuator reaches internally
−
20 °C. It
heats up the actuator to a proper working temperature, then heater switches off
automatically. Actuator will not run during heating process.
3. The adjustment options are only ensured after this heating up period.
H. Excess temperatures
In acc. to the ATEX rules and regulations Ex actuators must be protected against excess
temperature. The internal thermostat works as a maximum limiter and, in the event of
failure at incorrect temperatures, shuts off the actuator irreversible. An upstream connected
temperature sensor stops the actuator before reaching its max. temperature. This safety
feature is reversible, after cooling down the actuator is completely functional again. In
this case the failure must be eliminated immediately on site!
I. Synchron mode
Do not connect several actuators to one shaft or link mechanically together.
J. Mechanical protection
Actuators must be operated with a minimum external load.
After installing the actuator to the damper/armature a self adjustment drive has to be
performed in order to protect the damper/armature against mechanical overload.
During operation the actuator reduces briefly its speed (motor power) before reaching
the end position for a “gentle” blockade/stop.
K. Intrinsically safe circuits
The actuator has a flameproof enclosure acc. to EN 60079. The supply of the push
button (adjustment drive), the 10-position switch (adjustment of torque and running time),
the LED indicator and the sensor connection ExPro-TT is performed intrinsically safe!
L. Routine tests of fire dampers
For periodic inspection of fire dampers cut off the supply line (current of actuator).
The test button at ExPro-TT-... is only used for test purposes of actuator’s function.
Special solutions and accessories
...-CTS
Types in aluminium housing with seawater resistant coating
...-VAS
Types in stainless steel housing, parts nickel-plated
Adaptions
for dampers and valves on request
ExMax-...-S3
Ambient temperature up to +60 °C (T4), 110...240 VAC/DC, 25 % ED
ExPro-TT-...
Safety temperature trigger for fire dampers
ExBox-...
Ex-e terminal boxes for zone 1, 2, 21, 22
MKK-S
Mounting bracket for boxes type ...Box-... directly on actuator
ExSwitch
2 external aux. switches, adjustable for zone 1, 2, 21, 22
KB-S
Clamp for damper shafts Ø 10...20 mm and
□
10...16 mm
AR-12-xx
Reduction part for 12 mm square connection to 11, 10, 9 or 8 mm shafts
BSH-S
Mounting holder for actuators in fire danger areas
Kit-S8
Cable glands nickel-plated
4 / 4