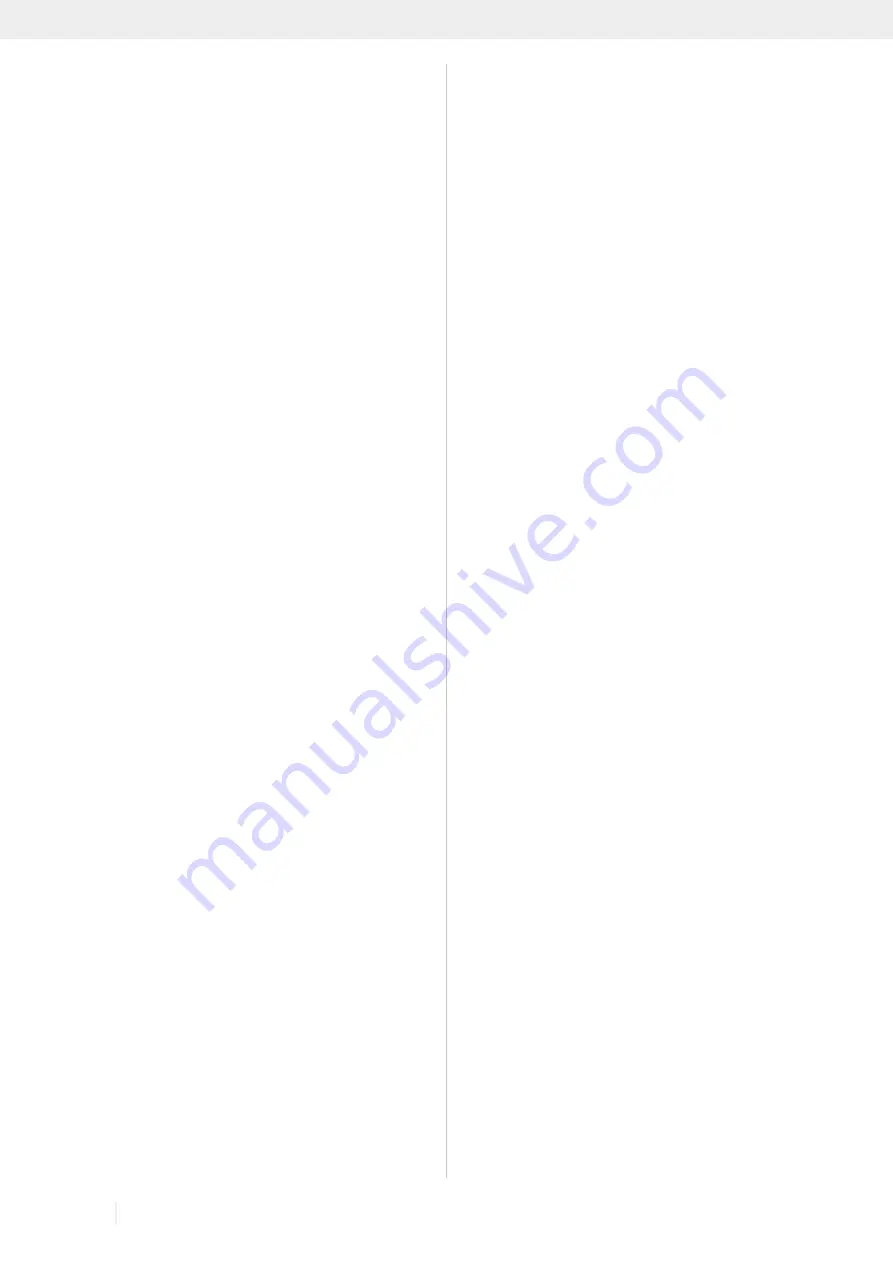
10
GB/IE/NI
9.4 Fitting/removing the saw blade guard
(fig. 13+14)
1. Loosen the screw with nut and washer (27) of the saw
blade guard (2). Place the saw blade guard (2) onto the
riving knife (3) from above.
2. Fit the screw with nut and washer (27) such that the screw
sits firmly in the elongated hole.
3. Do not over-tighten the screw (27). The saw blade guard
must remain free to move.
4. Disassembly takes place in reverse order.
m
WARNING:
Before starting sawing, the saw blade guard
(2) must be lowered onto the material to be sawn.
After fitting, check that the saw blade guard (2) is function-
ing properly. Lift the saw blade guard and then release it. The
saw blade guard should automatically move back to its starting
position.
9.5 Adjusting the riving knife (fig. 13-15)
m
WARNING:
Pull out the mains plug.
m
WARNING:
The setting of the saw blade (4) must be
checked after every saw blade replacement.
1. Set the saw blade (4) to the max. cutting depth, move to
the 0° position and lock in place.
2. Remove the saw blade guard (2) (see 9.4).
3. Loosen the two countersunk head screws of the table inlay
(25) and pull out the table inlay (5).
4. Loosen the riving knife fixing screw (26). Use the size 10
open-ended spanner (g) provided for this.
5. Slide the riving knife (3) upwards.
6. The distance between the saw blade (4) and the riving
knife (3) should be 3-5 mm (fig. 15).
7. Tighten the riving knife fixing screw (26) again and fit the
table inlay (5).
8. Mount the saw blade guard (2) with the screw with nut
and washer (27).
9.6 Connecting an extraction device (fig. 2)
1. Connect a suction hose to the suction adapter (16). Se-
cure the suction hose with a hose clamp (not included in
the scope of delivery) if necessary, to prevent it slipping off
the suction adapter (16).
2. A household vacuum cleaner is not suitable for use as an
extraction device. Use a multi-purpose suction device or
an extraction system designed specifically for sawdust.
10. Handling the equipment
10.1 On/off switch (fig. 3)
• It is possible to switch the saw on by pressing the green “I”
button. Before starting sawing, wait until the saw blade has
reached its maximum speed.
• In order to switch the saw off again, it is necessary to press
the red “0” button.
10.2 Setting the cutting depth (fig. 1+3)
The saw blade (4) can be adjusted to the required cutting
depth by turning the hand wheel (9).
• Counter-clockwise:
Greater cutting depth
• Clockwise:
Smaller cutting depth
Check the setting with a test cut.
10.3 Setting the angle (fig. 1, 17, 21, 22)
Angled cuts of 0°-45° to the left of the parallel stop (14) can
be carried out with the circular table saw.
m
Before making every cut, check that no collision can occur
between the stop rail (30), transverse stop (31) and the saw
blade (4).
1. Loosen the locking handle (7).
2. Set the desired angle on the scale by turning the hand wheel
(9).
3. Lock the locking handle (7) at the desired angle setting.
10.4 Using the parallel stop
(fig. 17-23)
10.4.1 Setting the stop height (fig. 17+18)
• The stop rail (30) of the parallel stop (14) has two guide
surfaces at different heights.
• Depending on the thickness of the material to be cut, the stop
rail (30) must be used for thick material (workpiece thickness
exceeding 25 mm) and for thin material (workpiece thick-
ness below 25 mm).
10.4.2 Turning the stop rail (fig. 17)
1. To turn the stop rail (30), first loosen the knurled nuts (i).
2. The stop rail (30) can now be pulled off the parallel stop
(14) and then slid over this again with the corresponding
guide.
3. Tighten the knurled nuts (i) again.
4. The stop rail (30) can be attached to the left or right of the
parallel stop (14) as required. To do this, only mount the
screws from the other side of the parallel stop (14).
10.4.3 Setting the cutting width (fig. 18+19)
The parallel stop (14) must be used when cutting sections of
wood lengthways.
1. Place the parallel stop (14) from above on the guide rail
(15) for the parallel stop (14).
2. 2 scales are printed on the guide rail (15) for the parallel
stop (14), which show the distance between the parallel
stop (14) and the saw blade (4).
3. Select the appropriate scale depending on whether the
stop rail (30) has been turned for processing thicker or
thinner material:
High stop rail: thick material
Low stop rail: thin material
4. Set the parallel stop (14) to the desired dimension on the
sight glass and use the eccentric lever (13) for the parallel
stop (14) to fix in place.
10.4.4 Setting the stop length (fig. 20)
In order to avoid the material to be cut becoming jammed, the
stop rail (30) can slide in a longitudinal direction.
Rule of thumb: The rear edge of the stop should intersect an
imaginary line that starts roughly at the centre of the saw blade
and runs to the rear at 45°:
1. Set the required cutting width.
2. Loosen the knurled nuts (i) and slide the stop rail (30) far
enough forward that it touches the imaginary 45° line.
3. Tighten the knurled nuts (i) again.