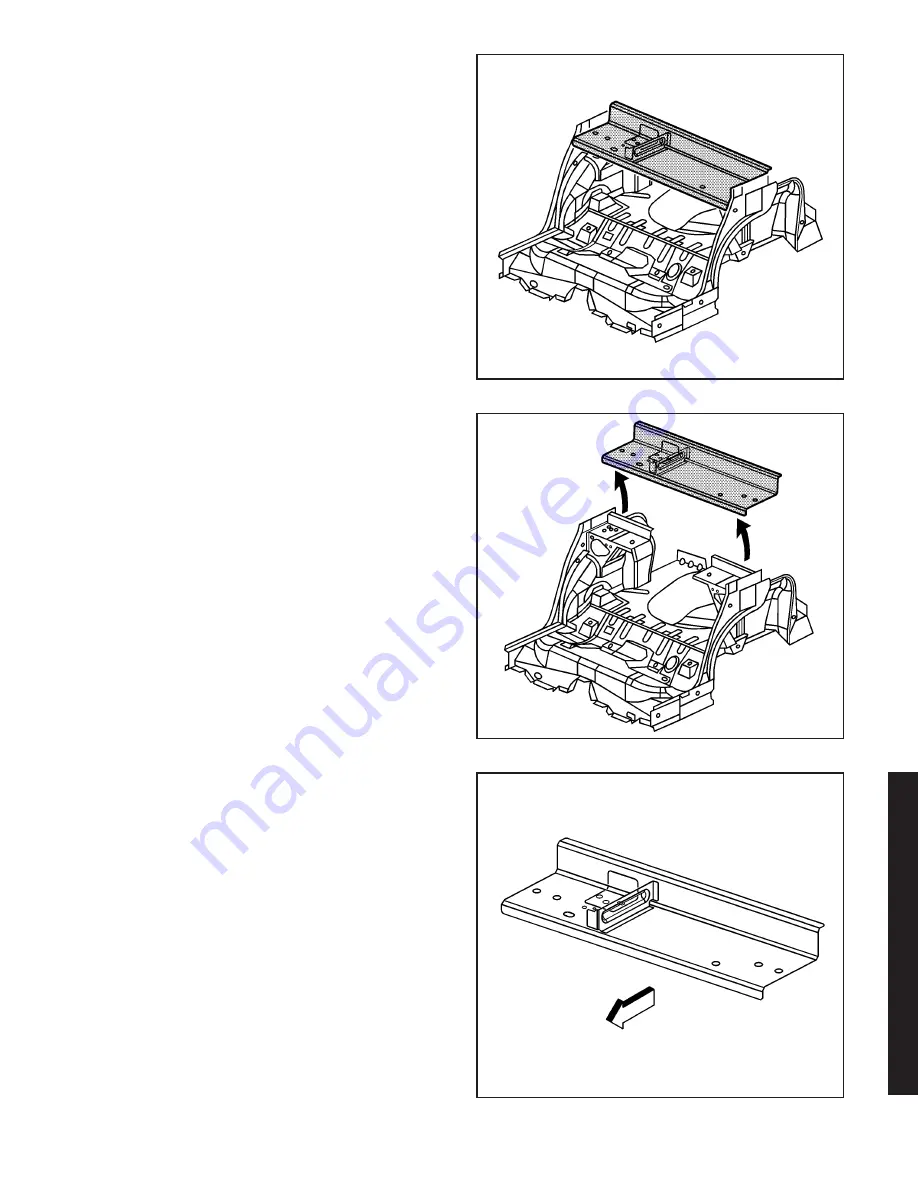
Important: Note the number and location of the
factory welds for installation of the rear window
reinforcement.
6. Locate and drill out all the necessary
factory welds.
7. Remove the rear window reinforcement.
Installation Procedure
Important: If the location of the original plug weld
holes can not be determined, space the plug
weld holes every 40 mm (1 1/2 in) apart.
1. Drill 8 mm (5/16 in) plug weld holes in the service
part as necessary in the locations noted from the
original panel.
2. Prepare all mating surfaces for welding as
necessary.
3. Apply 3M Weld-Thru Coating P/N 05916 or
equivalent to all mating surfaces.
872697
872699
872696
2003 Saturn Ion
3-115
2003
Saturn
Ion
Содержание 2003 Ion
Страница 10: ...Underbody 876938 3 10 2003 Saturn Ion...
Страница 13: ...Sedan Side 876943 2003 Saturn Ion 3 13 2003 Saturn Ion...