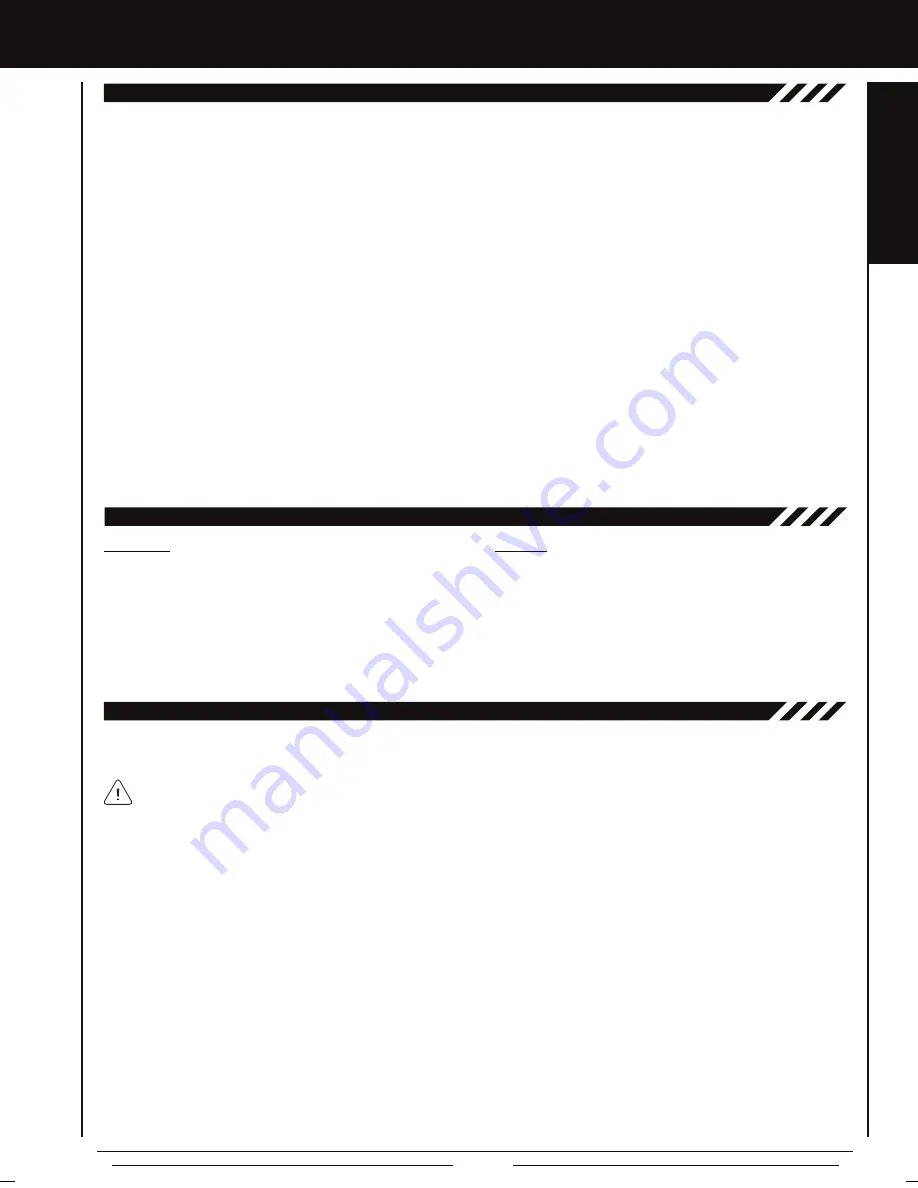
Page 5
Transmitter
Model: MT-4 Telemetry System
Output Power: 100mW
Nominal Input Voltage: 4.8v ~ 7.4v
Operating Voltage Range: 4.0v ~ 9.6v
Dry Weight: 13.68oz (388gr)
Frequency: 2.4GHz FHSS-4T
Receiver
Model: RX-461 Telemetry
Frequency: 2.4GHz FHSS-4T
Nominal Input Voltage: 4.8v ~ 7.4v
Weight: 0.34oz (9.6gr)
Dimensions: 1.43 x 1.04 x 0.64in (36.2 x 26.5 x 16.3mm)
Fail Safe Limit:
3.5v ~ 7.4v (FH4T) / 3.5v ~ 5.0v (FH2/FH3)
Torque: 80oz/in (5.8kg/cm @ 4.8v)
89oz/in (6.4kg/cm @ 6.0v)
Speed: 0.10 sec/60º @ 4.8v
0.08 sec/60º @ 6.0v
Dimensions: 1.59 x 0.83 x 1.04in
(40.4 x 21.1 x 26.4mm)
Weight: 1.77oz (50gr)
Torque: 50oz/in (3.6kg/cm @ 4.8v)
61oz/in (4.4kg/cm @ 6.0v)
Speed: 0.17 sec/60º @ 4.8v
0.14 sec/60º @ 6.0v
Dimensions: 1.54 x 0.79 x 1.42in
(39.1 x 20.0 x 36.0mm)
Weight: 1.55oz (43.9gr)
SDX-901 Digital High-Power Metal Gear Dual Ball Bearing Servo
Torque: 361oz/in (26.0kg/cm @ 4.8v)
423oz/in (30.5kg/cm @ 6.0v)
Speed: 0.19 sec/60º @ 4.8v
0.15 sec/60º @ 6.0v
Dimensions: 1.60 x 0.83 x 1.50in
(40.6 x 21.1 x 38.1mm)
Weight: 2.33oz (66gr)
SDX-1322 Digital Standard Ball Bearing Servo
Both analog and digital servos will work with your
MT-4 2.4GHz FHSS-4T
radio control system. To get the most out of your
experience, we recommend the use of digital servos in SHR or SSR mode. For more information about using different types
of servos and the different Servo Mode Types, see the
Changing the Mode Setting
section on page 55.
Torque: 124oz/in (8.9kg/cm @ 4.8v)
151oz/in (10.9kg/cm @ 6.0v)
Speed: 0.17 sec/60º @ 4.8v
0.13 sec/60º @ 6.0v
Dimensions: 1.54 x 0.78 x 1.50in
(39.0 x 20.0 x 37.4mm)
Weight: 1.93oz (56gr)
SDX-772 Digital High-Power Metal Gear Dual Ball Bearing Servo
We recommend using SANWA brand servos with your
MT-4 2.4GHz FHSS-4T
radio control system. These are a few of our
more popular servos.
4-Channel 2.4GHz FHSS-4T Digital High-Response Computer Radio with Advanced Programming
Telemetry System Features Updated Temperature, RPM/Speed and Voltage Displays in Real-Time on the Telemetry Screen
High-Power FHSS-4T Technology Provides the Best Reception and Connectivity, Giving Racers Added Assurance
4-Cell Battery Holder for Lighter Weight - Also Accepts Optional Ni-Cd/MH Batteries or 2S Li-Po or 2S Li-Fe/A123 Battery Packs
Adjustable Grip
Variable Rate Adjustment
Model Naming
Model Select
Model Select Shortcut (Direct Model)
Model Clear
Selectable Modulation Type
Multi-Function LCD Contrast
Adjustable Key Volume and Tone
Programmable Low Voltage Alarm
Inactivity and Over Voltage Alarms
Digital Battery Voltage Monitor
18 Model Memory
Telemetry Logging
Channel Set Menu
Servo Reversing
Steering, Throttle and Brake Dual Rate
End Point Adjustment
Exponential and ARC Adjustment
Servo Speed Adjustment
Anti-Lock Braking
Throttle Offset
Lap and Interval Timers
Total, Best and Individual Lap Display
Four Wheel Steering Mixing
Dual Throttle Mixing w/Dig & Burn
Normal, SSR and SHR Servo Modes
Center or Parallel Trim Types
Step Auxiliary
Point Auxiliary
Auxiliary Mixing
Programmable Fail Safe
Receiver Battery Voltage Fail Safe
Digital Trims
Servo Sub-Trim
Adjustable Throttle Trigger
Programmable Switches, Lever and Dial
Adjustable Steering Wheel
GENERAL
FEATURES AND SPECIFICATIONS
SYSTEM FEATURES
SYSTEM SPECIFICATIONS
SERVO RECOMMANDATIONS
SDX-801 Digital High Metal Gear Low-Profile Dual Ball Bearing Servo
Содержание MT-4
Страница 1: ...OPERATING MANUAL ...