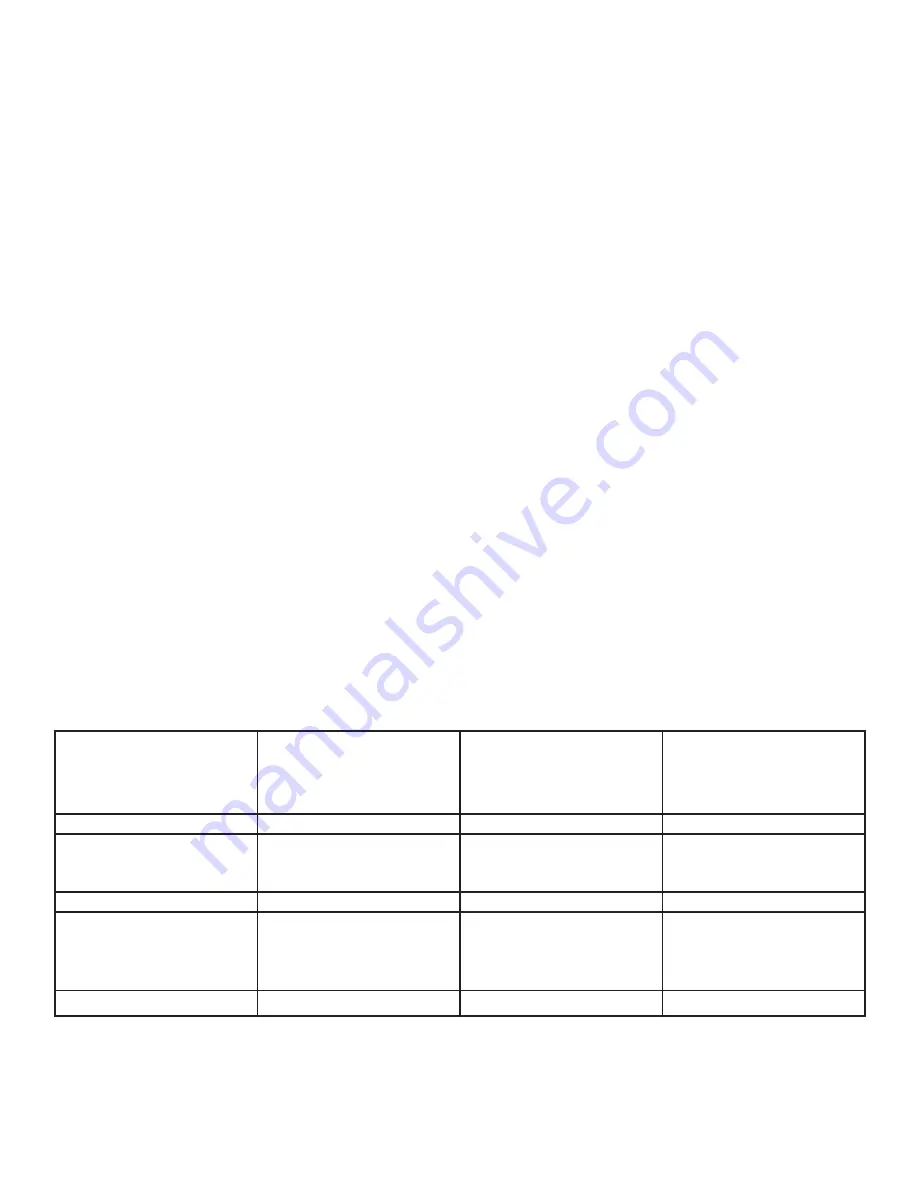
Maintenance Guide
All sensors are shipped from the factory pre-calibrated. To maintain accuracy and conformity with standards it is essential that they be
calibrated by a qualified technician once or twice per year.
Calibration Procedure
Use certified precision mixtures to adjust the sensitivity of the sensor due to normal wear and aging and guarantee that the designed alarm
set points are respected. It will also indicate the general condition of a sensor that is due for replacement. So called “automatic calibration”
or “self-test” will not provide this level of security.
Calibration Procedure for Electro-chemical and Catalytic sensors (CO NO2 CH4 NH3 CL2)
1. Use certified bottled calibration gas mixtures only. Ensure that sensors are powered on for a minimum of the break-in period for the
sensor. For electro-chemical type sensors, this is only a few minutes.
2. Press the right arrow to enter settings
3. Press the
↑
and
→
at the same time to enter calibration mode. SAZ (sensor A zero) will display and the current gas reading on the top
line
4. Inject bottled zero gas into first sensor. Use a flow rate of 0.1 LPM to 1 LPM. The gas fitting to sensor should not be sealed tight. If it is
the pressure will increase and distort the reading (high).
5. Adjust gas reading to zero with the
↑
and
↓
buttons
6. Press
↑
and
←
at the same time to save.
7. Press
→
the display will show SAS (sensor A span) and the current gas reading
8. Inject bottled span gas into first sensor and wait until the gas reading stops going up. The span gas should must be within the range of
sensor’s scale.
9. Adjust the reading to match the concentration in the bottle
10. Press
↑
and
←
at the same time to save
11. If second sensor installed press
→
and repeat steps 4 to 10 for sensor B
12. Press left arrow several times to return to settings and home.
Calibration Procedure for Refrigerant (type 13, 20) and VOC (type 01) sensors
1.0 Use certified bottled calibration gas mixed with air only, not nitrogen. Ensure that sensors are powered on for a minimum of the break-in
period for the sensor. For these types sensors, this is two days.
2.0 Inject bottled span gas
3.0 Adjust the blue potentiometer on the module to set the sensor reading displayed to that of the bottle mix. Do not change the factory
calibration constants in calibration mode as above.
4.0 Remove span gas mix and supply air. Sensor will return to zero.
5.0 If sensor does not return to zero, it needs replacement
BACnet Network Configuration
Setting 46
Bacnet Mode select
0 = communication disabled
1 = communication enabled
2 = communication enabled and display all
sensors on CAN network
0, 1, 2
Default 0
Setting 47
BMA MAC address
0-127
0
Setting 48
Baud rate
0 = 9600
1 = 19200
2 = 38400
3 = 76800
3
Setting 53
Max Master
1-127
127
Setting 54
Diagnostic tool to test MSTP
communication. Format XXXYYZZ where
YY= ID of device that passed token to
current sensor and YY = ID if device that
received token.
Setting 70
Device ID
4,194,304
50,000+BMA