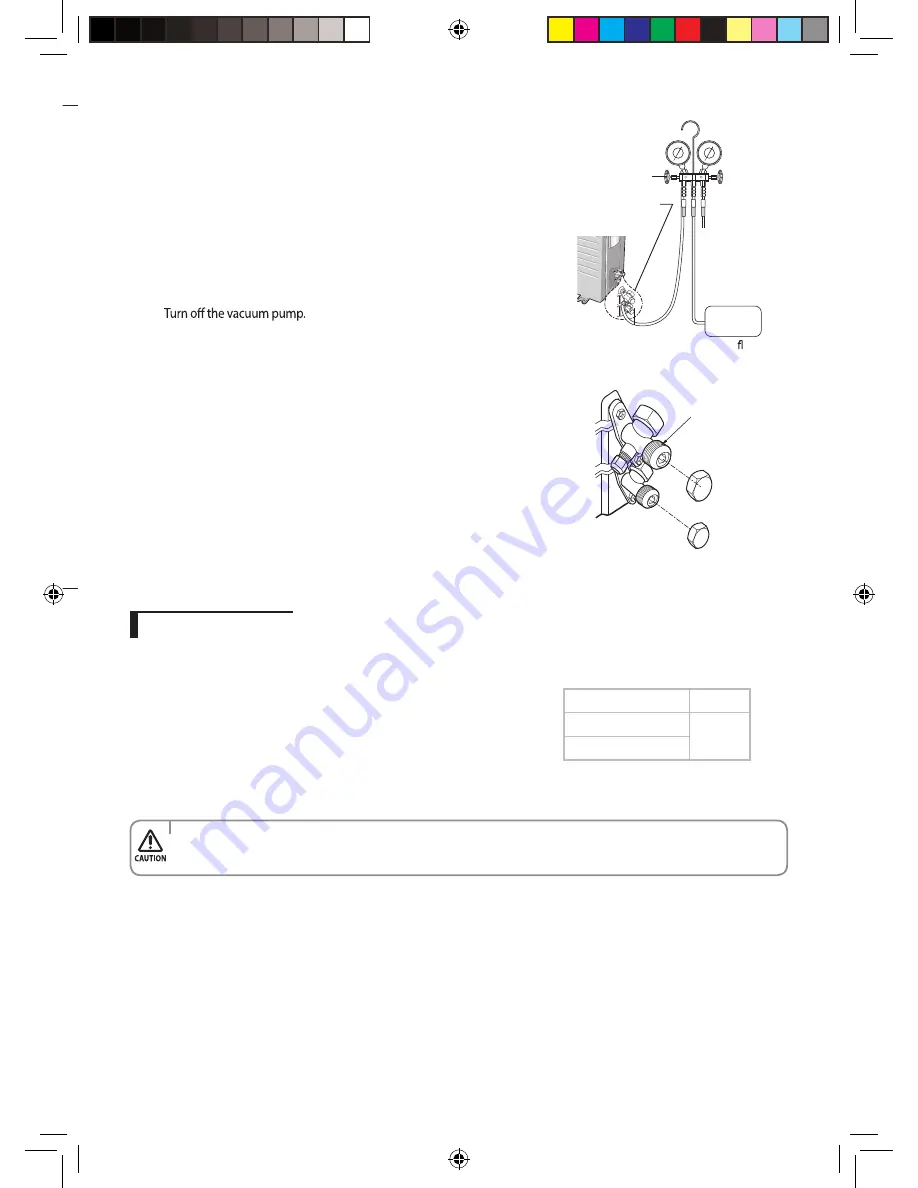
v
k
se t
s
34
3. Connect the charging hose of the low-pressure side of manifold gauge to a
gas service port as seen in the picture.
4. Open the valve of the low pressure side of manifold gauge counterclockwise.
5. Purge the air in the connected pipes using the vacuum pump for about
15 minutes.
Make ure that pressure gauge shows -0.1MPa(-76cmHg) after about
10 minutes.
This procedure is very important to avoid a gas leak.
Clo
he valve of the low pressure side of manifold gauge clockwise.
Chec for 2 minutes if there is any pressure change.
Remo e the hose of the low pressure side of manifold gauge.
6. Set a valve cork of liquid and gas service port to the open position.
7. Mount the valve stem nuts and the service port cap to the valve, and tighten
them at the torque of 183kgf
•
cm with a torque wrench.
8. Check for a gas leak paying particular attention to the 3-way valve’s stem nuts
and to the service port cap (Refer to page 36).
Vacuum
Pump
Manifold gauge
Valve
Gas service port
<Low pressure>
Liquid service port
<High pressure>
(Backward owing
prevention)
•
The remaining air in the Refrigeration cycle, which contains moisture, may cause malfunction on the compressor.
•
Always contact the service center or a professional installation agency for product installation.
Add refrigerant charge according to table below:
If you use a pipe longer than 7.5m,
‘A’g of refrigerant R410A must be added for each extra meter.
If you use a pipe shorter than 7.5m,
The purge time is normal.
Refer to the Service Manual for further details.
Adding Refrigerant
Model
A
18
09/12
15
MAX_XSA_IBIM_DB98-33747A_E.pdf
B
(liquid)
Stem nut
Valve stem
A
(Gas)