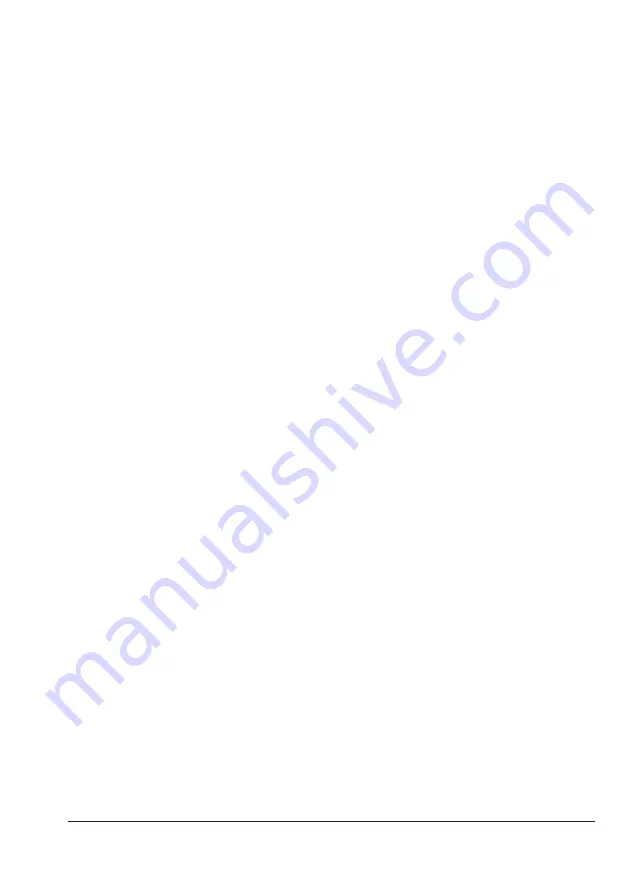
EB 2546-1 EN
23
Installation
Bypass and shut-off valves
−
Install a hand-operated shut-off valve
both upstream of the strainer and down-
stream of the regulator to be able to shut
down the plant for cleaning and mainte-
nance and when the plant is not used for
longer periods of time (see Fig. 7).
−
The bypass ensures that the plant does
not need to be shut down for service and
repair work on the regulator.
Insulation
To insulate cold systems, we recommend first
filling the plant and carefully rinsing it. The
regulator must not yet be insulated at this
stage.
1. Start up the plant and adjust the set
point.
2. Shut down the plant again and let it heat
up until the condensation water has
dried off.
3. Insulate the regulator and pipes convey-
ing the process medium using insulation
material with a water vapor barrier. If
the control line is to be routed through
the insulation, special care must be taken
with the sealing since slight changes in
shape may occur. The insulation thick-
ness depends on the medium tempera-
ture and the ambient conditions. 50 mm
is a typical thickness.
Pressure gauges
−
Install a pressure gauge both upstream
and downstream of the regulator to mon-
itor the pressures prevailing in the plant
(see Fig. 7).
Содержание 36-3
Страница 4: ...4 EB 2546 1 EN ...
Страница 35: ...EB 2546 1 EN 35 ...