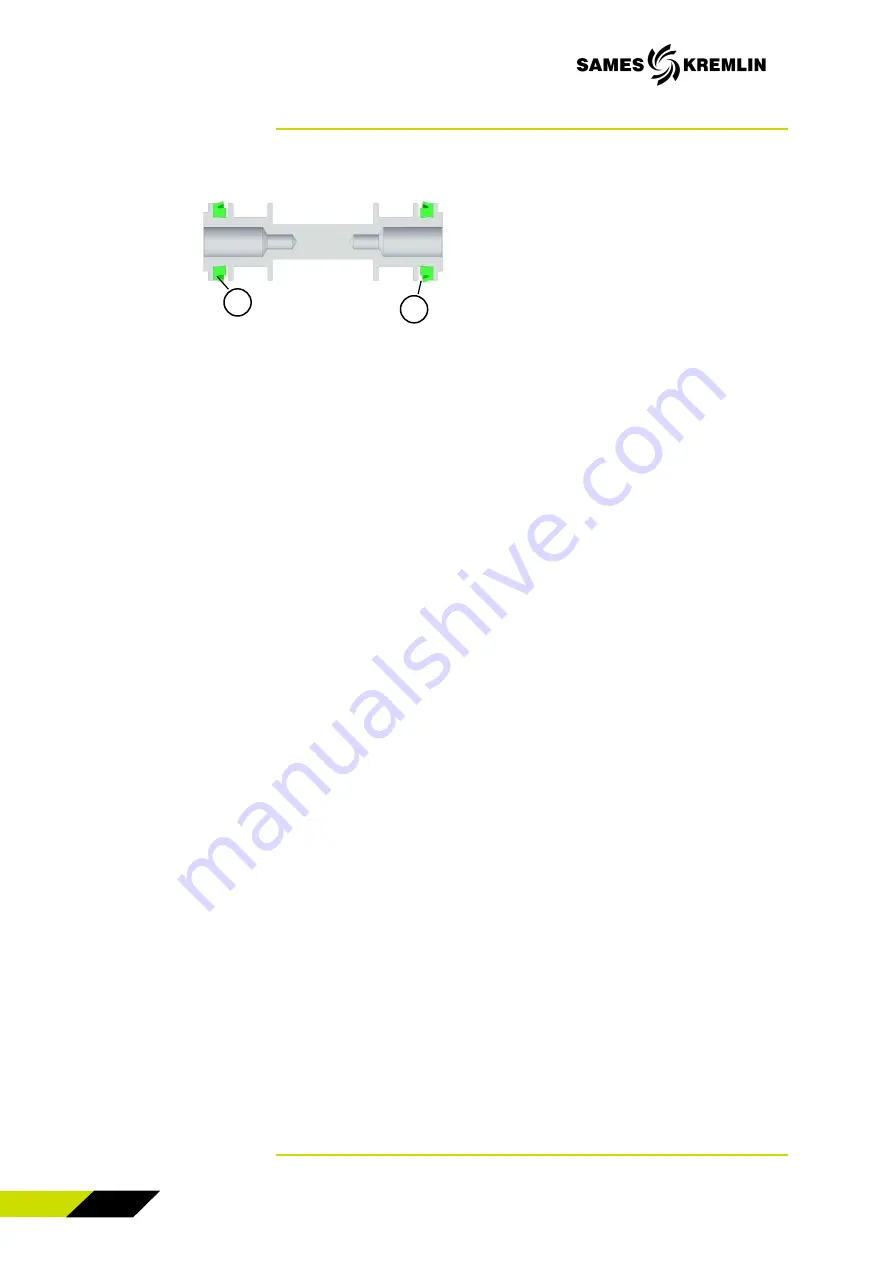
Replacing pump components
26/05/2020
582115110-EN-indC-Pump-01D140-01D140E.docx
52
5. Mount the piston seals (10) on the slide (G) as shown in diagram B.
Figure B
6. Place the slide (G) in the pneumatic valve block (E).
7. Place the O-ring (11) into the outer groove in the pneumatic valve block (E).
8. Insert the O-rings (12) and (13) into the groove of the pneumatic valve block (E).
During assembly, pay attention that the O-rings do not jump out of the grooves and
are damaged.
9. Insert the mounted pneumatic valve block (E) into the centrepiece of the pump.
The mounting direction is clearly shown in figure A.
10. Place the main valve slide (8) with the closed side forward into the pneumatic
valve block (E). The main valve slide (8) must be inserted so that slide (G) is able to
move it.
11.
Place the O-ring (6) in the pneumatic valve block (E).
Pay attention to correct assembly (the side without the O-ring groove first).
12. Place the O-rings (3), (4) and (5) into the grooves provided in the centrepiece of
the double diaphragm pump.
Ensure that the O-rings are not damaged and do not pop out.
13. Place the ceramic plate (17) into the pneumatic valve block (F).
Pay attention to correct assembly (the side with the large O-ring (9) first).
14. Place the O-rings (5) and (6) into the grooves provided in the centrepiece of the
pump.
Ensure that the O-rings are not damaged and do not pop out.
15. Place the intermediate plate (C) in the centrepiece of the pump.
16. Equip the plate (B) with the seal (2) and place the plate (B) in the centrepiece
of the pump.
17. Screw the plate (B) tight using the socket head screws (A).
The socket head screws are to be evenly tightened to a torque of 10 Nm.
10
10
Содержание 01D140
Страница 23: ...Identification 582115110 EN indC Pump 01D140 01D140E docx 26 05 2020 23 Pump model 01D140E...
Страница 29: ...General specifications 582115110 EN indC Pump 01D140 01D140E docx 26 05 2020 29 Dimensions...
Страница 55: ...Spare parts 582115110 EN indC Pump 01D140 01D140E docx 55 12 Spare parts 12 1 Exploded view...