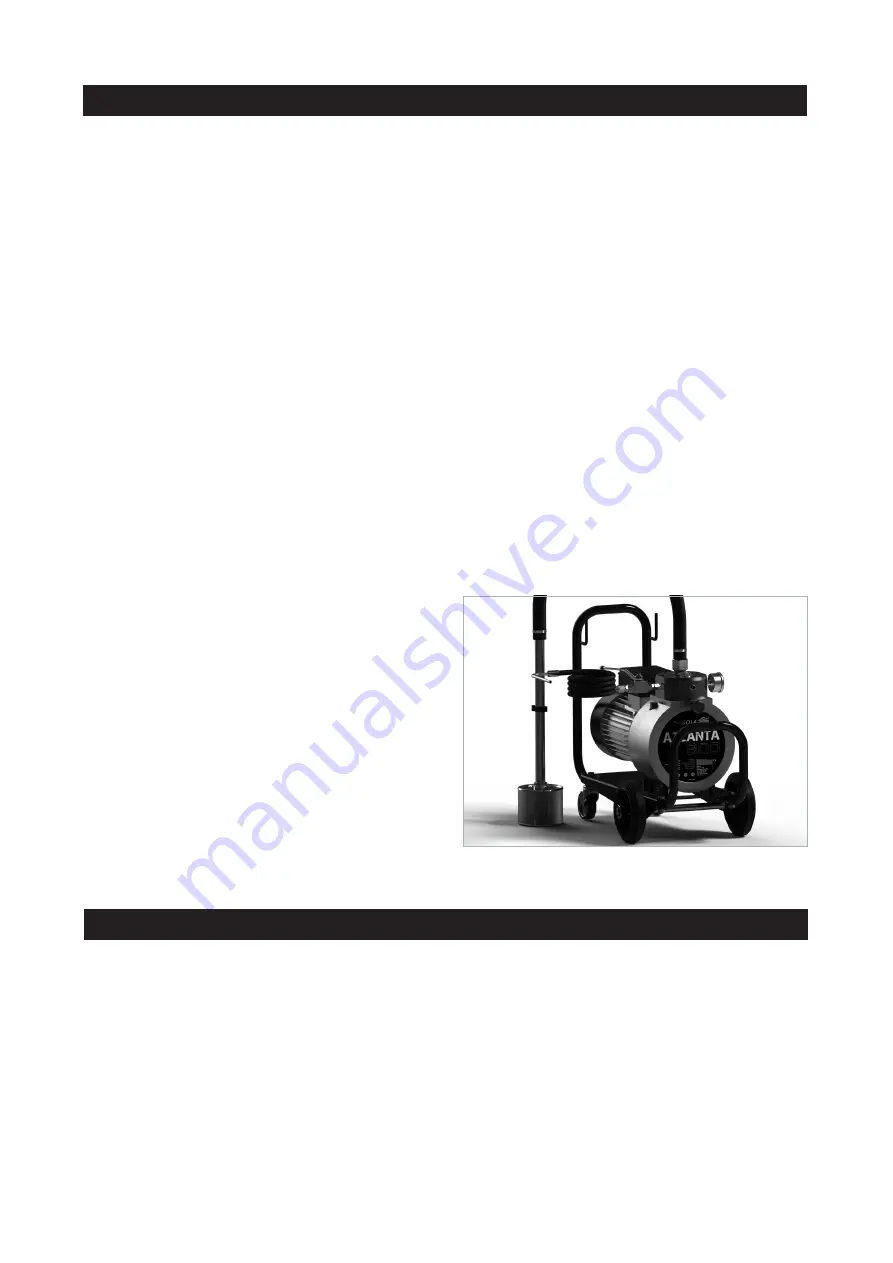
8. START UP
9. DEPRESSURISATION
With the aim of reducing the risk of severe bodily injury,
including the injection of products or injuries caused by
moving parts of the equipment or electric shock, the
procedure described below must be followed as soon as the
system is halted, during assembly, cleaning or changing the
cap and also when spraying is interrupted.
1) Set the gun safety catch.
2) With the equipment, pressurized hose and gun, turn the
pressure regulator (nº 5, Fig. 1) for the equipment to the
minimum setting (anticlockwise).
3) Remove the spray gun safety catch. Holding a metallic
part of the spray gun to the side of a correctly-grounded
bucket, press the trigger to drain the product (aim the jet
toward the side of the bucket) until gauge (No 7 Fig.1)
indicate "0".
4) Set the gun safety catch.
5) Open the product return key (No 4 Fig.1).
6) Turn the pressure regulator (No. 5 fig.1) clockwise until
the product FLOWS SMOOTHLY through the product return
Hose (No. 3 fig.1)
- 19 -
Before each start-up and especially after cleaning or repai-
ring the unit, a check must be made that all its elements are
securely tightened.
The first time you use your equipment there is no need to
depressurise it, as it is already supplied in a totally depres-
surised state, though it will be necessary to do this each
time any maintenance or repair work is carried out.
Should this safety measure not be observed, this may lead
to malfunctions, personal injury and accidents, which may
prove to be fatal. SAGOLA S.A. does not accept any
responsibility for the consequences of any non-compliance
with these safety regulations
Before starting up the equipment, proceed according to the
points given below, in the order in which they are indicated
(if all the specified steps are followed on shutting down the
equipment, it will be in the status referred to below):
1.- Open the product decompression valve (nº4 fig.1), to
drain the equipment.
2.- Set the pressure regulator (nº5, fig.1) to the minimum
position (turn anticlockwise).
3.- Check the product circuit for loose connections.
4.- Remove the product cap from the gun.
5.- Empty the cleaning solvent present in the interior of the
pump, by means of the drain tube (nº3 fig.1). To do this, set
the motor start-up switch to ON. Turn the regulator (nº5
fig.1) gently to the right. Within a few seconds solvent will
begin to run from drain tube (nº3 fig.1).
Collect the solvent issuing from the drain tube in a contai-
ner.
As soon as no more solvent runs out, turn the pressure
regulator to the minimum setting (anticlockwise) and
disconnect the motor by means of the switch (to the setting
“off”).
6.- Insert the suction probe (nº2 fig. 1) into the paint tank. If
the pump has a gravity tank, fill this tank (in accordance
with the quantity required for use). Place the drain tube in
the paint container or in the gravity tank (nº1 fig.1).
7.- Set the motor switch (nº8 fig.1) to the ON position. Turn
the pressure regulator (nº5 fig.1) gently to the right. Within
a few seconds product will run from the drain tube (nº3
fig.1).
Move the pressure regulator again, to the minimum setting.
Close the drain tube stopcock (nº4 fig.1).
8.- Aim the gun towards a properly-grounded container.
Press the trigger on the gun, holding a metallic part of the
gun (the hand protector, for instance) in contact with the
metallic container. Start turning the pressure regulator
once again (nº5 fig.1) gently to the right. Within a few
seconds, product will flow from the head of the gun which
is not fitted with a cap. Maintain the flow of product until this
is even (no air) from the head. Turn pressure regulator (nº5
Fig.1) to the minimum position. Release the gun trigger
and place insurance.
9.- Install the spray cap.
10.- Adjust the spray width:
- Increase the pressure by means of the pressure regulator
(nº5, fig.1) until the product flowing from the gun is fully
atomised. To avoid spraying too great a quantity of
product, which may lead to excessive mist and premature
wear on the cap and other parts of the equipment, always
use the lowest pressure setting possible to obtain the
performance and thickness in microns given by the manu-
facturer of the product.
- Once the atomising pressure for the product has been
determined, if a greater quantity of product is required, it is
preferable to use a cap of greater diameter than to increa-
se the pressure during application.
- To set the shape of the spray width, set the spray gun
safety catch, loosen the cap attachment bolt and turn to the
desired direction. Tighten the cap attachment bolt.