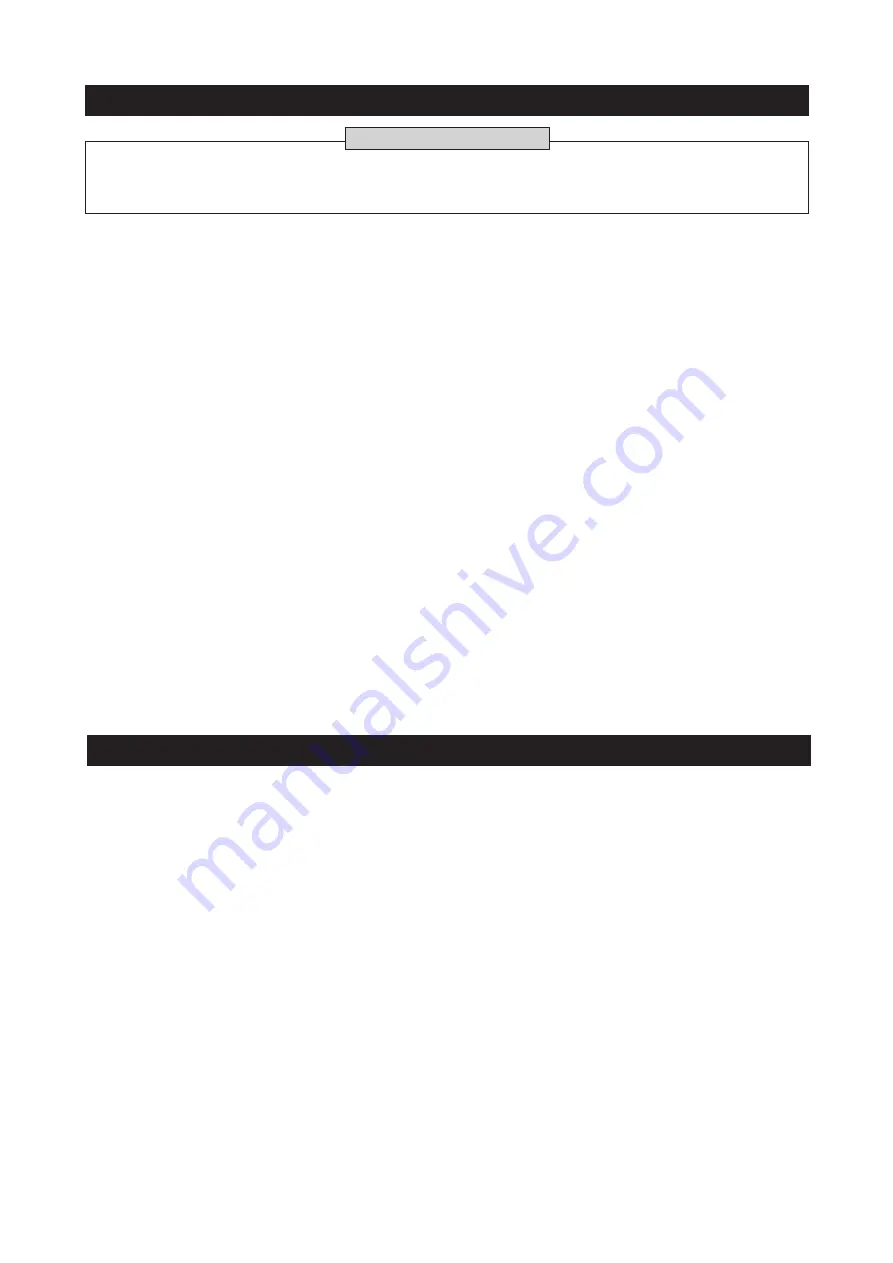
10. OPERATION
Only if the whole process indicated in the section regarding DEPRESSURISATION, described in section 9,
has been correctly carried out will the unit be ready to be started and used again.
The incorrect observance of this Depressurisation process could lead to malfunctions
in the equipment and deterioration of its components.
11. STOPPING
- 20 -
VERY IMPORTANT!!
1.- Power switch (No. 8 Fig.1) starting the electric motor.
2.- With the engine running, Set the pressure regulator (No.
4, figure 1) to the minimum position (turn anticlockwise).
3.- Pull the spray gun trigger, holding it until gauge (No 7
Fig.1) indicate "0".
4.- Set the gun safety catch.
5.- Open the product return key (No 4 Fig.1).
6.- Insert the suction probe (No 2 Fig.1) in the container
having the product to be applied or bear the product cup
(No.1 Fig.1).
7.- Turn the pressure regulator (No. 5 fig.1) clockwise until
the product flows smoothly through the product return
Hose (No. 3 fig.1).
8.- Close the product return key (No. 4 Fig.1).
9.- Turn the pressure regulator (No. 5 fig.1) to set the
desired application pressure, visible in the gauge (No. 7
Fig.1).
10.- Press the trigger on the gun, holding a metallic part of
the gun (the hand protector, for instance) in contact with
the metallic container.
Within a few seconds, product will flow from the head of the
gun which is not fitted with a cap. Maintain the flow of
product until this is even (no air) from the head.
11.- Set the gun safety catch.
12.- Install the air cap.
13.- Adjust the spray width:
13.1- Increase the pressure by means of the pressure
regulator (No.5, fig.1) until the product flowing from the gun
is fully atomised.
To avoid spraying too great a quantity of product, which
may lead to excessive mist and premature wear on the cap
and other parts of the equipment, always use the lowest
pressure setting possible to obtain the performance and
thickness in microns given by the manufacturer of the
product.
13.2- Once the atomising pressure for the product has
been determined, if a greater quantity of product is requi-
red, it is preferable to use a cap of greater diameter than to
increase the pressure during application.
13.3- To set the shape of the spray width, set the spray gun
safety catch, loosen the cap attachment bolt and turn to the
desired direction. Tighten the cap attachment bolt.
During application, the amount of product applied to areas
with difficult access, reduced space, etc. can be reduced
by decreasing the travel distance of the trigger when loose-
ning the grip of your fingers on it.
Adjust the distance between the air cap and the object to
be sprayed (10 / 20 cm.) depending on the same, the
product to be applied and the working conditions, in order
to increase transfer and obtain a reduction in the amount of
mist depending on the air cap used in each case.
11.1. Short stop
When stopping for a short period of time that does not pose
possible problems with catalysation or hardening of the
product inside the unit and accessories, keep the product
suction probe submerged in the product and apply the
procedure of Depressurisation (Section 9).
Set the motor switch (No.8, Fig.1) to the position “O” (off).
Disassemble the air cap and dip it in thinner.
11.2. Stopping when work is finished
11.2.1.- Apply the procedure of Depressurisation (Section
9).
11.2.2.- Disassemble the air cap and dip it in thinner
11.2.3.- Close the product return key. (No. 4 fig.1)
11.2.4.- Place the gun in the product container and press
the trigger to collect the product. Keep pressing the spray
gun trigger and remove the suction probe from the product
container, leaving it exposed to the air.
11.2.5.- Turn the pressure regulator again (No.5, fig.1)
clockwise. Product will start to run from the head of the
gun, stopping after a few seconds. At that moment the
hose and the product-containing area of the gun are empty
of product.
Note: if the equipment is fitted with a gravity tank (No.1,
fig.1), instead of an suction probe (No.2, fig. 1), empty the
contents of the tank through the gun, from the original
container containing the product from the start.
11.2.6.- Turn the pressure regulator (No.5, fig.1) to the
minimum setting (anticlockwise).
11.2.7.- Open the drain stopcock (No.4, fig.1) keeping a
container at hand in which to collect the product.
11.2.8.- Disconnect the motor switch (No.8, fig.1) turning it
to the setting “off”.
Now, the team is ready to proceed immediately to clean it.