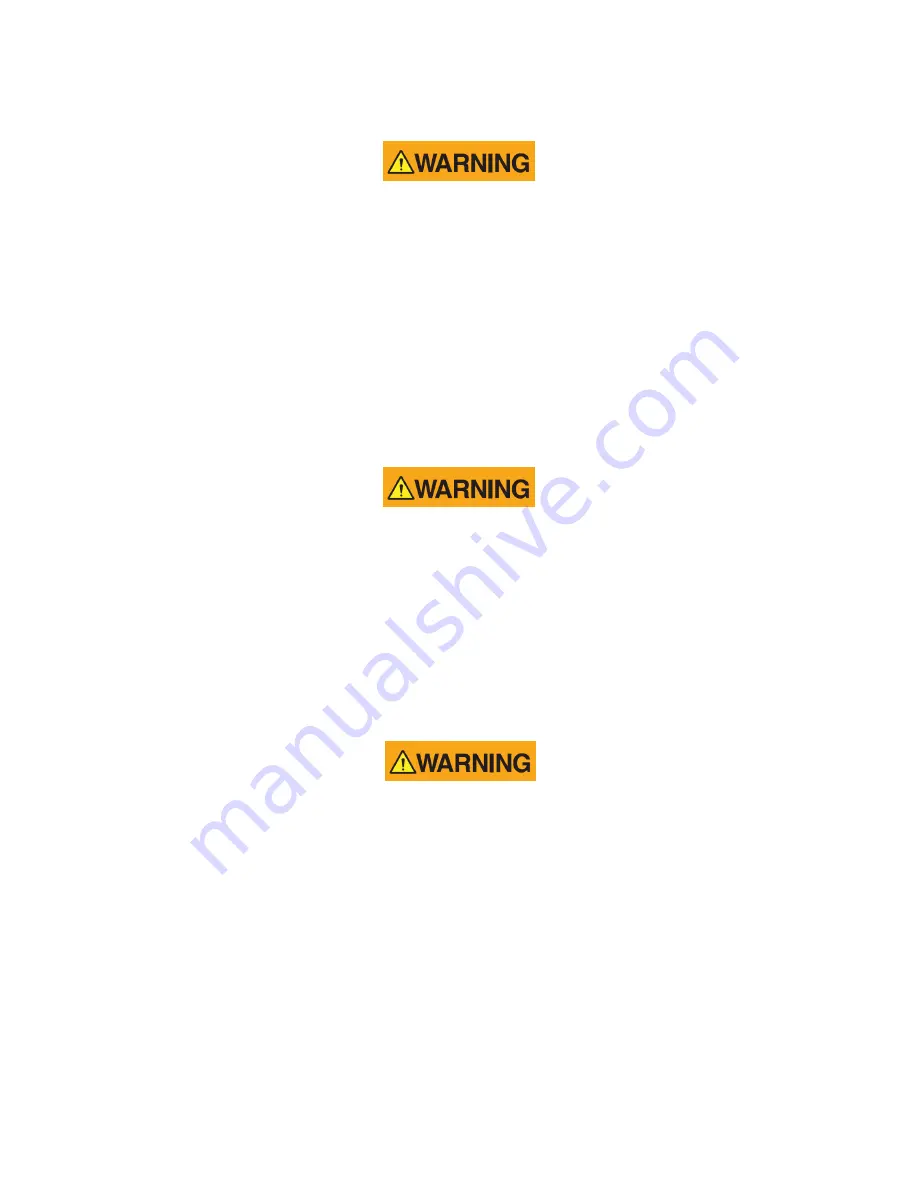
31
1.
Install the appropriate bit into the collet, finger tighten. A Drill Bit should extend approximately 1-
1/4” from the
end of the collet, (Fig. 22). A Router Bit should extend approximately 1-
5/8” from end of collet (Fig. 22).
Tighten Collet. This setting is for motor installation reference only, do not cycle the machine until step 5 is
complete!
Do Not power up or cycle the Screw Pocket Machine until the last step is complete.
2.
Mount the motor into its bracket(s), (Fig. 22) using the appropriate Bit Gauge (Fig. 22) to assist in aligning the
motor in the correct position. Tighten the bolts securing the drill motor and/or router motor.
3.
Position the Bit Gauge (Fig. 22) against the drill mount (Fig. 22) or router mount and confirm the bit is up
against the bottom of the Bit Gauge.
4.
SPM301HD only
. Re-install the air line to the drill motor. Pull back on the collar of the air line fitting. Push
the line into the fitting while twisting slightly. The collar will
“click” into place when the line is seated properly.
5. If the bit(s) are not properly touching the Bit Gauge, loosen the collet nut, reposition bit and tighten the collect
nut securely.
See “Installing a Router Bit” and “Installing a Drill Bit” for detailed bit adjustment instructions.
Always use supplied Bit Gauge (Fig. 22) when installing router or drill motors or bits. Failure to do so
could result in the bits colliding with each other or the machine table when the machine is cycled. If
your guide is missing or damaged contact SSM for a replacement.
Adjusting the Guide Arms
The Guide Arm Adjustment should be checked every 35-40 hours of operation. Bushing tension is correct when
you can rotate the round black or gray nylon bushing by hand, but feel mild resistance.
Unplug tool and disconnect air supply before making adjustments or installing bits. Observe
appropriate Lockout/Tagout procedures to insure the tool cannot accidentally be powered.
1.
Loosen the lock nut (Fig. 23).
NOTE: There are four Nuts, Bolts and Nylon Guides to be checked.
2.
Tighten bolt (Fig. 23) until slight resistance can be felt when rotating the nylon bushing (Fig. 23) by hand.
3.
Tighten nut. When the bushings are properly adjusted you will be able to turn the bushing easily by hand,
but will feel a slight drag. If this is too loose the tool will chatter in the cut. If it is too tight, the machine will
overload and motor life will be shortened. Repeat the above procedure for all four bushings.