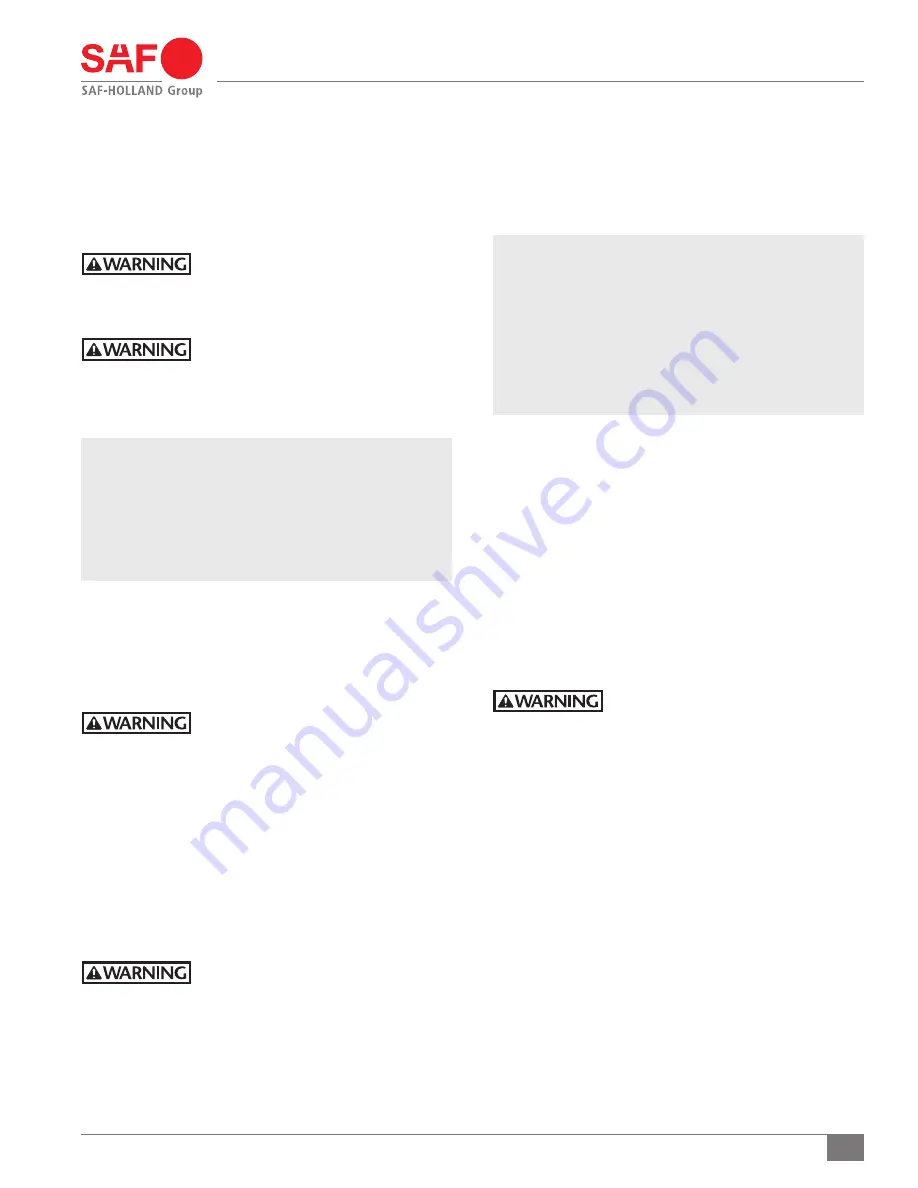
3
XL-AS20067BM-en-US · 2021-02-05 · Amendments and Errors Reserved · © SAF-HOLLAND, Inc., SAF-HOLLAND, HOLLAND, SAF,
and logos are trademarks of SAF-HOLLAND S.A., SAF-HOLLAND GmbH, and SAF-HOLLAND, Inc.
General Safety Instructions
1. General Safety Instructions
Read and observe all Warning and Caution hazard alert
messages in this publication. They provide information
that can help prevent serious personal injury, damage to
components, or both.
Failure to properly support the vehicle and
axles prior to commencing work could
create a crush hazard which, if not avoided,
could result in death or serious injury.
Failure to follow manufacturer’s instructions
regarding spring brake pressure or air
pressure control could allow uncontrolled
release of energy which, if not avoided,
could result in death or serious injury.
NOTE:
In the United States, workshop safety requirements
are defined by federal and/or state Occupational
Safety and Health Act (OSHA). Equivalent laws could
exist in other countries. This manual is written based
on the assumption that OSHA or other applicable
employee safety regulations are followed by the
location where work is performed.
Please observe the following safety instructions in order to maintain
the operational and road safety of the suspension system.
1. The wheel contact surfaces between the wheel and hub
MUST NOT be additionally painted. The contact surfaces
MUST be clean, smooth and free from grease.
Failure to keep wheel and hub contact
surfaces clean and clear of foreign material
could allow wheel/hub separations which,
if not avoided, could result in death or
serious injury.
2. Only the wheel and tire sizes approved by the trailer
builder may be used.
3. Before operating vehicle, ensure that the maximum
permissible axle load is NOT exceeded and that the
load is distributed equally and uniformly.
4. Ensure that the brakes are NOT overheated by
continuous operation.
Failure to minimize the use of brakes during
overheating conditions could result in
deterioration of brake efficiency which, if
not avoided, could result in death or
serious injury.
5. The parking brake MUST NOT be immediately applied when
the brakes are overheated, as the brake drums or discs may
be damaged by different stress fields during cooling.
6. Observe the operating recommendation of the trailer
manufacturer for off-road operation of the installed axles.
IMPORTANT:
The definition of OFF-ROAD means driving
on non-asphalt/non-concrete routes, e.g.
gravel roads, agricultural and forestry tracks,
on construction sites and in gravel pits.
IMPORTANT:
Off-road operation of axles beyond
the approved application design could
result in damage and impair suspension
system performance.
7. All suspension and axles systems require routine service,
inspection and maintenance in order to maintain optimum
performance and operational safety as well as an opportunity
to recognize wear.
8. In the event of suspension air pressure loss, quickly
reduce speed as safely as possible and remove the
vehicle from traffic. If unable to remove vehicle from
traffic, follow DOT safety requirements regarding
emergency situations.
9. Contact a qualified towing and/or service company to
assist in repairing vehicle or to move it to a qualified
repair facility. DO NOT operate the vehicle in the absence
of suspension air pressure.
Operating the vehicle without proper air
pressure can cause tire failure, fire, or loss
of vehicle control which, if not avoided
could result in death or serious injury.
We highly recommend the use of only SAF-HOLLAND
®
Original Parts.
A list of SAF-HOLLAND technical support locations to
supply SAF-HOLLAND Original Parts can be found at
www.safholland.us or contact SAF-HOLLAND Customer
Service at 888-396-6501. Updates to this manual will be
published as necessary on the internet at www.safholland.us.