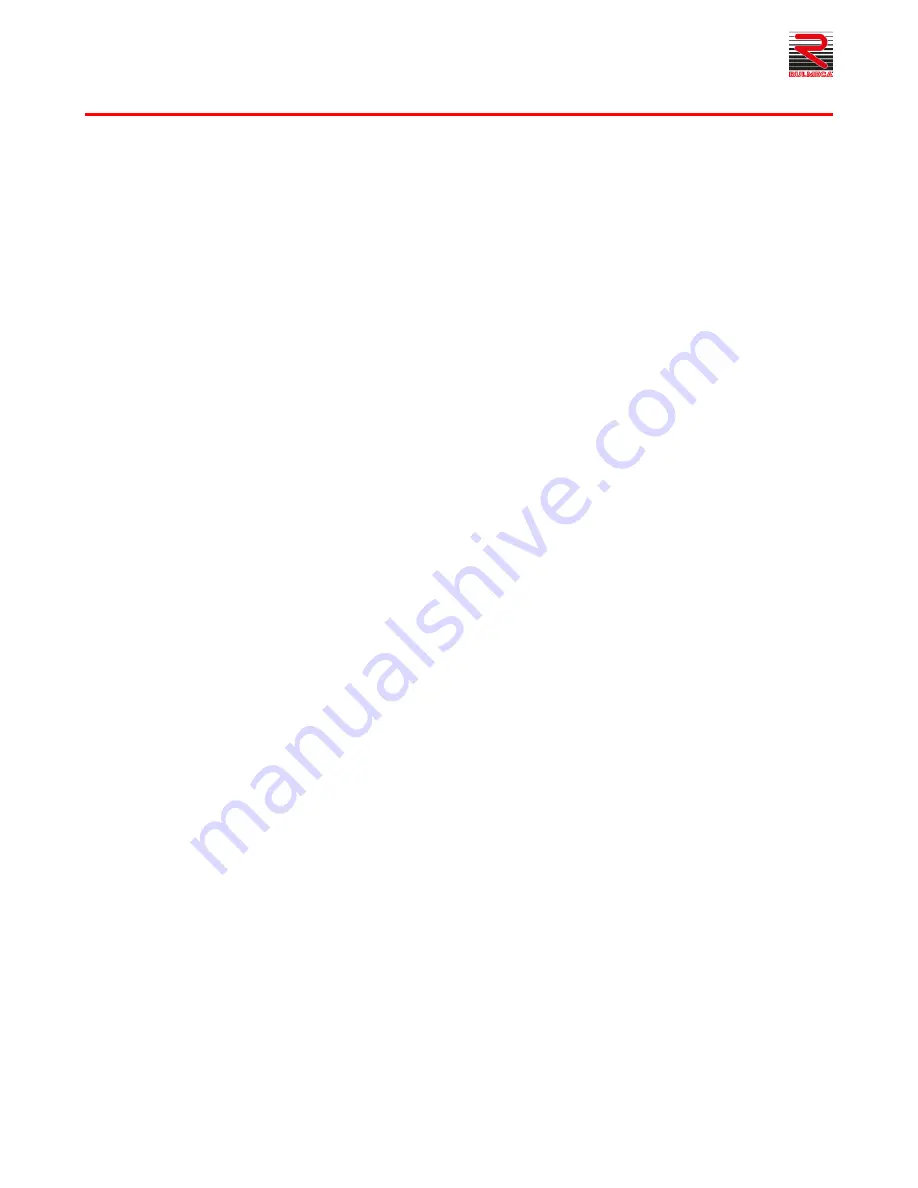
TECHNICAL MANUAL FOR THE RDR BL3 - V1.1 DRIVE ROLLER
Rev. 21/09/2018
page 23
8
WIRING
8.1
Prerequisites:
•
The Drive Roller can also be used without an RMC-BL3 electronic board provided that the following
instructions are adhered to closely.
•
All electrical installation tasks must be performed by authorized and qualified persons.
•
Before electrical installation, the operator must ensure that he works in complete safety.
•
The Drive Roller must be supplied only by 24VDC. NEVER supply it with alternating current.
•
Before connecting the Drive Roller to the power cable or to the I/O lines, disconnect the voltage.
•
When wiring the cable of the Drive Roller, provide an appropriate radius so as not to bend it excessively and
crush it at the outlet of the fixing pin. Drive Rollers returned with pinched, cut or deformed cables are not
covered by warranty
•
Make sure that the roller-bearing structure is properly grounded, functioning and efficient.
•
The formation of electrostatic charges in conveyed packages, if not adequately managed, can generate
malfunctions and/or breakages in the Drive Roller.
8.2
Power supply
A constant and reliable supply is an essential requirement for efficient Drive Roller operation.
Stabilized, good quality and reliable power supply units are ESSENTIAL.
The size of the power supply unit must be evaluated by taking account of the current required for the maximum
number of motors operating simultaneously on the system and of their average current absorbed under the
heaviest conveyed packages.
Approximately:
-
POWER SUPPLY UNIT 5 A
1 Drive Roller
-
POWER SUPPLY UNIT 10 A
3 Drive Rollers
-
POWER SUPPLY UNIT 20 A
6 Drive Rollers
The number of Drive Rollers that can be connected to the individual power supply unit depends on how many
Drive Rollers are active simultaneously and on their average absorbed current. Knowing this and calculating the
current required, the number of Drive Rollers that can be connected to each power supply unit of a certain size
could also be greater than the above number.
Do not forget, in the calculation, to maintain a safety margin if several Drive Rollers start up simultaneously.
The inrush and nominal currents of the Drive Rollers are affected by the weight of the loads conveyed on the
conveyor and by the desired acceleration (if varied by PLC or external equipment).
The power supply unit should be positioned near the Drive Rollers and the supply to the Drive Rollers in the
conductors should not drop below 24V. This could make it necessary to set excessively high voltage beyond the
permitted range so that the voltage reaching the Drive Roller is around 24 VDC.
For conveyors having a considerable length, it is advisable to distribute the power-supply units along the conveyor
line rather than having a single large power supply unit installed in a main electrical cabinet at the start of the line,
and/or far from the Drive Rollers. If the line is long, in order to standardize the power supply to the motors, connect
the power supply in a closed loop at the start and end of the conveyor.
It is preferable to provide a dedicated power line for the Drive Rollers. If this is not possible, make sure that all
appliances with inductive loads that are supplied by the same power supply unit as the Drive Roller (coils of remote
switches and relays) are adequately filtered (RC) by commercially available filters that are very cheap and can be
supplied by the manufacturers of the above appliances.
8.3
Prevention of electromagnetic interference
Electromagnetic interference (EMI) causes radio interference commonly known as "noise" emissions that
adversely affect the performance of the brushless motor and of its driver.
The most effective techniques for limiting EMI comprise filtering the VAC supply, shielding and separating the 24
VDC lines with channels and effective grounding of the channels.
Содержание RDR BL3
Страница 9: ...TECHNICAL MANUAL FOR THE RDR BL3 V1 1 DRIVE ROLLER Rev 21 09 2018 page 9 RIGHT WRONG...
Страница 17: ...TECHNICAL MANUAL FOR THE RDR BL3 V1 1 DRIVE ROLLER Rev 21 09 2018 page 17 7 TECHNICAL DRAWINGS FOR DRIVE ROLLER...
Страница 18: ...TECHNICAL MANUAL FOR THE RDR BL3 V1 1 DRIVE ROLLER Rev 21 09 2018 page 18...
Страница 19: ...TECHNICAL MANUAL FOR THE RDR BL3 V1 1 DRIVE ROLLER Rev 21 09 2018 page 19...
Страница 20: ...TECHNICAL MANUAL FOR THE RDR BL3 V1 1 DRIVE ROLLER Rev 21 09 2018 page 20 TAMPERED DRIVE ROLLERE FOR CURVES...
Страница 21: ...TECHNICAL MANUAL FOR THE RDR BL3 V1 1 DRIVE ROLLER Rev 21 09 2018 page 21...