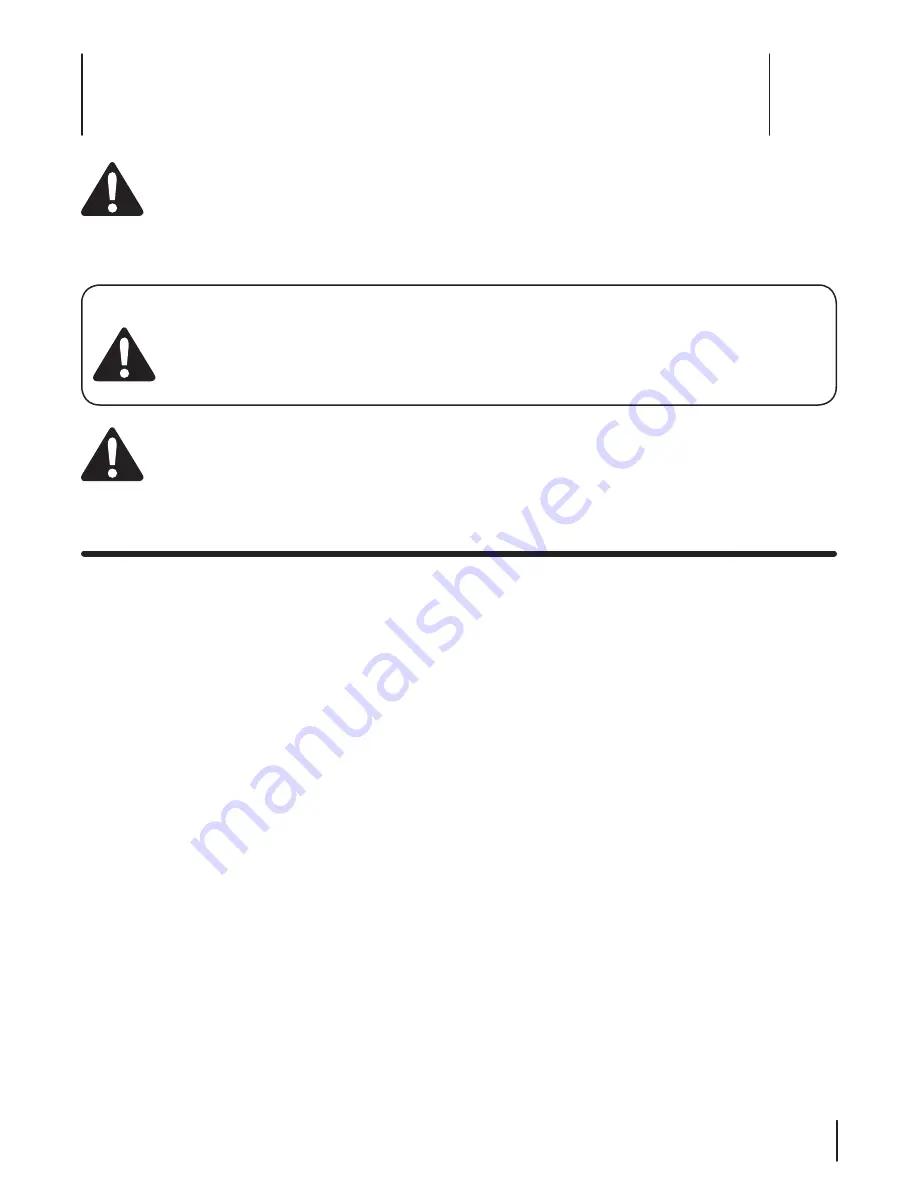
Important Safe Operation Practices
2
3
Training
1.
Read, understand, and follow all instructions on the
machine and in the manual(s) before attempting to
assemble and operate. Keep this manual in a safe place for
future and regular reference and for ordering replacement
parts.
2.
Be familiar with all controls and their proper operation.
Know how to stop the machine and disengage them
quickly.
3.
Never allow children under 16 years of age to operate this
machine. Children 16 and over should read and understand
the instructions and safe operation practices in this manual
and on the machine and be trained and supervised by an
adult.
4.
Never allow adults to operate this machine without proper
instruction.
5.
Many accidents occur when more than one person
operates the machine. If a helper is assisting in stacking
logs, never activate the control until the helper is a
minimum of 10 feet from the machine.
6.
Keep bystanders, pets, and children at least 10 feet from
the machine while it is in operation.
7.
Never allow anyone to ride on this machine.
8.
Never transport cargo on this machine.
9.
Hydraulic log splitters develop high fluid pressures during
operation. Fluid escaping through a pin hole opening can
penetrate your skin and cause blood poisoning, gangrene,
or death. Give attention to the following instructions at all
times:
a. Do not check for leaks with your hand.
b. Do not operate machine with frayed, kinked,
cracked, or damaged hoses, fittings, or tubing.
c. Stop the engine and relieve hydraulic system
pressure by cycling the valve control lever from
forward to reverse several times while engine is
not running; returning to neutral before repairing
or adjusting fittings, hoses, tubing, or other system
components.
d. Do not adjust the pressure settings of the pump or
valve.
10. Leaks can be detected by passing cardboard or wood,
while wearing protective gloves and safety glasses, over
the suspected area. Look for discoloration of cardboard or
wood.
11. If injured by escaping fluid, see a doctor immediately.
Serious infection or reaction can develop if proper medical
treatment is not administered immediately.
12. Keep the operator zone and adjacent area clear for safe,
secure footing.
WARNING!
This symbol points out important safety instructions which, if not followed,
could endanger the personal safety and/or property of yourself and others. Read and follow
all instructions in this manual before attempting to operate this machine. Failure to comply
with these instructions may result in personal injury.
When you see this symbol.
HEED ITS WARNING!
DANGER!
This machine was built to be operated according to the safe operation practices in
this manual. As with any type of power equipment, carelessness or error on the part of the
operator can result in serious injury. This machine is capable of amputating hands and feet
and throwing debris. Failure to observe the following safety instructions could result in
serious injury or death.
CALIFORNIA PROPOSITION 65
WARNING!
Engine Exhaust, some of its constituents, and certain vehicle components
contain or emit chemicals known to State of California to cause cancer and birth defects
or other reproductive harm.
Содержание LS 33T
Страница 21: ...Notes 10 21 ...
Страница 22: ...22 Section 10 Notes ...
Страница 23: ...23 Section 10 Notes ...