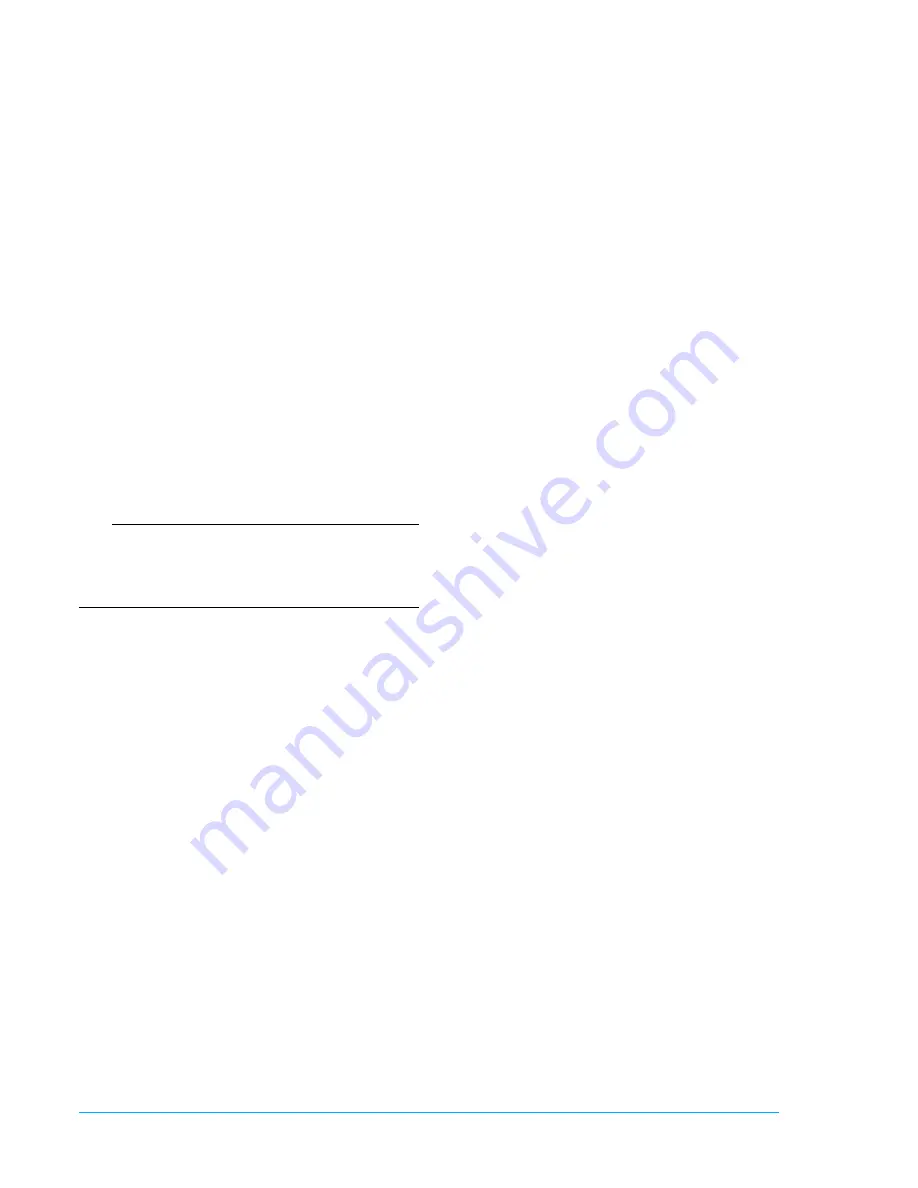
ROTORCOMP VERDICHTER
Operating Manual - NK 100
6.2
[en] 09/2008
6.4 Recommissioning screw compressor
system
Screw compressor systems switched off, shut-
down or stored for longer than three months can-
not be put into operation again until after the fol-
lowing measures have been carried out:
– Rotate the screw compressor in the direction of
rotation several times by hand.
– With the screw compressor system at a com-
plete stop, fill approx. 0.2 liters of oil (same oil
type as in the oil separator tank) into the oil
intake hole with a syringe.
– On models with a transmission, pour 0.25 liters
of oil into the transmission via the oil filler open-
ing.
– Rotate the screw compressor again in the
direction of rotation several times by hand.
– Check the oil level in the separator tank and top
up if necessary (see chapter 7 "Maintenance").
– Test the running check function for the screw
compressor system for at least 15 minutes.
d
Warning:
The system may not be started with the feed
chamber completely filled. There is a danger of
considerable damage.
Содержание NK 100
Страница 1: ...Operating Manual SCREW COMPRESSOR COMPACT MODULE NK 100 NK 100 G en 09 2008...
Страница 24: ...ROTORCOMP VERDICHTER Operating Manual NK 100 3 16 en 09 2008...
Страница 44: ...ROTORCOMP VERDICHTER Operating Manual NK 100 8 4 en 09 2008...
Страница 50: ...ROTORCOMP VERDICHTER Operating Manual NK 100 10 4 en 09 2008...
Страница 51: ......