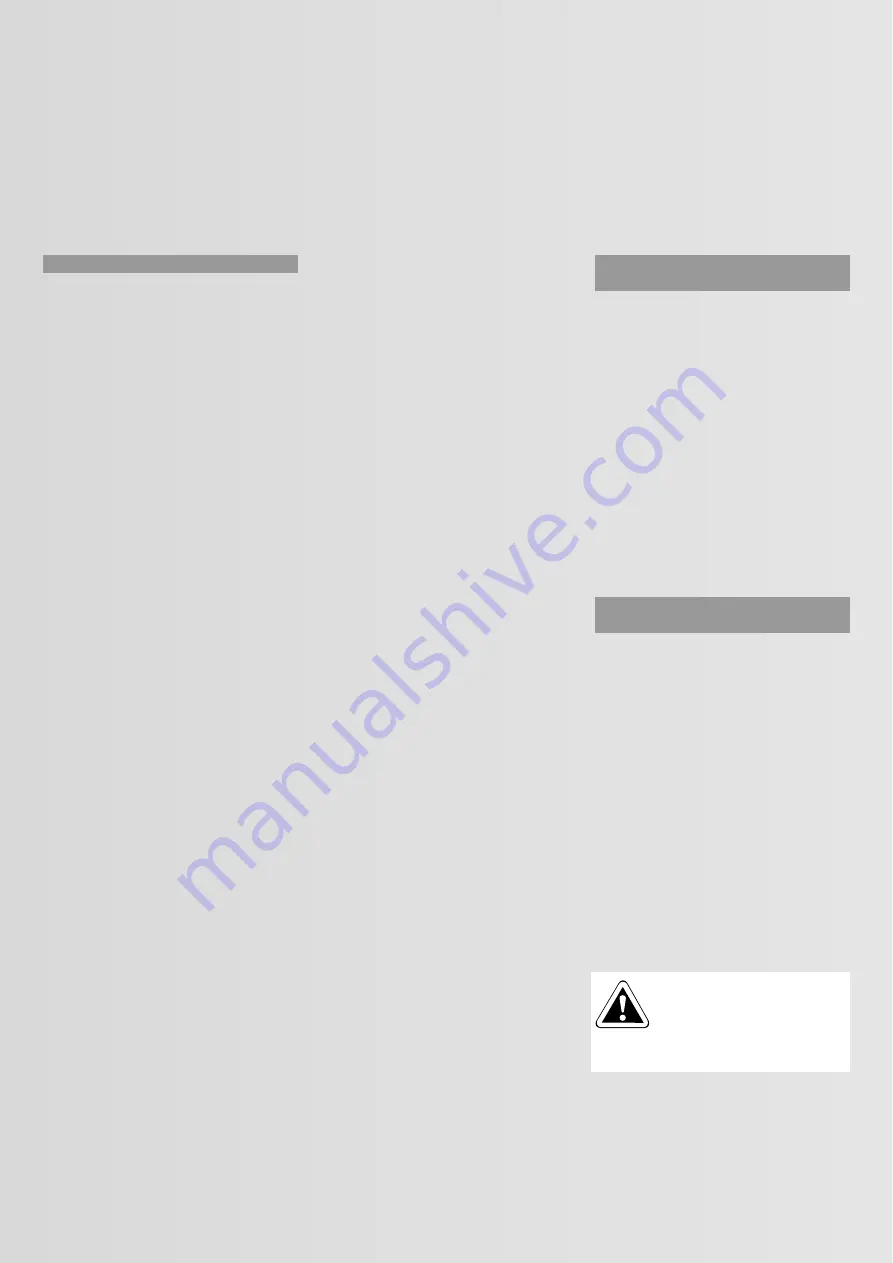
Gas type conversion
Conversion to natural gas LL, L
• To enable a reliable start of a burner that is,
as standard adjusted to natural gas E/H,
with natural gas LL/L, first open the mixer
adjusting screw (pos. 11) one turn anti-
clockwise.
• Then adjust the gas volume as described
above, so that the O
2
or CO
2
content shown
in Fig. 5.1.7 (GSU 25/GCU 25) or Fig. 5.1.8
(GSU 35/GCU 35) will be maintained.
• Enter the conversion to a different gas type
and the selected thermal load (see Fig. 8.4.)
on the adjustment label below the type plate
on the equipment front and confirm the
work by signature.
• Affix the equipment label for the LL/L gas
adjustment supplied to the burner fan
casing.
Converting from LPG to natural gas
• To ensure the correct function and reliable
starting of a burner, set as standard to LPG,
with natural gas, first remove the brass
restrictor inserted between the safety gas
pressure governor (pos. 3) and the Venturi
nozzle (pos. 8).
• For this, remove the Venturi nozzle from the
burner fan (possible with the burner
installed); then remove the three screws
that secure the Venturi nozzle on the gas
governor. Remove the restrictor and
re-assemble the burner in reverse order.
• Initially close the mixture adjusting screw
(pos. 11) one turn clockwise.
• Then adjust the gas volume as described
above, so that the O
2
or CO
2
content shown
in Fig. 5.1.7 (GSU 25/GCU 25) or Fig. 5.1.8
(GSU 35/GCU 35) will be maintained.
• Enter the conversion to a different gas type
and the selected thermal load (see Fig. 8.4.)
on the adjustment label below the type plate
on the equipment front and confirm the work
by signature.
• Affix the equipment label for the natural gas
or natural gas LL/L adjustment (request the
label from ROTEX) to the burner fan casing.
[ 40 ]
Limiting the maximum burner output
The maximum burner output can be limited at
the boiler control panel by entering an
appropriate parameter. After entry of the
contractor access code, the maximum speed of
the burner fan (subject to output) can be
adjusted at the “Burner control unit”
parameter level for heating mode (parameter
2) and DHW heating mode (parameter 3). The
entry is made as a percentage of the rated
equipment output (see operating instructions
for heating contractors “ROTEX control unit”).
This limit may be advisable, for example if the
gas supply company offers a better tariff for
equipment with a lower output rating.
Limiting the minimum burner output
The minimum burner output can be regulated
via the ROTEX THETA 23R control unit by
entering an appropriate parameter. After entry
of the contractor access code, the minimum
speed of the burner fan (subject to output) can
be adjusted at the “Burner control unit”
parameter level (parameter 4). The entry is
made as a percentage of the rated equipment
output (see operating instructions for heating
contractors “ROTEX control unit”).
Raising the minimum burner output may be
advisable, for example, if the flue gas pressure
drop is relatively high, and the flame becomes
unstable at minimum load, or if the flue gas
system calculations will not meet
requirements at partial load.
Important:
Output changes
should be entered on the
adjustments label below the
type plate at the front of the equipment
and should be confirmed by signature.
Содержание GasCompactUnit Series
Страница 17: ... 17 Fig 3 4 3 Flue gas system sets ...
Страница 55: ... 55 ...
Страница 58: ... 58 Fig 8 1 Residual head GSU 25 GCU 25 heating side Fig 8 2 Residual head GSU 35 GCU 35 heating side ...