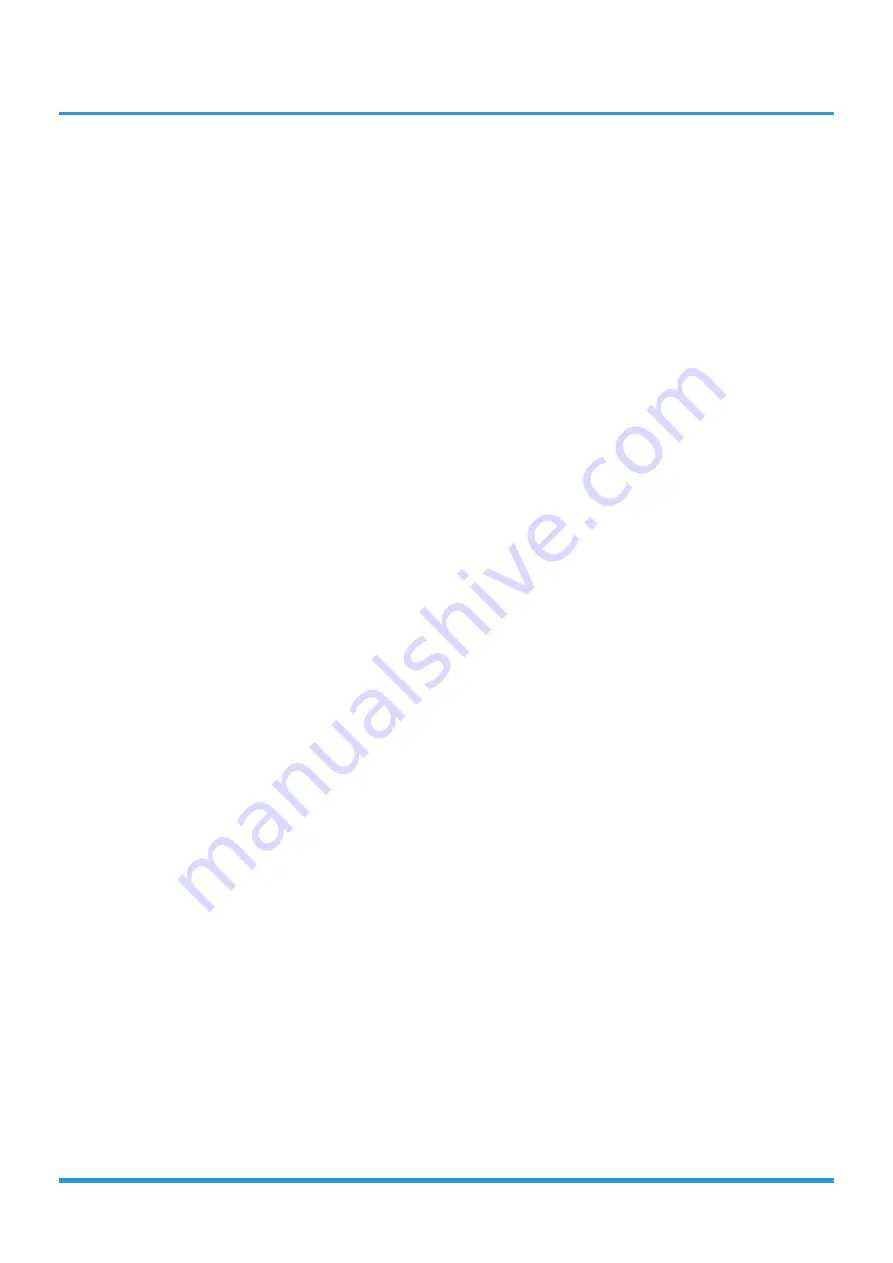
Safety Precautions
5
• The refrigerant charge shall be recovered into the
correct recovery cylinders. The system shall be flushed
with OFN to render the unit safe. This process may
need to be repeated several times. Compressed air or
oxygen shall not be used for this task. Flushing shall
be achieved by breaking the vacuum in the system
with OFN and continuing to fill until the working
pressure is achieved, then venting to atmosphere, and
finally pulling down to a vacuum. This process shall
be repeated until no refrigerant is within the system.
When the final OFN charge is used, the system shall
be vented down to atmospheric pressure to enable
work to take place. This operation is absolutely vital if
brazing operations on the pipe-work are to take place.
• Ensure that the outlet for the vacuum pump is not
close to any ignition sources and there is ventilation
available.
2.16 Charging procedures
• In addition to conventional charging procedures, the
following requirements shall be followed:
• Ensure that contamination of different refrigerants
does not occur when using charging equipment.
Hoses or lines shall be as short as possible to
minimize the amount of refrigerant contained in
them.
• Cylinders shall be kept upright.
• Ensure that the refrigeration system is earthed prior
to charging the system with refrigerant.
• Label the system when charging is complete (if not
already).
• Extreme care shall be taken not to overfill the
refrigeration system.
• Prior to recharging the system it shall be pressure
tested with OFN. The system shall be leak tested on
completion of charging but prior to commissioning.
A follow up leak test shall be carried out prior to
leaving the site.
2.17 Decommissioning
Before carrying out this procedure, it is essential that the
technician is completely familiar with the equipment and
all its detail. It is recommended good practice that all
refrigerants are recovered safely. Prior to the task being
carried out, an oil and refrigerant sample shall be taken.
In case analysis is required prior to re-use of reclaimed
refrigerant. It is essential that electrical power is available
before the task is commenced.
• Become familiar with the equipment and its operation.
• Isolate system electrically.
• Before attempting the procedure ensure that:
• mechanical handling equipment is available, if
required, for handling refrigerant cylinders;
• all personal protective equipment is available and
being used correctly;
• the recovery process is supervised at all times by a
competent person;
• recovery equipment and cylinders conform to the
appropriate standards.
• Pump down refrigerant system, if possible.
• If a vacuum is not possible, make a manifold so that
refrigerant can be removed from various parts of the
system.
• Make sure that cylinder is situated on the scales before
recovery takes place.
• Start the recovery machine and operate in accordance
with manufacturer’s instructions.
• Do not overfill cylinders. (No more than 80 % volume
liquid charge).
• Do not exceed the maximum working pressure of the
cylinder, even temporarily.
• When the cylinders have been filled correctly and the
process completed, make sure that the cylinders and
the equipment are removed from site promptly and all
isolation valves on the equipment are closed off.
• Recovered refrigerant shall not be charged into
another refrigeration system unless it has been cleaned
and checked.
2.18 Labelling
• Equipment shall be labelled stating that it has been de-
commissioned and emptied of
• refrigerant. The label shall be dated and signed. Ensure
that there are labels on the equipment stating the
equipment contains flammable refrigerant.
2.19 Recovery
• When removing refrigerant from a system, either for
servicing or decommissioning, it is recommended good
practice that all refrigerants are removed safely.
• When transferring refrigerant into cylinders, ensure
that only appropriate refrigerant recovery cylinders
are employed. Ensure that the correct numbers of
cylinders for holding the total system charge are
available. All cylinders to be used are designated
for the recovered refrigerant and labelled for that
refrigerant (i.e. special cylinders for the recovery of
refrigerant). Cylinders shall be complete with pressure
relief valve and associated shut-off valves in good
working order.
Содержание ANERU Series
Страница 2: ......
Страница 5: ......
Страница 6: ...Contents 1 Precautions 2 2 Information servicing For flammable materials 3 Safety Precautions...
Страница 12: ...Contents 1 Model Reference 2 2 External Appearance 3 Model Reference...
Страница 15: ...Model Reference 4 2 2 Outdoor Unit Single Fan Outdoor Unit Double Fan Outdoor Unit...
Страница 18: ...IDU Console 3 2 Dimensional Drawings 16 Drain pipe Hanging arm 195 700 600 210...
Страница 21: ...IDU Console 6 6 Air Velocity and Temperature Distributions Discharge Angle 60...
Страница 36: ...IDU Compact Cassette 4 2 Dimensional Drawings...
Страница 38: ...IDU Compact Cassette 6 4 Service Place...
Страница 41: ...IDU Compact Cassette 9 Heating airflow velocity distributions Heating temperature distributions...
Страница 43: ...IDU Compact Cassette 11 Heating airflow velocity distributions Heating temperature distributions...
Страница 45: ...IDU Compact Cassette 13 Heating airflow velocity distributions Heating temperature distributions...
Страница 47: ...IDU Compact Cassette 15 Heating airflow velocity distributions Heating temperature distributions...
Страница 56: ......
Страница 115: ...IDU Super Slim Casstte 54 36k 42k 48k 55k...
Страница 118: ......
Страница 131: ...IDU Duct 7 6 Fan Performance 12K...
Страница 132: ...IDU Duct 8 18K...
Страница 133: ...IDU Duct 9 24K...
Страница 134: ...IDU Duct 10 30K 36K...
Страница 135: ...IDU Duct 11 42K 48K...
Страница 136: ...IDU Duct 12 55K...
Страница 165: ...IDU Duct 41 12k 18k 24k 30k...
Страница 166: ...IDU Duct 42 36k 42k 48k 55k...
Страница 178: ......
Страница 179: ...35mm 1 38in...
Страница 180: ......
Страница 256: ...IDU Floor Ceiling 82 36k 48k 55k...
Страница 259: ......
Страница 267: ...Outdoor Unit 3 Panel Plate B30...
Страница 268: ...Outdoor Unit 4 Panel Plate BA30...
Страница 269: ...Outdoor Unit 5 Panel Plate CA30...
Страница 270: ...Outdoor Unit 6 Panel Plate D30...
Страница 271: ...Outdoor Unit 7 Panel Plate X230...
Страница 272: ...Outdoor Unit 8 Panel Plate X330...
Страница 273: ...Outdoor Unit 9 Panel Plate X430...
Страница 274: ...Outdoor Unit 10 Panel Plate E30...
Страница 275: ...Outdoor Unit 11 Panel Plate 590...
Страница 276: ...Outdoor Unit 12 2 Service Place...
Страница 285: ...Outdoor Unit 21 UO70Xo UO90Xo UO100Xo UO100Xo3F...
Страница 286: ...Outdoor Unit 22 UO120Xo UO140Xo UO160Xo...
Страница 291: ......
Страница 292: ......
Страница 293: ......
Страница 294: ......
Страница 295: ...Outdoor unit printed circuit board diagram 17122000044714 17122000048121 17122000046453...
Страница 297: ...Outdoor unit printed circuit board diagram 17122000048064...
Страница 299: ...Outdoor unit printed circuit board diagram 17122000047742 1 3 4 6 8 9 5 7 10 12 11 2 13...
Страница 302: ...Outdoor unit printed circuit board diagram 17122000041841...
Страница 304: ...Outdoor unit DC motor driver board diagram 17122000021912 5 6 1 2 3 4...
Страница 320: ...3 IDU Installation Duct Connector Connector...
Страница 352: ...Product Features 13 Remote LCD Screen Indicators...
Страница 549: ......
Страница 550: ......
Страница 551: ......
Страница 552: ...email info rotenso com www rotenso com INSTALLER STAMP...