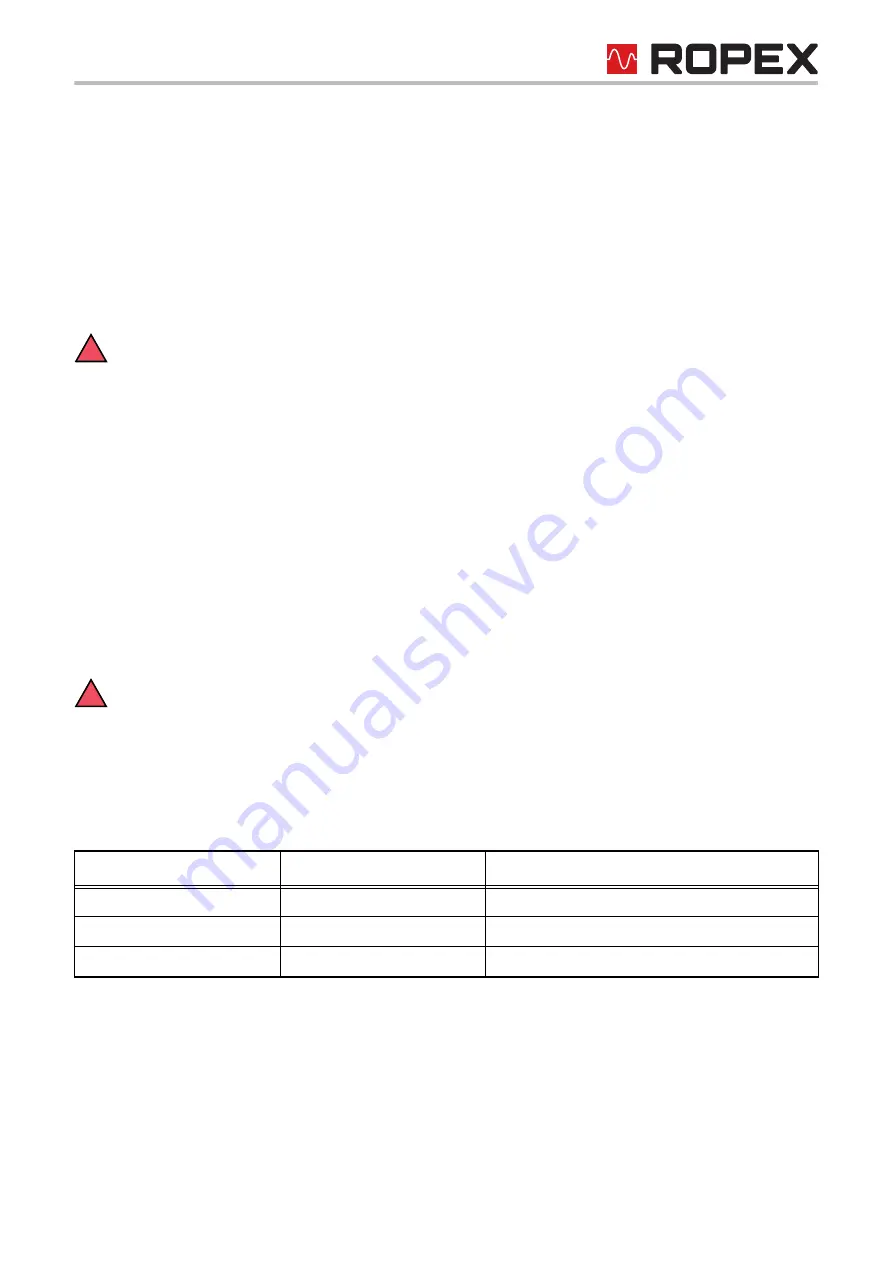
Startup and operation
Version 2
RES-5012
Page 19
Each time the heatsealing band is replaced, you must calibrate the zero point with the AUTOCAL function while
the band (and the environment, i.e. silicone, PTFE cover, sealing bar etc.) is still cold in order to compensate pro-
duction-related resistance tolerances.
If a new heating element is used, the above-described procedure for burning in must be performed.
7.4
Startup procedure
Please also refer to section 2 "General information" on page 3 and section 3 "Use" on page 7.
Mounting, installation and startup may only be performed by authorized persons who have received
suitable instruction and are familiar with the associated risks and warranty provisions.
7.4.1
Initial startup
Condition: The device must be correctly installed and connected (
section 6 "Mounting and installation" on
page 8).
Proceed as follows to start up the controller for the first time:
1. Switch off the line voltage and the 24 VDC supply, and verify that the circuit is de-energized.
2. Link the ESI file into the EtherCAT
®
master (
section 8.3), then select the required parameters, make the con-
nections and start the communication.
3. Make sure that the higher-level controller does not send values not equal to zero to the temperature controller.
4. Switch on the line voltage and the 24 VDC supply (the order is arbitrary).
5. When the voltage is switched on, the yellow "AUTOCAL" LED lights up for approximately 0.3 seconds to indi-
cate that the controller is being powered up correctly. As long as the EtherCAT
®
communication is not active,
neither the "ECAT RUN" LED nor the "ECAT ERROR" LED light up.
If the red "ALARM" LED lights up for 0.3…1.5 seconds when the voltage is switched on in addition
to the yellow "AUTOCAL" LED, the configuration of this controller has been changed in the visual-
ization software (
section 8.12 "USB interface for visualization software ROPEXvisual
order to avoid malfunctions, please check the controller configuration before continuing the startup pro-
cedure.
6. The green "ECAT_RUN" LED lights up to indicate an active EtherCAT
®
communication.
7. One of the following states then appears:
8. Activate the AUTOCAL function while the heatsealing band is still cold by setting the AC bit (
A
UTO
C
AL) in the
EtherCAT
®
protocol (
section 8.4 "Communication protocol" on page 24). The yellow "AUTOCAL" LED lights
up for the duration of the calibration process (approx. 10…15 seconds). The AA bit (
A
UTOCAL
a
ctive) is addi-
tionally set and a voltage of approximately 0 VDC appears at the actual value output (terminals 17+18). If an
ATR-x is connected, it indicates 0…3 °C.
After the zero point has been calibrated, the "AUTOCAL" LED goes out and a voltage of 0.66 VDC (300 °C
range) or 0.4 VDC (500 °C range) appears at the actual value output. If an ATR-x is connected, it must be set
to "Z".
If the zero point was not calibrated successfully, the AL bit (
al
arm active) is set and the red "ALARM" LED blinks
"ALARM" LED
"OUTPUT" LED
ACTION
OFF
Short impulses every 1.2 s
Go to step 8
BLINKS fast (4 Hz)
OFF
Go to step 8
LIT continuously
OFF
Error diagnosis (
section 8.19)
!
!