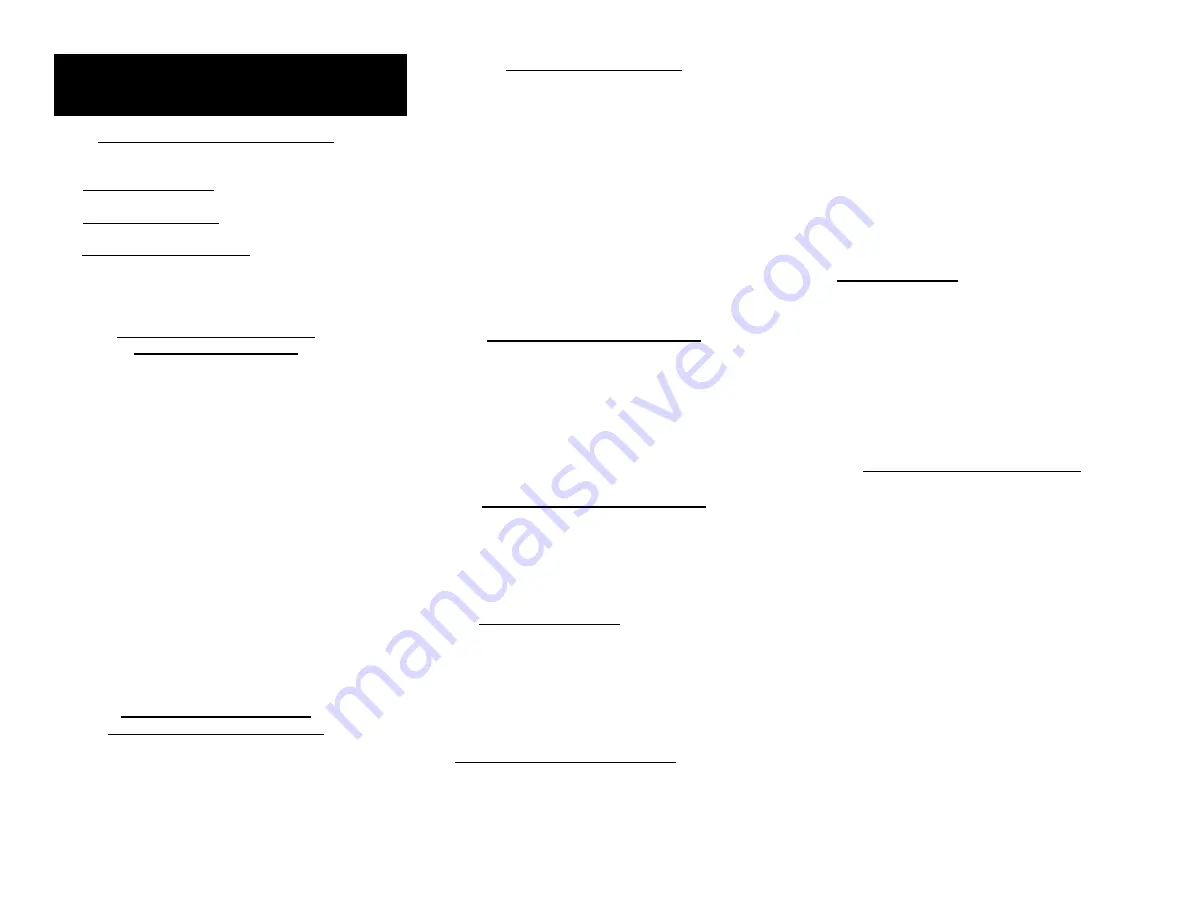
1. SELECT THE PULSE SETTING
Match the control’s pulse mode to the feeder’s
tuning:
A. For 60 pulse output - Set DIP switch (S1) to
60 on the circuit card.
B. For 120 pulse output - Set DIP switch (S1) to
120 on the circuit card.
C. For 40, 30 or 60 Reverse pulse settings, see
the “S1 Programming Chart.”
Note: Readjust the MAX trimpot after changing
pulse switch setting.
2. LIMITING THE MAXIMUM
OUTPUT OF CONTROL
The
MAX
output trimpot can be adjusted to limit
the maximum vibration level of the vibratory feeder
when the Main Control Dial is fully turned up.
When setting up the MAX output of the feeder
control, the output wiring to feeder must be
connected and the control set for the proper pulse
(60 or 120) setting. The Run Jumper must be
connected as shown on the wiring diagram or on
the ON/OFF Control Guide.
A. Power input should be
OFF
or disconnected.
B. Open cover to allow access to circuit card.
C. Adjust the
MAX
Output trimpot counter-
clockwise to its minimum setting.
D. Using
CAUTION
, turn power
ON
(no output
should be present).
E. Rotate the
MAIN CONTROL DIAL
on front
cover clockwise to its highest setting.
F. Adjust the
MAX
Output trimpot so that the
output to the feeder reaches its desired
maximum level.
3. SETTING THE MINIMUM
OUTPUT LEVEL OF CONTROL
When the vibratory feeder is nearly empty, turn the
MAIN CONTROL DIAL
to “1” and adjust the
MIN
trimpot to just below the slowest speed that
provides the proper feed rate. The MIN trimpot
also serves as the “low speed” trimpot for 2-speed
operation. See “S1 Programming Chart” for
feature selection details.
4. MAIN CONTROL DIAL
The output power is controlled by the
MAIN
CONTROL DIAL
. It is a logarithmic-tapered
power out curve (non-linear) that spreads the
power broadly across the
MAIN CONTROL DIAL
The logarithmic taper power curve helps to give
maximum "Fine Control" over the output speed of
the vibratory feeder. When very precise
adjustment of the
MAIN CONTROL DIAL
is
needed, increase the MIN trimpot setting and/or
decrease the MAX trimpot setting. For precise
scaling at low amplitudes, use the linear POT taper
or reduce the Max pot setting. To select a linear
pot taper for the Main Control Dial, see the “S1
Programming Chart.”
5. SETTING THE SOFT-START
The start-up rate of the control output can be
adjusted to ramp up to the desired output level
instead of starting abruptly. Soft-start keeps parts
from falling off the tooling, reduces spring shock,
and hammering when the control turns ON. Turn
the
SOFT
Start trimpot clockwise for the gentlest
start (about a 6 sec. ramp up to full output). Turn
the trimpot fully counter-clockwise for no soft start.
6. REMOTE OFF/ON CONTROL
A Run Jumper has been installed at the factory as
shown on the enclosed wiring diagram.
Remote OFF/ON operation of the FC-40
Plus
Series
Feeder Cube® control can be configured
to operate in one of the following ways.
A. A
low current switch
such as a paddle
switch can replace the factory-installed Run
Jumper "J1." The "Run Contact" connects to
terminals 6 and 7. The contact must be able to
switch 5VDC and 2mA. The control will run
only when the contact is closed. Refer to
Section A of the OFF/ON CONTROL GUIDE.
B.
Feeder Bowl/Hopper Interlock
allows the
Hopper control to operate only when the Bowl
is running and the paddle switch contact is
closed. The
interlock input
on terminals 11
and 12 of TB2 is controlled by the
interlock
output
of a "Parts Sensing Feeder Bowl
Control" such as an FC-90
Plus
.
Remove jumper "J1" of this control from
terminals 6 and 7. Connect the Hopper
Paddle switch to alternate terminals 5 and 6.
Connect TB2 terminals 11 and 12 of this
control to the "Parts Sensing Control". Refer
to Section B of the OFF/ON CONTROL
GUIDE. Check specific instructions for the
"Parts Sensing Control" wiring. Two FC-40
Series controls will not interlock to each other
since neither one has an
interlock output
.
C.
Low Voltage DC
can be used to turn the
control
ON
and
OFF.
Move jumper "J1" from
terminal 7, to terminal 5, (6 remains the
same). Then connect the positive signal (+10
to 30VDC @ 10mA) to terminal 12 and the
negative to terminal 11 of TB2. The control
will now turn
ON
when the DC signal is
present at terminals 11 and 12 of TB2. This
input is optically isolated. Refer to Section C
of the OFF/ON CONTROL GUIDE.
7. REMOTE SPEED CONTROL
Remote control of the power level can be
accomplished by the following methods:
A. 4-20mA signal from a PLC can be used to
remotely vary the output of the control instead of
the Main Control Dial. The 4-20mA input is
automatically in control whenever a 4-20mA
signal is applied to the control (terminals TB2-8
& 9). The Main Control dial setting is ignored
whenever there is a 4-20mA signal. The 4-20mA
input is transformer isolated from the power line.
In an environment with high electrical noise, use
a shielded cable for the 4-20mA signal. The “S1
Programming Chart” shows how change to 0-
20mA speed control instead of the default of 4-
20mA.
B. A 0-5VDC Analog input signal may be applied in
place of the Main Control Dial at H1. The 0-
5VDC input is transformer isolated from the
power line.
CE-41 Plus 24-211 10/16/2012 Page 2
ADJUSTMENTS
& SET UP